In the world of logistics and shipping, pallets play a crucial role in transporting goods efficiently. When it comes to maximizing the space on a pallet, knowing how many boxes can fit becomes essential. In this article, we will explore the importance of understanding pallet dimensions, box dimensions, stacking techniques, load stability, and introduce a handy tool – the pallet box calculator.
Understanding Pallet Dimensions
Before we dive into the calculations, let’s first familiarize ourselves with standard pallet sizes. Pallets come in various dimensions, but the most common ones are:
Before we begin: Every Amazon Seller needs a suite of tools for Keyword Research, Product Development, and Listing Optimization. Our top pick is Helium 10 and readers of this post can get 20% off their first 6 months by clicking the image below.
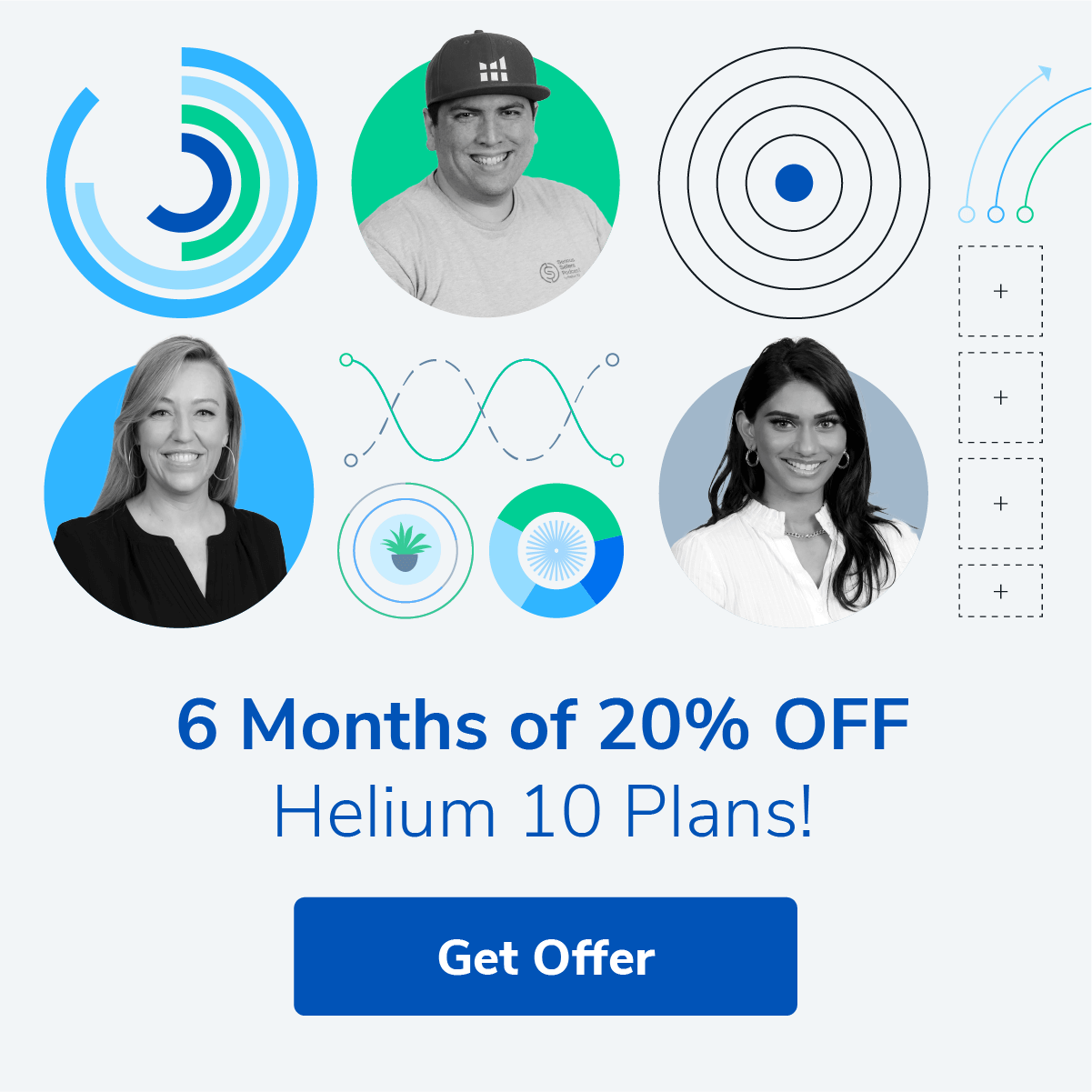
-
Standard Pallet Sizes
The standard pallet sizes vary across regions, but the most prevalent ones include 48″ x 40″ (122cm x 102cm) in the United States and 120cm x 80cm (47″ x 31″) in Europe. These dimensions are widely used in industries such as retail, manufacturing, and logistics.
Standard pallet sizes have been established to ensure compatibility and efficiency in supply chains. The 48″ x 40″ pallet, also known as the GMA pallet, is the most widely used size in the United States. It is designed to fit through standard doorways and is compatible with most forklifts and pallet jacks. This size is commonly used in grocery stores, warehouses, and distribution centers.
In Europe, the 120cm x 80cm pallet, also known as the EUR pallet, is the standard size. It is widely used in industries such as automotive, pharmaceuticals, and food and beverage. The dimensions of this pallet are optimized for compatibility with European trucks and containers, ensuring efficient transportation and storage.
Standard pallet sizes provide a level of uniformity and predictability in the movement of goods. They enable efficient stacking, storage, and transportation, reducing costs and minimizing damage to products during handling.
-
Custom Pallet Sizes
While standard sizes are popular, custom pallets are also widely used to accommodate specific needs. Custom pallets can be designed to fit irregularly shaped products or to optimize space utilization based on unique requirements.
Custom pallets offer flexibility and versatility in handling specialized products. For example, in the automotive industry, custom pallets are often used to transport car parts of different shapes and sizes. These pallets are designed with specific compartments and fixtures to securely hold the parts during transportation.
In the retail sector, custom pallets are used to create attractive displays and maximize product visibility. These pallets may have built-in shelves or compartments to showcase products in an organized and appealing manner.
Custom pallet sizes can also be tailored to fit specific storage spaces or transportation equipment. For instance, in warehouses with limited vertical clearance, custom pallets with reduced heights can be designed to maximize storage capacity. Similarly, in industries where space utilization is critical, custom pallets can be engineered to fit precisely within shipping containers or trucks, optimizing load efficiency.
Custom pallet sizes provide a solution for businesses with unique requirements. They allow for efficient handling, storage, and transportation of products that may not conform to standard dimensions. By tailoring pallet sizes to specific needs, businesses can enhance operational efficiency and reduce costs.
The Importance of Box Dimensions
Now that we understand pallet dimensions, let’s explore the significance of box dimensions in optimizing pallet usage.
When it comes to shipping and logistics, box dimensions play a vital role in ensuring efficient and cost-effective transportation. The size of the box not only affects the number of items that can be packed but also impacts the overall stability and safety of the shipment.
-
Common Box Sizes
Boxes come in a wide variety of sizes, from small ones used for individual items to larger ones for bulk shipments. Standard box sizes often range from 12″ x 12″ x 12″ (30cm x 30cm x 30cm) to 24″ x 24″ x 24″ (60cm x 60cm x 60cm).
Smaller boxes are commonly used for delicate or valuable items that require extra protection during transit. On the other hand, larger boxes are ideal for bulky items or when shipping multiple products together.
It’s important to choose the right box size based on the nature of the goods being shipped. Using a box that is too large for the items can result in unnecessary empty space, leading to increased shipping costs and potential damage due to movement during transportation. Conversely, using a box that is too small may not provide adequate protection and could lead to product damage.
-
Calculating Box Volume
Calculating the volume of a box is crucial in determining the number of boxes that can fit on a pallet. Box volume is calculated by multiplying the length, width, and height of the box together. For example, a box measuring 12″ x 12″ x 12″ has a volume of 1,728 cubic inches (or 1 cubic foot).
Knowing the box volume is essential for optimizing pallet usage. By understanding the volume of each box, logistics professionals can accurately calculate the number of boxes that can be stacked on a pallet, maximizing the use of available space.
Moreover, calculating box volume allows for efficient planning of transportation resources. By knowing the exact dimensions of the boxes, logistics managers can determine the most suitable mode of transportation, whether it be by truck, ship, or air, and make informed decisions regarding the allocation of resources.
Considering the importance of box dimensions, it is crucial for businesses to carefully analyze their shipping requirements and select the appropriate box sizes for their products. By doing so, they can optimize pallet usage, reduce shipping costs, and ensure the safe delivery of goods to their customers.
The Role of Stacking in Pallet Optimization
Efficient stacking techniques can significantly impact the number of boxes that can fit on a pallet. This not only helps in maximizing space utilization but also ensures stability during transportation. Let’s delve into different stacking methods:
-
Vertical Stacking Techniques
Stacking boxes vertically ensures maximum use of the pallet’s height. By aligning boxes one on top of the other, you can create stable and efficient stacks that leave minimal wasted space. This technique is particularly useful when dealing with items that are uniform in shape and size.
When implementing vertical stacking, it is important to consider the weight distribution of the boxes. Placing heavier items at the bottom of the stack helps maintain balance and stability. Additionally, using dividers or separators between layers can provide added support and prevent boxes from shifting during transportation.
Furthermore, vertical stacking allows for easy access to individual boxes, making it convenient for both loading and unloading processes. This method is commonly used in industries such as warehousing, logistics, and retail, where efficient space utilization is crucial for cost-effective operations.
-
Interlocking Stacking Techniques
Interlocking stacking involves strategically fitting the boxes together, like a puzzle. By placing boxes in a way that minimizes gaps between them, you can optimize space utilization and prevent boxes from shifting during transportation. This technique is particularly effective when dealing with irregularly shaped items or items with varying sizes.
When implementing interlocking stacking, it is important to consider the dimensions and shapes of the boxes. By analyzing the contours and edges of each box, you can identify the best possible arrangement to minimize wasted space. This method requires careful planning and attention to detail to ensure a secure and stable stack.
In addition to maximizing space utilization, interlocking stacking techniques also offer benefits such as enhanced load stability and reduced risk of damage to the contents. By tightly fitting the boxes together, you minimize the chances of them shifting or toppling over during transportation, thus reducing the likelihood of product breakage or loss.
It is worth noting that interlocking stacking may require additional packaging materials, such as corner protectors or cushioning, to provide extra support and protection to the boxes. These measures help safeguard the integrity of the stacked items and maintain their quality throughout the supply chain.
By understanding and implementing different stacking techniques, businesses can optimize their pallet utilization and improve overall operational efficiency. Whether it’s vertical stacking for uniform items or interlocking stacking for irregularly shaped items, the goal remains the same – to maximize space utilization, ensure stability, and protect the contents during transportation.
The Impact of Load Stability on Pallet Capacity
Choosing the right stacking technique is crucial, not only for space optimization but also for load stability during transit. Let’s explore some techniques to enhance load stability:
-
Balancing Weight for Stability
To ensure load stability, it’s important to distribute the weight evenly across the pallet. Placing heavier boxes at the bottom and lighter ones on top helps maintain a stable and secure load.
-
Utilizing Shrink Wrap and Strapping
Securing the boxes with shrink wrap and strapping provides an extra layer of protection and stability. These materials help prevent boxes from shifting or falling during transportation, ensuring the safety and integrity of the load.
The Pallet Box Calculator: A Step-by-Step Guide
Now that we have covered the key factors in maximizing pallet capacity, let’s introduce a handy tool – the pallet box calculator. This calculator simplifies the process of determining how many boxes can fit on a pallet. Here’s a step-by-step guide on how to use it:
-
Inputting Pallet and Box Dimensions
Start by entering the dimensions of your pallet and boxes into the calculator. Ensure you accurately measure the length, width, and height of each element. The calculator will use this information to perform the calculations.
-
Selecting Your Stacking Method
After providing the dimensions, you’ll have the option to select your desired stacking method, be it vertical stacking or interlocking stacking. The calculator will consider your selection while calculating the optimal number of boxes.
-
Interpreting Your Results
Once you’ve entered the relevant details and selected the stacking method, the pallet box calculator will display the maximum number of boxes that can fit on your pallet. This valuable information can help streamline your logistical operations and improve efficiency.
Conclusion
Knowing how many boxes can fit on a pallet is crucial in optimizing space utilization and reducing transportation costs. By understanding pallet dimensions, box dimensions, stacking techniques, and load stability, you can make informed decisions to maximize pallet capacity. The pallet box calculator serves as a valuable tool in simplifying these calculations, providing you with accurate results for efficient shipping and logistics operations.
Maximize Your Pallet’s Potential with Your eCom Agent
Ready to take your Amazon selling game to the next level? Your eCom Agent’s suite of AI tools is designed to streamline your operations and boost your efficiency. From product development to review analysis and detail page enhancement, our AI does the heavy lifting for you. Don’t let logistics slow you down. Subscribe to Your eCom Agent’s AI Tools today and transform hours of work into seconds of smart, AI-powered strategy.