In today’s fast-paced e-commerce industry, efficient inventory control plays a crucial role in the success of a company like Amazon. With millions of products being bought and sold each day, it is essential for Amazon to have a strong inventory control system in place to ensure smooth operations and customer satisfaction.
Understanding Inventory Control at Amazon
Inventory control refers to the management of stock levels, ensuring that the right products are available at the right time, in the right quantities. In the case of Amazon, effective inventory control enables the company to fulfill orders promptly, minimize stock-outs, and optimize warehouse operations.
Before we begin: Every Amazon Seller needs a suite of tools for Keyword Research, Product Development, and Listing Optimization. Our top pick is Helium 10 and readers of this post can get 20% off their first 6 months by clicking the image below.
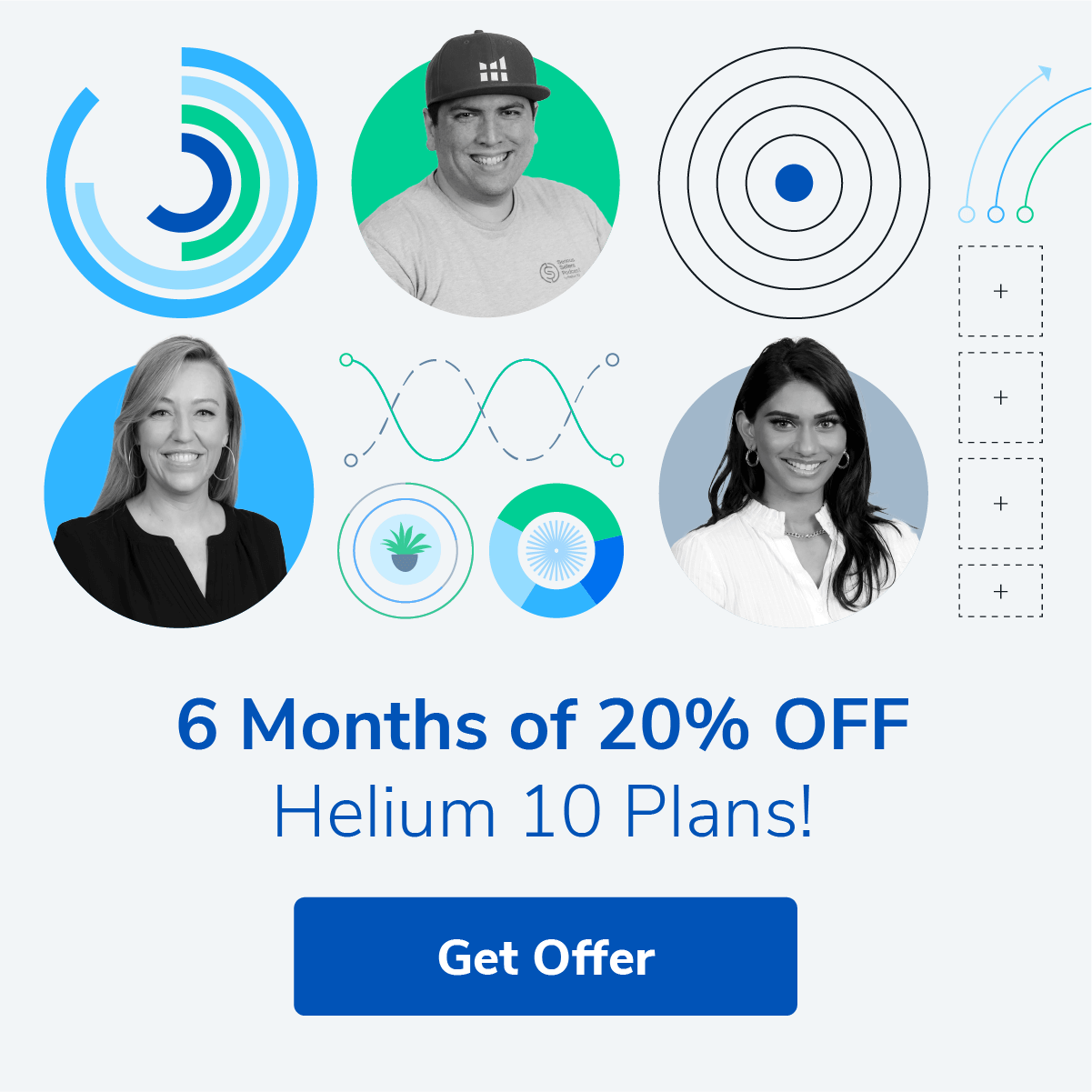
Amazon’s inventory control system is a crucial component of its overall success. By carefully managing its inventory, Amazon can offer customers a wide range of products, maintain low prices, and provide fast shipping times. This level of control ultimately translates into higher customer satisfaction and repeat business.
One key element of Amazon’s inventory control system is its centralized database. This database provides real-time visibility into stock levels across Amazon’s vast network of warehouses. With this information readily available, Amazon can accurately track inventory, identify trends, and make informed decisions regarding stock replenishment and allocation.
Another important aspect of Amazon’s inventory control system is the use of advanced algorithms and predictive analytics. These tools allow Amazon to forecast demand with a high degree of accuracy. By analyzing historical sales data, market trends, and other relevant factors, Amazon can anticipate customer demand and adjust its inventory levels accordingly. This proactive approach helps to minimize stock-outs and ensure that popular products are always available to customers.
In addition to demand forecasting, Amazon’s inventory control system also focuses on resource allocation. By analyzing data on warehouse capacity, labor availability, and transportation logistics, Amazon can optimize its operations and ensure that products are stored and shipped efficiently. This not only reduces costs but also improves order fulfillment speed, allowing Amazon to meet its customers’ expectations for fast and reliable delivery.
Furthermore, Amazon’s inventory control system is designed to handle the complexities of its vast product catalog. With millions of products available for sale, Amazon must effectively categorize and organize its inventory. Through the use of advanced categorization algorithms and robust search capabilities, Amazon ensures that customers can easily find the products they are looking for, further enhancing the overall shopping experience.
In conclusion, Amazon’s inventory control system is a critical factor in its success. By leveraging advanced technology, data analytics, and efficient processes, Amazon can effectively manage its inventory, meet customer demand, and deliver an exceptional shopping experience. Through continuous innovation and optimization, Amazon continues to set the standard for inventory control in the e-commerce industry.
The Importance of Quality Assurance in Inventory Control
Quality assurance is a critical aspect of inventory control at Amazon. It involves the implementation of processes and procedures to ensure that products are received, stored, and shipped in optimal condition, meeting quality standards and customer expectations.
At Amazon, quality assurance is not just a mere formality; it is a comprehensive approach that permeates every step of the inventory control process. From the moment a product arrives at one of Amazon’s fulfillment centers to the moment it reaches the customer’s doorstep, every effort is made to guarantee its quality and integrity.
Defining Quality Assurance in the Context of Inventory Control
Quality assurance in inventory control encompasses various activities, including thorough inspections of incoming stock, accurate identification and categorization of products, proper storage and handling, and regular audits to identify any potential issues or discrepancies.
When a shipment of products arrives at an Amazon fulfillment center, it undergoes a rigorous inspection process. Trained quality assurance specialists carefully examine each item to ensure that it meets the specified quality standards. This includes checking for any visible defects, verifying the accuracy of the product’s labeling and packaging, and confirming that it matches the description provided by the supplier.
Once the products pass the initial inspection, they are accurately identified and categorized. This step is crucial for efficient inventory management. Each item is assigned a unique identifier, such as a barcode or SKU (Stock Keeping Unit), which allows for easy tracking and retrieval. This meticulous categorization ensures that products can be located quickly when an order is placed, minimizing delays and improving customer satisfaction.
Proper storage and handling are also essential components of quality assurance in inventory control. Amazon’s fulfillment centers are equipped with state-of-the-art facilities designed to maintain the integrity of the products. Temperature-controlled areas are available for items that require specific storage conditions, such as perishable goods or sensitive electronics. Additionally, specialized equipment, such as forklifts and conveyor systems, are used to handle products with care, reducing the risk of damage during transportation and storage.
Regular audits are conducted to maintain the accuracy and integrity of the inventory. These audits involve physical counts of the products to ensure that the recorded quantities match the actual stock levels. Any discrepancies are promptly investigated and resolved to prevent inventory inaccuracies and potential stockouts.
The Impact of Quality Assurance on Inventory Management
A robust quality assurance system ensures that Amazon’s inventory is accurate, well-maintained, and free from defects. This reduces the risk of selling damaged or expired products, enhances customer trust, and minimizes returns and associated costs. Furthermore, it helps Amazon to maintain a positive brand image in the market.
By implementing stringent quality assurance measures, Amazon can confidently assure its customers that the products they receive are of the highest quality. This commitment to quality has earned Amazon a reputation for reliability and customer satisfaction. It also contributes to the company’s long-term success by fostering customer loyalty and encouraging repeat purchases.
Moreover, quality assurance in inventory control enables Amazon to optimize its operations. Accurate inventory counts and well-maintained stock levels allow for efficient order fulfillment, reducing the risk of stockouts or overstocking. This, in turn, minimizes storage costs and improves overall operational efficiency.
In conclusion, quality assurance plays a vital role in inventory control at Amazon. It ensures that products are received, stored, and shipped in optimal condition, meeting quality standards and customer expectations. Through thorough inspections, accurate identification and categorization, proper storage and handling, and regular audits, Amazon maintains an accurate and well-maintained inventory. This commitment to quality enhances customer trust, reduces returns and associated costs, and contributes to Amazon’s positive brand image and long-term success.
Challenges in Amazon’s Current Inventory Control Quality Assurance
While Amazon has achieved remarkable success in inventory control, there are still areas that can be improved in terms of quality assurance.
Amazon’s inventory control is undoubtedly impressive, but like any system, it is not without its challenges. These challenges, if left unaddressed, can have significant implications for the company’s operations and reputation. It is crucial for Amazon to identify and tackle these issues head-on to maintain its position as a leader in the e-commerce industry.
Identifying the Gaps in Amazon’s Inventory Control
One weakness lies in the need for better visibility and accuracy when receiving and storing products. While Amazon has implemented advanced technologies and processes to streamline these operations, there is still room for improvement. Increasing the efficiency of these processes would minimize the chances of inventory discrepancies and maximize overall control.
Furthermore, Amazon’s vast and ever-expanding product catalog poses a unique challenge in maintaining accurate inventory control. With millions of products being added and sold on the platform daily, ensuring that each item is properly accounted for can be a daunting task. The company must continuously innovate and develop robust systems to handle this immense volume of inventory.
Another area that requires attention is the management of third-party sellers. Amazon’s marketplace allows independent sellers to list and sell their products, which adds complexity to the inventory control process. Ensuring that these sellers adhere to Amazon’s quality standards and accurately report their inventory is crucial for maintaining a seamless customer experience.
The Consequences of Inadequate Quality Assurance
Inadequate quality assurance can result in serious consequences, such as delivering defective products to customers, tarnishing the company’s reputation, and incurring financial losses due to returns and damaged stock. The repercussions of these issues can be far-reaching, impacting customer trust and loyalty.
When customers receive defective or subpar products, it not only affects their satisfaction but also damages Amazon’s reputation as a reliable and trustworthy platform. Negative reviews and word-of-mouth can spread quickly, leading to a decline in sales and potential loss of customers to competitors.
Moreover, the financial implications of inadequate quality assurance should not be underestimated. Returns and refunds due to defective products can result in significant financial losses for Amazon. Additionally, damaged stock that cannot be sold further adds to the financial burden. It is therefore imperative for Amazon to address these shortcomings and invest in robust quality assurance measures.
In conclusion, while Amazon has achieved remarkable success in inventory control, there are still areas that can be improved in terms of quality assurance. By identifying the gaps in inventory control, such as the need for better visibility and accuracy, and understanding the consequences of inadequate quality assurance, Amazon can take proactive steps to enhance its systems and processes. This continuous improvement will not only benefit the company but also ensure customer satisfaction and maintain its position as a leader in the e-commerce industry.
Strategies for Improving Inventory Control Quality Assurance
Amazon can enhance its inventory control quality assurance through several strategies.
Adopting Advanced Technologies for Better Inventory Control
Implementing cutting-edge technologies, such as automated barcode scanning and RFID tagging, can significantly improve the speed and accuracy of inventory processes. These technologies enable real-time tracking, reduce human errors, and facilitate seamless collaboration among warehouse teams.
Enhancing Employee Training for Quality Assurance
Investing in comprehensive training programs for employees involved in inventory control can greatly enhance their understanding of quality assurance principles and practices. This would empower them to identify potential issues, exercise greater attention to detail, and improve overall quality control processes.
Measuring the Success of Improved Inventory Control Quality Assurance
To gauge the effectiveness of their efforts in improving inventory control quality assurance, it is essential for Amazon to establish key performance indicators (KPIs).
Key Performance Indicators for Inventory Control
Some relevant KPIs include inventory accuracy, order fulfillment rate, return rate, and customer satisfaction ratings. Regularly monitoring these metrics would allow Amazon to assess the impact of quality assurance improvements and make data-driven decisions for further optimization.
Evaluating the Effectiveness of Quality Assurance Improvements
Through periodic audits and feedback analysis, Amazon can evaluate the success of quality assurance improvements. This ongoing evaluation process ensures that any deviations or shortcomings are promptly identified, allowing for timely corrective measures.
Conclusion
Efficient inventory control and quality assurance are critical factors behind Amazon’s unparalleled success. By understanding the importance of maintaining optimal stock levels and continuously improving quality assurance processes, Amazon can further solidify its position as a global leader in the e-commerce industry.
Take Your Amazon Business to the Next Level
Ready to enhance your inventory control and quality assurance with cutting-edge AI? Subscribe to Your eCom Agent’s AI Tools today and transform the way you manage your Amazon inventory. Let our AI suite streamline your processes, from product development to review analysis, and see the difference that intelligent automation can make. Join the revolution and ensure your Amazon business thrives in the competitive e-commerce landscape.