In today’s rapidly evolving digital landscape, efficient delivery fulfillment is becoming increasingly crucial for businesses of all sizes. Whether you are an e-commerce giant or a local brick-and-mortar store looking to expand your online presence, understanding the ins and outs of delivery fulfillment is essential to providing a seamless customer experience. This comprehensive guide will walk you through the key components, steps, and technology involved in the delivery fulfillment process. So, let’s dive in and explore everything you need to know.
Understanding Delivery Fulfillment
Before we delve into the intricacies of delivery fulfillment, let’s start by defining this crucial aspect of the supply chain.
Before we begin: Every Amazon Seller needs a suite of tools for Keyword Research, Product Development, and Listing Optimization. Our top pick is Helium 10 and readers of this post can get 20% off their first 6 months by clicking the image below.
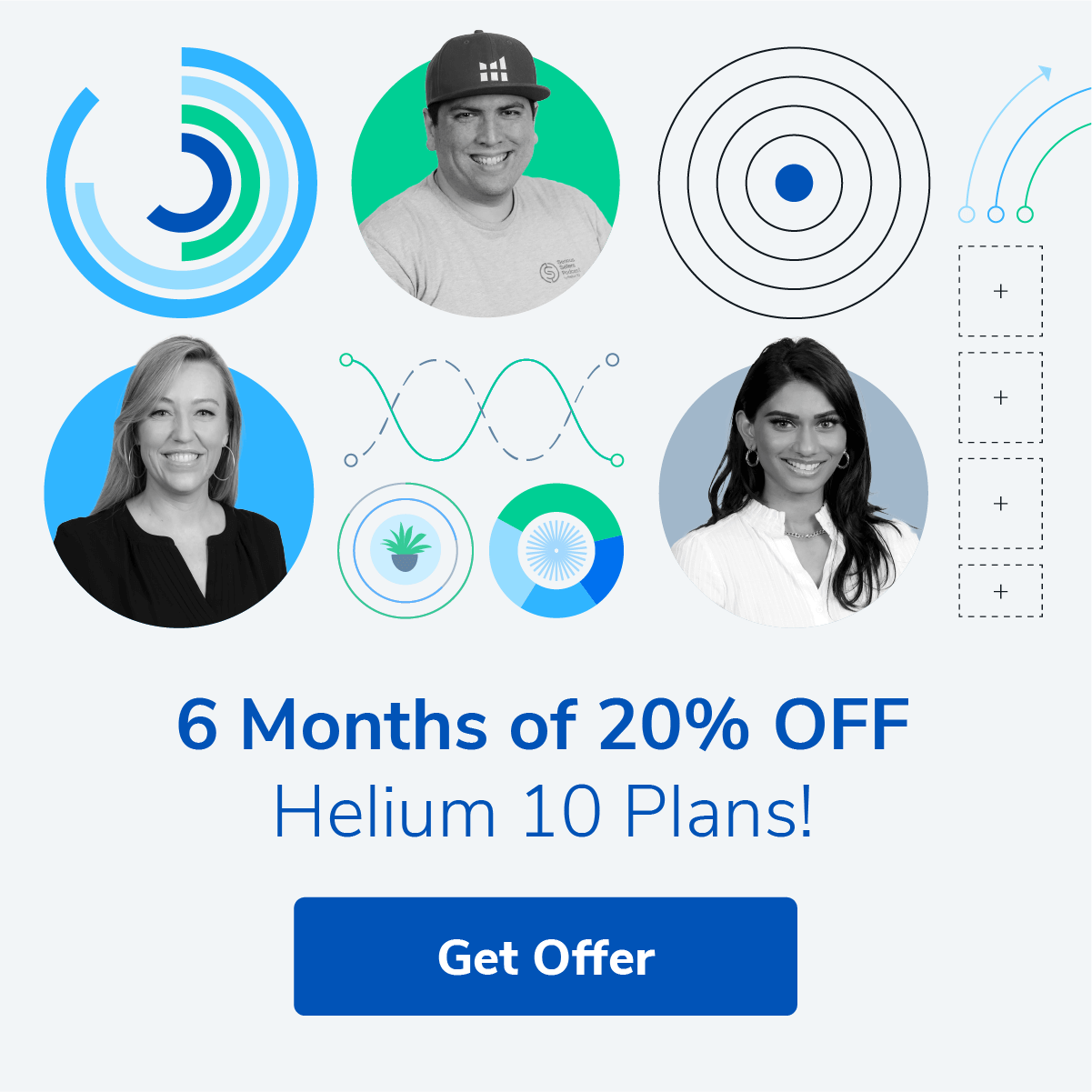
Delivery fulfillment encompasses all the activities involved in processing and delivering orders to customers. From receiving inventory to packaging and shipping, each step plays a vital role in ensuring timely and accurate delivery.
When it comes to delivery fulfillment, efficiency is key. Efficient delivery fulfillment is paramount for customer satisfaction and retention. With the rise of online shopping, customers expect fast and reliable delivery. A study revealed that 66% of consumers say that delivery speed influences their decision to shop with an online retailer. Delayed or incorrect deliveries can lead to negative reviews and damage your brand reputation.
Now, let’s take a closer look at the different stages of delivery fulfillment:
1. Receiving Inventory
The first step in delivery fulfillment is receiving inventory. This involves inspecting and verifying the received goods against the purchase orders. It is essential to check for any damages or discrepancies and record them accurately. Proper inventory management ensures that you have the right products in stock to fulfill customer orders.
2. Order Processing
Once the inventory is received, the next step is order processing. This includes picking and packing the items for shipment. Efficient order processing involves organizing the warehouse layout to optimize picking routes and using barcode scanning or other technology to ensure accurate item selection.
3. Packaging
Proper packaging is crucial to protect the products during transit. The packaging should be sturdy enough to withstand handling and transportation. It is also important to consider the size and weight of the package to minimize shipping costs and optimize space utilization.
4. Shipping
Shipping is the final stage of delivery fulfillment. Choosing the right shipping method and carrier is essential to ensure timely delivery. Factors such as cost, speed, and reliability should be taken into consideration. Tracking numbers should be provided to customers so they can monitor the progress of their shipments.
Efficient delivery fulfillment requires effective coordination and communication between different departments, including inventory management, order processing, packaging, and shipping. Automation and technology play a significant role in streamlining these processes, reducing errors, and improving overall efficiency.
In conclusion, delivery fulfillment is a critical aspect of the supply chain that involves various stages, from receiving inventory to packaging and shipping. Efficient delivery fulfillment is essential for customer satisfaction and retention in today’s competitive online marketplace. By understanding and optimizing each stage of the process, businesses can ensure timely and accurate delivery, thereby enhancing their brand reputation and customer loyalty.
Key Components of Delivery Fulfillment
Now that we grasp the importance of delivery fulfillment, let’s explore its key components.
Delivery fulfillment is a critical aspect of any business that sells products. It involves a series of processes that ensure orders are accurately processed, packaged, and delivered to customers in a timely manner. Let’s dive deeper into the key components of delivery fulfillment.
Inventory Management
Effective inventory management is the foundation of successful fulfillment. It involves accurately tracking your stock levels, ensuring sufficient inventory to meet customer demand, and minimizing the risk of overstocking or stockouts.
Inventory management is a complex task that requires careful planning and execution. It starts with setting up a robust system to track and manage inventory. This includes implementing barcode scanning technology, using inventory management software, and conducting regular stock audits.
Furthermore, inventory management involves forecasting demand and planning for seasonal fluctuations. By analyzing historical sales data and market trends, businesses can predict future demand and adjust their inventory levels accordingly. This helps prevent stockouts and ensures that customers can always find the products they need.
Order Processing
Order processing involves receiving, verifying, and preparing customer orders for shipment. This includes picking the items from the warehouse, checking for accuracy, and preparing them for packaging.
Efficient order processing is crucial for customer satisfaction. It starts with receiving orders promptly and accurately. This can be done through various channels, such as online platforms, phone calls, or email. Once the orders are received, they need to be verified for accuracy, ensuring that the correct items and quantities are being shipped.
After verification, the items are picked from the warehouse. This process requires careful organization and efficient picking methods to minimize errors and maximize productivity. Once the items are picked, they are checked again for accuracy before being prepared for packaging.
Order processing also involves generating shipping labels, invoices, and any necessary documentation. This ensures that the packages are properly labeled and all required information is included.
Shipping and Delivery
The final stage of delivery fulfillment is shipping and delivery. This encompasses the physical transportation of packages from your warehouse to the customers’ location. Choosing the right shipping carrier and optimizing delivery routes can significantly impact efficiency and customer satisfaction.
Shipping and delivery require careful planning and coordination. Businesses need to select reliable shipping carriers that offer competitive rates and timely delivery. This involves negotiating contracts, comparing shipping options, and monitoring carrier performance.
Optimizing delivery routes is another important aspect of shipping and delivery. By analyzing customer locations and order volumes, businesses can determine the most efficient routes for their delivery vehicles. This helps reduce transportation costs, minimize delivery times, and improve overall customer satisfaction.
Furthermore, businesses need to ensure that packages are properly packaged and protected during transportation. This includes using appropriate packaging materials, such as bubble wrap or packing peanuts, to prevent damage during transit.
In conclusion, delivery fulfillment is a complex process that involves inventory management, order processing, and shipping and delivery. By effectively managing these key components, businesses can ensure that their products reach customers in a timely and efficient manner, leading to increased customer satisfaction and loyalty.
Steps in the Delivery Fulfillment Process
Now that we understand the key components, let’s break down the delivery fulfillment process into individual steps.
Receiving and Storing Inventory
Upon receiving inventory from suppliers, it’s essential to inspect and organize it for easy retrieval. Efficient storage practices, such as using barcodes or RFID tags, can streamline the fulfillment process and minimize errors.
Inspecting the received inventory involves carefully examining each item to ensure that it matches the order specifications and is free from any damages or defects. This step is crucial to maintain high-quality standards and prevent any issues during the fulfillment process.
Organizing the inventory plays a vital role in efficient order fulfillment. By categorizing the received items based on their characteristics, such as size, type, or popularity, it becomes easier to locate and retrieve them when needed. This systematic approach saves time and reduces the chances of errors or delays.
Order Processing and Packaging
Once a customer places an order, it goes through the order processing stage. This step involves confirming the order, gathering the items, and carefully packaging them to ensure safe transport.
Order confirmation is an important part of the process as it verifies the customer’s intent to purchase and ensures that the items are available in the inventory. This step may include checking the stock levels, validating payment details, and confirming the shipping address.
Gathering the items for the order requires efficient coordination between the warehouse staff. They carefully pick the items from their designated locations, ensuring accuracy and minimizing the chances of picking the wrong product. This attention to detail guarantees that customers receive the correct items they ordered.
Once all the items are gathered, the packaging process begins. Packaging materials, such as boxes, bubble wrap, or padded envelopes, are selected based on the nature of the items. Special care is taken to protect fragile or delicate products, ensuring they reach the customer in perfect condition.
Shipping and Delivery
After packaging, the orders are handed over to the shipping carrier for delivery. Tracking numbers and order updates allow customers to monitor their shipments, creating a transparent and satisfactory experience.
Shipping carriers play a crucial role in the delivery fulfillment process. They are responsible for transporting the packages from the warehouse to the customer’s doorstep. The choice of shipping carrier depends on various factors, such as the destination, delivery speed, and the nature of the items being shipped.
Tracking numbers provide customers with real-time updates on the status and location of their shipments. This transparency helps build trust and allows customers to plan for the arrival of their orders. In case of any delays or issues during transit, the tracking information enables proactive communication and resolution.
Delivery is the final step in the fulfillment process. The shipping carrier ensures that the package reaches the customer within the estimated timeframe. Timely and reliable delivery is crucial for customer satisfaction and can significantly impact the overall shopping experience.
Choosing a Delivery Fulfillment Service
With the complexity of delivery fulfillment, many businesses opt to outsource this crucial function. Selecting the right delivery fulfillment service plays a significant role in ensuring smooth operations and customer satisfaction.
Factors to Consider
When choosing a delivery fulfillment service, consider factors such as pricing, reliability, scalability, and technological capabilities. Adequate communication channels and integration with your existing systems are also essential for seamless order processing.
Benefits of Outsourcing Delivery Fulfillment
Outsourcing delivery fulfillment can provide numerous benefits to businesses. It frees up internal resources, reduces operational costs, leverages expertise, and allows you to focus on core competencies. Additionally, outsourced fulfillment centers often have extensive networks and can reach customers in various regions more efficiently.
Technology in Delivery Fulfillment
Advancements in technology have revolutionized the delivery fulfillment landscape. Let’s explore the role of automation and the impact of AI and machine learning.
Role of Automation in Delivery Fulfillment
Automation plays a vital role in streamlining the delivery fulfillment process. From automated inventory management systems to robotic order picking, leveraging technology reduces manual errors, increases efficiency, and accelerates order fulfillment.
Impact of AI and Machine Learning
The integration of AI and machine learning algorithms enables predictive analytics, demand forecasting, and intelligent route optimization. By analyzing vast amounts of data, these technologies can enhance decision-making, identify delivery patterns, and minimize delivery times.
In conclusion, the world of delivery fulfillment is dynamic and ever-evolving. Understanding the key components, steps, and technology involved is crucial to providing exceptional customer experiences. By effectively managing inventory, optimizing order processing and packaging, and leveraging the benefits of outsourcing and technology, businesses can stay ahead of the competition and provide seamless delivery fulfillment services. So, take these insights and apply them to your own operations, and unlock the potential for growth and customer satisfaction in the world of delivery fulfillment.
Enhance Your Amazon Selling Experience with AI
Ready to revolutionize your Amazon business? Subscribe to Your eCom Agent’s AI Tools today and harness the power of artificial intelligence to optimize your product development, analyze customer feedback, and improve your detail pages with unparalleled efficiency. Transform your delivery fulfillment strategy and elevate your customer satisfaction to new heights—effortlessly and instantly.