Calculating pallet space in a warehouse is crucial for optimizing storage capacity and improving operational efficiency. By accurately measuring and determining the amount of space required for storing pallets, businesses can effectively utilize their warehouse space and ensure smooth operations. In this article, we will delve into the basics of warehouse space calculation, the steps involved in calculating pallet space, common mistakes to avoid, and the tools and software available for accurate space calculation.
Understanding the Basics of Warehouse Space Calculation
Accurate space calculation is the foundation of efficient warehouse management. It involves assessing the dimensions of the warehouse, determining the size and orientation of pallets, calculating the number of pallets per row, and considering aisle space and safety margins. Understanding the importance of accurate space calculation is crucial for maximizing efficiency and minimizing storage costs.
Before we begin: Every Amazon Seller needs a suite of tools for Keyword Research, Product Development, and Listing Optimization. Our top pick is Helium 10 and readers of this post can get 20% off their first 6 months by clicking the image below.
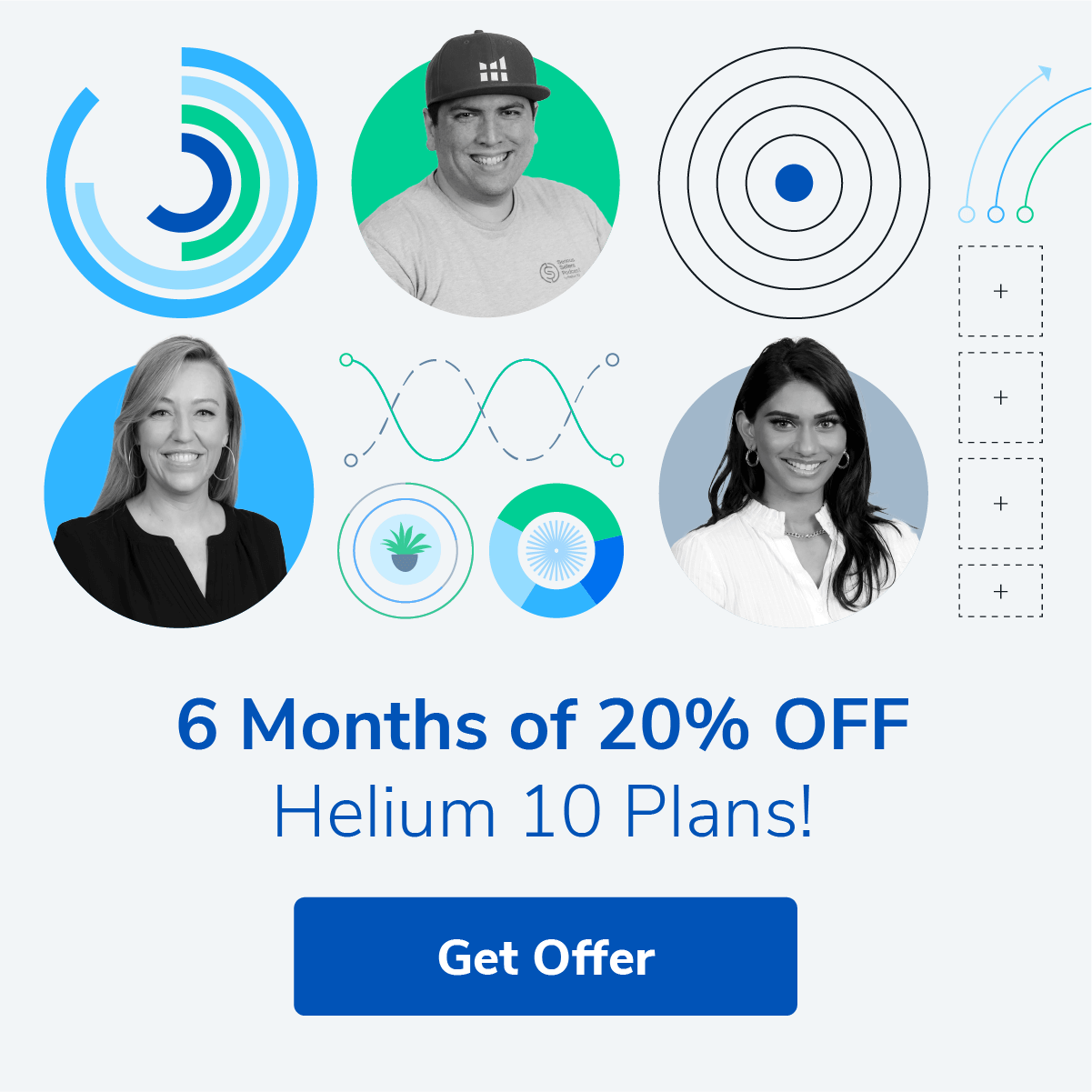
Importance of Accurate Space Calculation
Accurate space calculation allows businesses to optimize their warehouse storage capacity, accommodating the maximum number of pallets while ensuring efficient retrieval. By effectively utilizing available space, businesses can minimize the need for additional warehouses, thereby saving costs. Accurate space calculation also ensures smooth material flow, reducing the time required for order picking and minimizing the risk of errors.
Key Terms and Concepts in Warehouse Space Calculation
Before diving into the steps involved in calculating pallet space, it is important to familiarize ourselves with some key terms and concepts. These include:
- Pallet size: The dimensions of a pallet, typically measured in length, width, and height.
- Pallet orientation: The placement of pallets within the warehouse, either parallel or perpendicular to the aisles.
- Aisle space: The space required for safe maneuvering of forklifts or other material handling equipment in the aisles.
- Safety margins: The additional space allocated to ensure safe movement of personnel and equipment, as well as compliance with safety regulations.
Now that we have a basic understanding of the key terms and concepts in warehouse space calculation, let’s explore the steps involved in accurately calculating pallet space.
The first step is to assess the dimensions of the warehouse. This includes measuring the length, width, and height of the available storage area. By knowing the exact dimensions, businesses can determine the maximum number of pallets that can be accommodated.
Next, it is important to consider the size and orientation of the pallets. Pallets come in various sizes, and it is crucial to choose the right size that fits the available space efficiently. Additionally, the orientation of the pallets, whether parallel or perpendicular to the aisles, can impact the overall storage capacity and material flow within the warehouse.
Calculating the number of pallets per row is another critical step in space calculation. This involves dividing the width of the warehouse by the width of the pallet, taking into account any safety margins required. By determining the number of pallets that can fit in a row, businesses can optimize the storage capacity and ensure efficient retrieval.
Aisle space is an essential consideration in warehouse space calculation. Sufficient aisle space is necessary for the safe maneuvering of forklifts or other material handling equipment. It is important to allocate enough space to ensure smooth operations and minimize the risk of accidents or damage to goods.
Lastly, safety margins play a crucial role in accurate space calculation. These additional spaces are allocated to ensure the safe movement of personnel and equipment within the warehouse. Safety regulations and guidelines should be followed to prevent any potential hazards and maintain a secure working environment.
In conclusion, accurate space calculation is vital for efficient warehouse management. By understanding the key terms and concepts, as well as following the necessary steps, businesses can optimize their storage capacity, minimize costs, and ensure smooth material flow. It is an essential aspect of warehouse operations that should not be overlooked.
Steps to Calculate Pallet Space in a Warehouse
Calculating pallet space involves several steps that need to be followed systematically. Let’s take a look at each step in detail:
Measuring the Warehouse Dimensions
The first step in calculating pallet space is to measure the dimensions of the warehouse. This includes determining the length, width, and height of the available storage area. Accurate measurements are crucial for assessing the maximum number of pallets that can be accommodated.
When measuring the length of the warehouse, it is important to take into account any obstructions such as columns or equipment that may reduce the usable space. Similarly, the width should be measured from wall to wall, considering any protrusions or irregularities that may affect the storage capacity.
The height measurement is particularly important as it determines the vertical space available for stacking pallets. It is essential to consider any height restrictions imposed by the building structure or fire safety regulations.
Determining Pallet Size and Orientation
Once the warehouse dimensions are known, the next step is to determine the size and orientation of the pallets. It is important to consider the standard pallet sizes used in the industry and choose the appropriate size for your specific requirements.
The most common pallet sizes are 48 inches by 40 inches and 42 inches by 48 inches. However, there are also variations such as Euro pallets and custom-sized pallets. The choice of pallet size should be based on factors such as the type of products being stored, the weight-bearing capacity of the pallets, and the compatibility with the material handling equipment used in the warehouse.
In addition to pallet size, deciding whether the pallets will be placed parallel or perpendicular to the aisles is crucial for efficient storage and retrieval. Parallel placement allows for easy access to each pallet, while perpendicular placement maximizes the use of space by creating longer rows.
Calculating the Number of Pallets per Row
After determining the pallet size and orientation, the next step is to calculate the number of pallets that can be accommodated in each row. This calculation is based on the width of the pallets and the available width of the warehouse.
To calculate the number of pallets per row, divide the available width of the warehouse by the width of the pallets, taking into account any aisle space required. It is important to account for aisle space and safety margins while calculating the number of pallets per row.
For example, if the warehouse width is 100 feet and the pallet width is 4 feet, with a required aisle space of 6 feet, the calculation would be as follows:
(100 feet – 6 feet) / 4 feet = 23 pallets per row
It is important to note that the calculation may vary depending on the specific requirements and regulations of the warehouse.
Factoring in Aisle Space and Safety Margins
In addition to calculating the number of pallets per row, it is essential to consider aisle space and safety margins. Aisle space is necessary for safe and efficient movement of forklifts or other material handling equipment.
The width of the aisles should be determined based on the type of equipment used and the maneuverability required. Narrow aisles can maximize storage capacity but may limit the types of equipment that can be used. Wide aisles, on the other hand, provide more flexibility but may reduce the overall storage capacity.
Safety margins ensure compliance with safety regulations and allow sufficient space for personnel and equipment to maneuver. These margins should be determined based on the specific requirements of the warehouse and any applicable safety standards.
By factoring in aisle space and safety margins, the overall pallet space calculation becomes more accurate and ensures a safe and efficient warehouse operation.
Common Mistakes in Warehouse Space Calculation
While calculating pallet space, certain common mistakes should be avoided to ensure accurate results and efficient warehouse management. Let’s take a look at some of these mistakes:
Overlooking Vertical Space
One common mistake is overlooking the vertical space available in the warehouse. Businesses often focus on horizontal space utilization and fail to consider the height of the storage area. By utilizing vertical space effectively, businesses can significantly increase their storage capacity.
Ignoring Pallet Overhang
Another mistake is ignoring pallet overhang. Pallets can often extend beyond their specified dimensions, especially when they contain irregularly shaped or protruding items. Ignoring pallet overhang can lead to inefficient space utilization and could potentially cause safety hazards.
Neglecting Safety and Accessibility Requirements
One crucial aspect that should not be neglected is safety and accessibility requirements. Failing to allocate sufficient space for aisles, safety margins, and safe movement can result in accidents, damage to goods, and operational inefficiencies. It is essential to ensure compliance with safety regulations and prioritize safe and easy access to stored goods.
Tools and Software for Warehouse Space Calculation
Thankfully, there are several tools and software available to assist in accurate warehouse space calculation. These digital tools offer numerous benefits and features that aid in optimizing storage capacity. Let’s explore some of the advantages of using digital tools for space calculation and the key features to look for:
Benefits of Using Digital Tools for Space Calculation
Utilizing digital tools for warehouse space calculation offers several advantages. Firstly, these tools provide precise calculations and eliminate the chances of human error. Additionally, they save time and effort by automating the calculation process. Digital tools also allow for easy scenario testing and optimization, helping businesses make informed decisions.
Features to Look for in Warehouse Space Calculation Software
When choosing warehouse space calculation software, there are certain features to look for to ensure optimal results. These include compatibility with existing systems, ease of use, real-time data updates, dynamic reports and visualizations, and the ability to customize calculations based on specific business requirements.
In conclusion, calculating pallet space in a warehouse is a crucial task that requires careful consideration of various factors. By understanding the basics of warehouse space calculation, following the systematic steps, avoiding common mistakes, and utilizing digital tools, businesses can optimize their storage capacity, improve operational efficiency, and enhance overall warehouse management.
Optimize Your Amazon Warehouse Space with AI
Ready to take your Amazon business to the next level? With Your eCom Agent, you can harness the power of AI to maximize your warehouse efficiency effortlessly. Our tools are designed to streamline your operations, from product development to review analysis and detail page enhancement. Don’t let manual calculations slow you down. Subscribe to Your eCom Agent’s AI Tools today and transform hours of work into seconds of simplicity!