In today’s fast-paced world of e-commerce, fulfillment centers play a crucial role in ensuring that products reach customers efficiently and seamlessly. Understanding the concept and inner workings of a fulfillment center is essential for businesses looking to optimize their operations and improve customer satisfaction. Let’s delve into the key components that make up a fulfillment center and explore how technology has revolutionized the industry.
Understanding the Concept of a Fulfillment Center
A fulfillment center is a warehouse facility that specializes in the storage, packing, and shipping of products for businesses partnering with e-commerce platforms. The primary purpose of a fulfillment center is to streamline the order fulfillment process and ensure that products are delivered to customers in a timely manner.
Before we begin: Every Amazon Seller needs a suite of tools for Keyword Research, Product Development, and Listing Optimization. Our top pick is Helium 10 and readers of this post can get 20% off their first 6 months by clicking the image below.
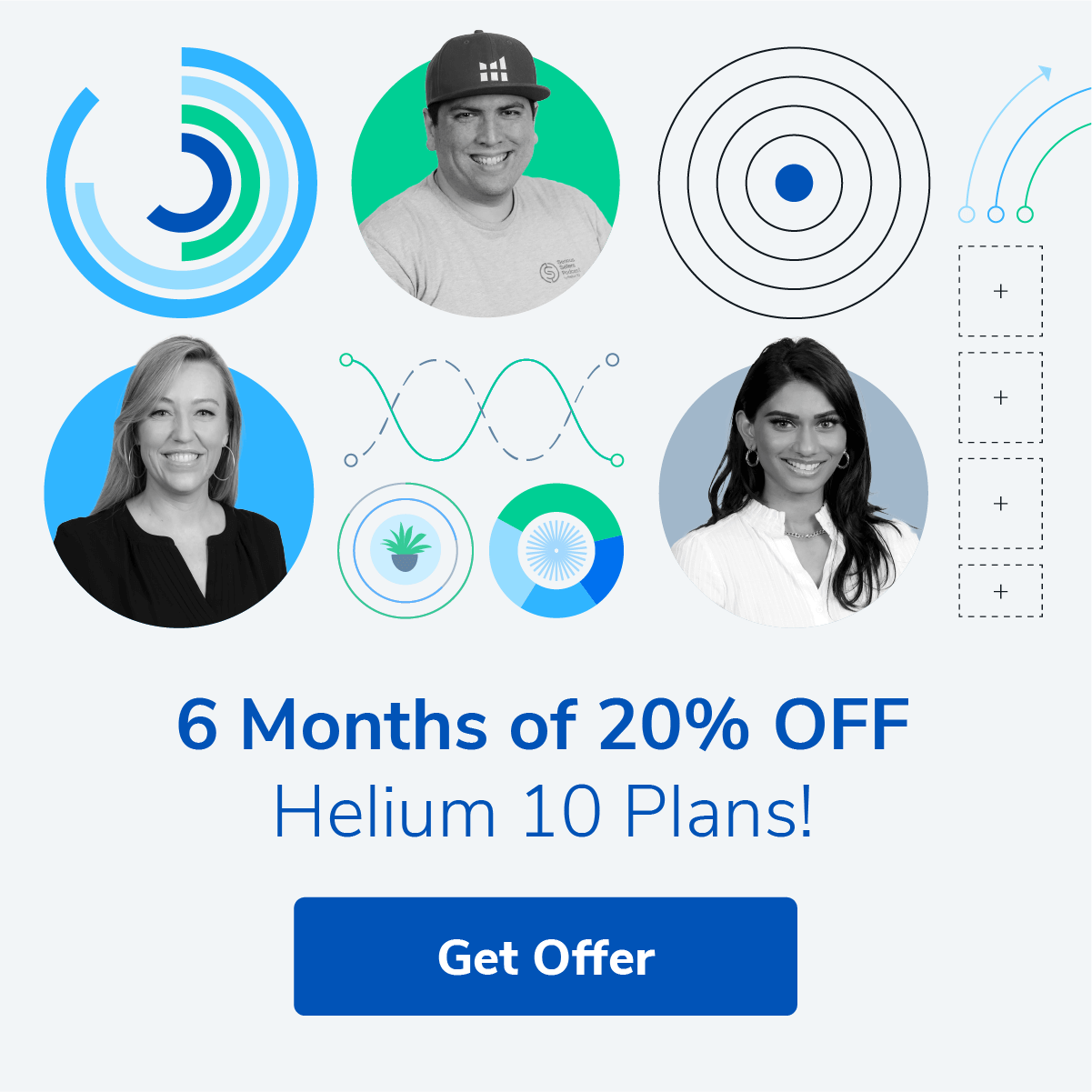
But what exactly goes on inside a fulfillment center? Let’s take a closer look at the key components that make up this crucial part of the e-commerce industry.
Definition and Purpose of a Fulfillment Center
A fulfillment center is a warehouse facility that specializes in the storage, packing, and shipping of products for businesses partnering with e-commerce platforms. The primary purpose of a fulfillment center is to streamline the order fulfillment process and ensure that products are delivered to customers in a timely manner.
Key Components of a Fulfillment Center
A fulfillment center comprises various essential components that work harmoniously to facilitate smooth operations. These components include:
- Receiving and Storage:
Upon receiving products from suppliers, fulfillment centers meticulously inspect and categorize the inventory. This step ensures accurate stock management and avoids discrepancies during order processing.
The receiving and storage area of a fulfillment center is a bustling hub of activity. Skilled workers carefully unload incoming shipments, checking for any signs of damage or discrepancies. Once the products have been inspected, they are meticulously organized and stored in designated areas within the warehouse.
Efficient inventory management systems are employed to keep track of the stock levels, ensuring that there is always enough inventory available to fulfill customer orders. This meticulous attention to detail in the receiving and storage process helps prevent errors and delays in the order fulfillment process.
- Order Processing and Packaging:
Once an order is received, it is carefully picked, packed, and labeled. Adequate packaging plays a significant role in protecting items during transit and maintaining product integrity.
The order processing and packaging area of a fulfillment center is a well-organized space where workers meticulously pick the items required for each order. They ensure that the correct products are selected and that any special instructions from customers, such as gift wrapping or personalized notes, are followed.
After the items have been picked, they are carefully packed using appropriate packaging materials to ensure their safe transportation. This includes using bubble wrap, packing peanuts, or air pillows to protect fragile items. The packages are then labeled with the necessary shipping information, including the customer’s address and any tracking numbers.
Efficient order processing and packaging not only ensures that the correct products reach the customers but also helps maintain the overall quality and condition of the items during transit.
- Shipping and Delivery:
Efficient fulfillment centers partner with reliable logistics providers to ensure prompt and reliable delivery of products to customers’ doorsteps. Real-time tracking and communication enhance transparency and improve the overall customer experience.
Once the packages are ready for shipment, fulfillment centers work closely with trusted logistics providers to ensure that the products are delivered to the customers in a timely manner. These logistics partners handle the transportation and delivery of the packages, utilizing their expertise and infrastructure to ensure efficient and reliable service.
Real-time tracking systems are employed to monitor the progress of each shipment, allowing both the fulfillment center and the customer to have visibility into the package’s journey. This transparency helps build trust and confidence in the delivery process, as customers can easily track their orders and receive updates on estimated delivery times.
Efficient shipping and delivery processes are crucial in providing a positive customer experience. By partnering with reliable logistics providers, fulfillment centers can ensure that products reach customers’ doorsteps in a timely and secure manner.
The Role of Technology in Fulfillment Centers
Fulfillment centers play a crucial role in the supply chain, ensuring that products are efficiently stored, processed, and shipped to customers. In recent years, the integration of technology has transformed these centers, enabling them to operate with greater speed, accuracy, and efficiency. Let’s explore some of the key technologies that have revolutionized the fulfillment center industry.
Inventory Management Systems
To effectively manage inventory, fulfillment centers utilize advanced inventory management systems. These systems are designed to handle the complex task of tracking and organizing vast amounts of products. With real-time tracking capabilities, businesses can monitor their inventory levels at all times, ensuring that they have the right products in stock to meet customer demand.
Automated forecasting is another crucial feature of inventory management systems. By analyzing historical sales data and market trends, these systems can predict future demand with a high degree of accuracy. This allows businesses to optimize their inventory levels, avoiding stockouts and minimizing excess inventory.
Efficient stock replenishment is yet another benefit of inventory management systems. These systems can automatically generate purchase orders when inventory levels reach a certain threshold, streamlining the replenishment process. This ensures that businesses can quickly restock their products, reducing the risk of running out of popular items.
Automation and Robotics in Fulfillment
The integration of automation and robotics has revolutionized the fulfillment center industry, making it possible to handle large volumes of orders with speed and precision. Automated systems have significantly expedited processes such as picking, sorting, and packing.
One of the key advantages of automation is the reduction of human error. By automating repetitive tasks, businesses can minimize the risk of mistakes that can occur during manual handling. This not only improves the accuracy of order fulfillment but also reduces the likelihood of returns or customer dissatisfaction.
Robotics technology, including autonomous guided vehicles (AGVs) and robotic arms, has also played a significant role in enhancing operational efficiency in fulfillment centers. AGVs are used to transport goods within the facility, eliminating the need for manual labor and reducing the time required to move products from one location to another.
Robotic arms, on the other hand, are capable of performing intricate tasks such as picking and packing. These arms can handle items of various shapes and sizes, ensuring that products are carefully and efficiently prepared for shipping. By automating these labor-intensive tasks, businesses can increase their productivity and reduce the strain on human workers.
In conclusion, technology has revolutionized the fulfillment center industry, enabling businesses to operate with greater efficiency and accuracy. Inventory management systems and automation technologies have significantly improved inventory control, order fulfillment, and overall operational efficiency. As technology continues to advance, we can expect further innovations that will shape the future of fulfillment centers.
The Process of Order Fulfillment
Receiving and Storing Inventory
Upon arrival, products undergo thorough quality checks and are sorted into designated storage areas within the fulfillment center. Efficient organization and accurate inventory management systems facilitate quick and precise retrieval when orders are placed.
Order Processing and Packaging
When an order is received, fulfillment center employees retrieve the requested items from the storage area and ensure accurate product selection. The items are then carefully packaged to guarantee safe transport, taking into account factors such as fragility and dimensions.
Shipping and Delivery
Once packaged, the items are handed over to the logistics partner for shipping and delivery to the customer’s designated address. Fulfillment centers collaborate with reputable carriers to ensure secure and timely transportation, providing customers with an exceptional delivery experience.
The Importance of Efficient Fulfillment Operations
Customer Satisfaction and Retention
A well-functioning fulfillment center directly impacts customer satisfaction and retention rates. Prompt order processing, accurate packaging, and timely delivery create a positive and memorable experience for customers, enhancing their loyalty to a brand.
Cost Efficiency and Profitability
Efficient fulfillment operations can significantly contribute to cost savings and increased profitability for businesses. By minimizing errors, optimizing inventory management, and utilizing technologies like automation, fulfillment centers can help reduce operational expenses and improve the bottom line.
Challenges in Fulfillment Center Operations
Managing High Volume Orders
As businesses grow and attract a larger customer base, managing high volumes of orders can become a significant challenge for fulfillment centers. Scalability and strategic planning are crucial in meeting demand and ensuring that operations can handle increased order volumes efficiently.
Dealing with Returns and Exchanges
Returns and exchanges are an inevitable part of the e-commerce business. Fulfillment centers must have robust processes in place to handle returns and exchanges smoothly. Efficiently processing these requests helps maintain customer satisfaction and ensures that returned products are promptly restocked or refurbished.
In conclusion, understanding how a fulfillment center works is vital for businesses seeking to enhance their e-commerce operations. By comprehending the key components, embracing technology advancements, and streamlining order fulfillment processes, businesses can achieve increased customer satisfaction, cost efficiency, and overall profitability.
Enhance Your Amazon Selling Experience with AI
As an Amazon Seller, you understand the importance of efficient fulfillment operations for customer satisfaction and profitability. Your eCom Agent is here to take your e-commerce business to the next level. Utilize our AI-powered tools to develop better products, analyze customer feedback, and optimize your detail pages with unprecedented speed and accuracy. Don’t let manual processes slow you down. Subscribe to Your eCom Agent’s AI Tools today and transform hours of work into seconds of smart, automated decision-making.