Are you trying to optimize your storage space by calculating how many boxes can fit on a pallet? In this article, we will guide you through the process of determining the maximum number of boxes that can be stacked on a pallet. By understanding pallet dimensions, box sizes, stacking techniques, and safety considerations, you will be able to make efficient use of space and ensure safe transportation of goods.
Understanding Pallet Dimensions
Before you start calculating how many boxes can fit on a pallet, it’s crucial to have a good grasp of pallet dimensions. Pallets come in various standard sizes, which dictate the maximum amount of surface area available for stacking boxes.
Before we begin: Every Amazon Seller needs a suite of tools for Keyword Research, Product Development, and Listing Optimization. Our top pick is Helium 10 and readers of this post can get 20% off their first 6 months by clicking the image below.
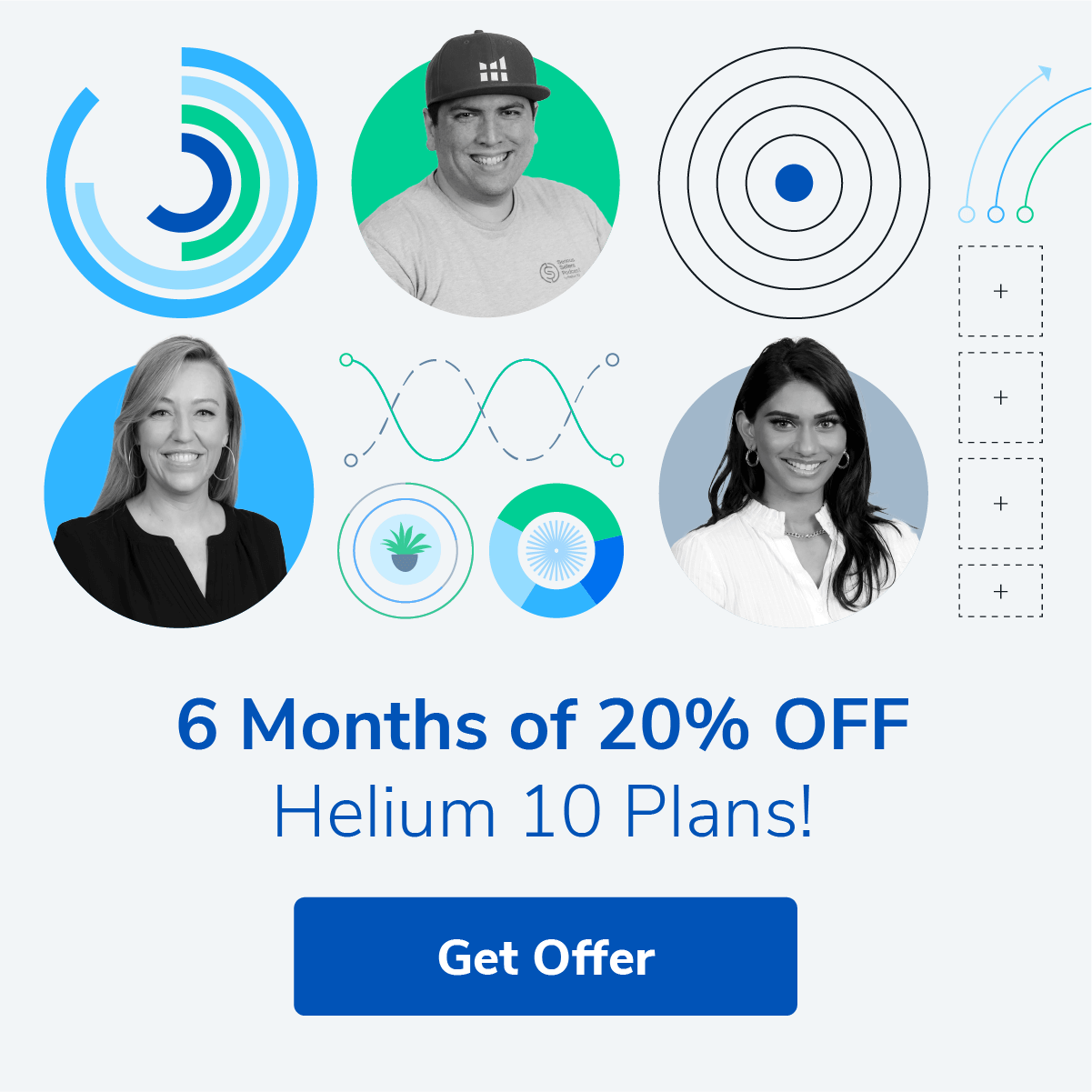
When it comes to pallet dimensions, there are a few common standard sizes that you should be familiar with. One of the most widely used sizes is 48″ x 40″. This size is commonly referred to as a standard pallet and is widely used in many industries. Another popular size is 42″ x 42″, which is often used in the automotive and chemical industries. Additionally, there is the 48″ x 48″ pallet, which is commonly used for heavy-duty applications.
Each of these standard pallet sizes has its own unique characteristics and applications. The 48″ x 40″ pallet, for example, is known for its versatility and compatibility with most warehouse racking systems. It is also the most commonly used size for shipping goods internationally. The 42″ x 42″ pallet, on the other hand, is designed to fit perfectly into the cargo space of many trucks, making it an ideal choice for transportation purposes. The 48″ x 48″ pallet, with its larger surface area, is often used for storing and transporting bulky or heavy items.
Standard Pallet Sizes
Common standard pallet sizes include 48″ x 40″, 42″ x 42″, and 48″ x 48″. These dimensions typically serve as the base for calculating box placement on a pallet.
It’s important to note that while these standard sizes are widely used, there are also custom pallet sizes available. These custom sizes are often designed to meet specific requirements or to accommodate unique products or packaging. Custom pallets can be tailored to fit the dimensions of a specific product, ensuring optimal space utilization and minimizing the risk of damage during transportation or storage.
Importance of Knowing Pallet Dimensions
Knowing the size of the pallet is essential to ensure a secure and stable stacking arrangement. It enables you to determine the maximum number of boxes that can be accommodated while maintaining structural integrity.
By understanding pallet dimensions, you can effectively plan and optimize your warehouse or transportation operations. You can calculate the number of pallets needed for a particular shipment, estimate the storage capacity of your warehouse, and ensure that your products are stacked in a safe and efficient manner.
Additionally, knowing the dimensions of the pallets you are working with allows you to make informed decisions when it comes to packaging and product design. You can design your packaging to fit the pallet dimensions, maximizing space utilization and minimizing wasted space. This can result in cost savings, as you can fit more products on each pallet, reducing the number of pallets required for transportation or storage.
In conclusion, understanding pallet dimensions is crucial for efficient and effective logistics operations. Whether you are calculating how many boxes can fit on a pallet or planning your warehouse layout, having a good grasp of pallet dimensions will help you make informed decisions and optimize your operations.
Basics of Box Dimensions
Now that you have a solid understanding of pallet dimensions, let’s dive into the basics of box dimensions. Box dimensions refer to length, width, and height, which vary depending on the type of box and its intended contents.
Understanding box dimensions is crucial in various industries, including shipping, logistics, and storage. Whether you are a business owner, a warehouse manager, or simply someone who frequently uses boxes for storage or moving, knowing how to measure and choose the right box size can save you time, money, and effort.
When it comes to box dimensions, there are various factors to consider. The size and weight of the items you plan to pack, the available storage space, and the transportation method all play a role in determining the ideal box dimensions.
Common Box Sizes
Common box sizes range from small shipping boxes, such as 12″ x 12″ x 12″, to larger storage boxes, such as 18″ x 18″ x 24″. However, it’s important to note that these are just examples, and box sizes can vary significantly based on specific needs and requirements.
For instance, if you are shipping delicate items that require extra padding and protection, you might opt for a smaller box size to ensure a snug fit and minimize the risk of damage during transit. On the other hand, if you are packing large, bulky items, you would need a box with ample space to accommodate them comfortably.
Choosing the right box size based on the dimensions of your products is crucial. A box that is too small can lead to items being squeezed, potentially causing damage, while a box that is too large can result in items shifting during transportation, increasing the risk of breakage.
Additionally, it’s worth noting that some industries have standardized box sizes to ensure compatibility with automated systems and optimize efficiency. For example, the e-commerce industry often relies on standardized box sizes to streamline the packaging and shipping process.
How to Measure a Box
When measuring a box, always start with the length, followed by the width, and then the height. This order ensures consistency and avoids confusion when communicating box dimensions.
Use a measuring tape or ruler to obtain accurate measurements. Ensure that the measuring tool is straight and aligned with the edges of the box for precise results. Take multiple measurements to double-check accuracy and record the dimensions in a standardized format.
It’s important to note that box dimensions are typically provided in the order of length, width, and height. For example, if you measure a box and obtain dimensions of 10 inches in length, 8 inches in width, and 6 inches in height, the box dimensions would be written as 10″ x 8″ x 6″.
Consistency in measuring and recording box dimensions is essential, especially when dealing with large quantities of boxes or when collaborating with others in the supply chain. Clear and accurate communication of box dimensions ensures that everyone involved understands the size requirements and can plan accordingly.
By understanding the basics of box dimensions, you are equipped with the knowledge to make informed decisions when it comes to choosing the right box size for your specific needs. Whether you are shipping products, storing items, or organizing your belongings, taking into account box dimensions can help optimize efficiency and minimize the risk of damage.
The Concept of Stacking
Now that you have a handle on pallet and box dimensions, let’s explore the concept of stacking. Stacking boxes effectively is key to maximizing the number of boxes that can fit on a pallet.
When it comes to optimizing space utilization, stacking boxes vertically and horizontally are two common methods. Each method has its own considerations and benefits, allowing you to make the most efficient use of your available space.
Stacking Boxes Vertically
When stacking boxes vertically, you need to consider the total height of the stack. It is crucial to ensure that the stack’s height does not exceed the height of the pallet. Leaving enough headspace is essential to prevent damage to the contents of the boxes and maintain stability during transportation.
Moreover, it is important to consider the weight distribution when stacking boxes vertically. Placing heavier boxes at the bottom of the stack and lighter ones on top helps maintain stability and reduces the risk of toppling over.
Additionally, you may want to consider using dividers or separators between layers of stacked boxes. These dividers can provide additional support and prevent shifting or collapsing of the boxes during transit.
Stacking Boxes Horizontally
Stacking boxes horizontally involves arranging boxes side by side on the pallet’s surface. This method is particularly useful when dealing with larger boxes or irregularly shaped items.
When stacking boxes horizontally, it is essential to ensure that the width of the boxes, when combined, does not exceed the width of the pallet. This prevents overhang and maintains stability during transport.
Furthermore, you should consider the weight distribution when stacking boxes horizontally. Placing heavier boxes closer to the center of the pallet helps distribute the weight evenly and reduces the risk of the load shifting during transportation.
It is worth noting that when stacking boxes horizontally, you may want to consider using dunnage or cushioning materials between the boxes. These materials can provide additional protection and prevent damage caused by friction or impact.
By carefully considering the dimensions, weight distribution, and stability of the stacked boxes, you can optimize the use of space on the pallet and ensure the safe transportation of your goods.
Calculating Box Placement on a Pallet
Now that you understand the basics of pallet dimensions and stacking techniques, you can move on to calculating box placement on a pallet. This step involves taking into account box orientation and gap calculation.
The Role of Box Orientation
Box orientation refers to the positioning of the length, width, and height of the boxes in relation to the pallet. It’s important to consider the most efficient orientation that minimizes wasted space and allows for the maximum number of boxes.
The Importance of Gap Calculation
When calculating box placement, it’s crucial to leave small gaps between boxes to provide stability and prevent shifting during transportation. The size of the gap will depend on the fragility of the contents and the method of transportation.
Safety Considerations in Pallet Stacking
Finally, safety is paramount when stacking boxes on a pallet. Understanding weight distribution principles and avoiding overhang are essential to maintain stability and prevent accidents.
Weight Distribution Principles
When stacking boxes on a pallet, distribute the weight evenly to prevent the pallet from becoming top-heavy, which could lead to instability and potential accidents.
Avoiding Overhang
Overhang refers to the portion of a box that extends beyond the edge of the pallet. It’s crucial to avoid overhang as it can compromise stability and pose a safety risk during transportation.
In conclusion, calculating how many boxes can fit on a pallet requires a comprehensive understanding of pallet and box dimensions, stacking techniques, and safety considerations. By following the guidelines outlined in this article, you can make efficient use of space, ensure safe transportation, and streamline your logistical operations.
Maximize Your Pallet Efficiency with Your eCom Agent
Ready to take your Amazon business to the next level? With Your eCom Agent, you can effortlessly optimize your product listings, analyze customer feedback, and enhance your detail pages using the power of AI. Say goodbye to the tedious manual work and hello to efficiency. Subscribe to Your eCom Agent’s AI Tools today and transform how you manage your Amazon operations!