Amazon Fulfillment Centers play a crucial role in Amazon’s supply chain, ensuring efficient order processing, inventory management, and packaging and shipping processes. This article takes an in-depth look at the operations of Amazon Fulfillment Center BFL1, shedding light on its unique features, inner workings, the human element, and the role of technology and automation in improving efficiency and customer satisfaction.
Understanding Amazon’s Fulfillment Network
To comprehend the operations of Amazon Fulfillment Center BFL1, it is essential to understand how it fits into Amazon’s intricate fulfillment network. Fulfillment centers serve as the backbone of Amazon’s supply chain, essentially acting as large warehouses from which products are stored, processed, and shipped to customers all around the world.
Before we begin: Every Amazon Seller needs a suite of tools for Keyword Research, Product Development, and Listing Optimization. Our top pick is Helium 10 and readers of this post can get 20% off their first 6 months by clicking the image below.
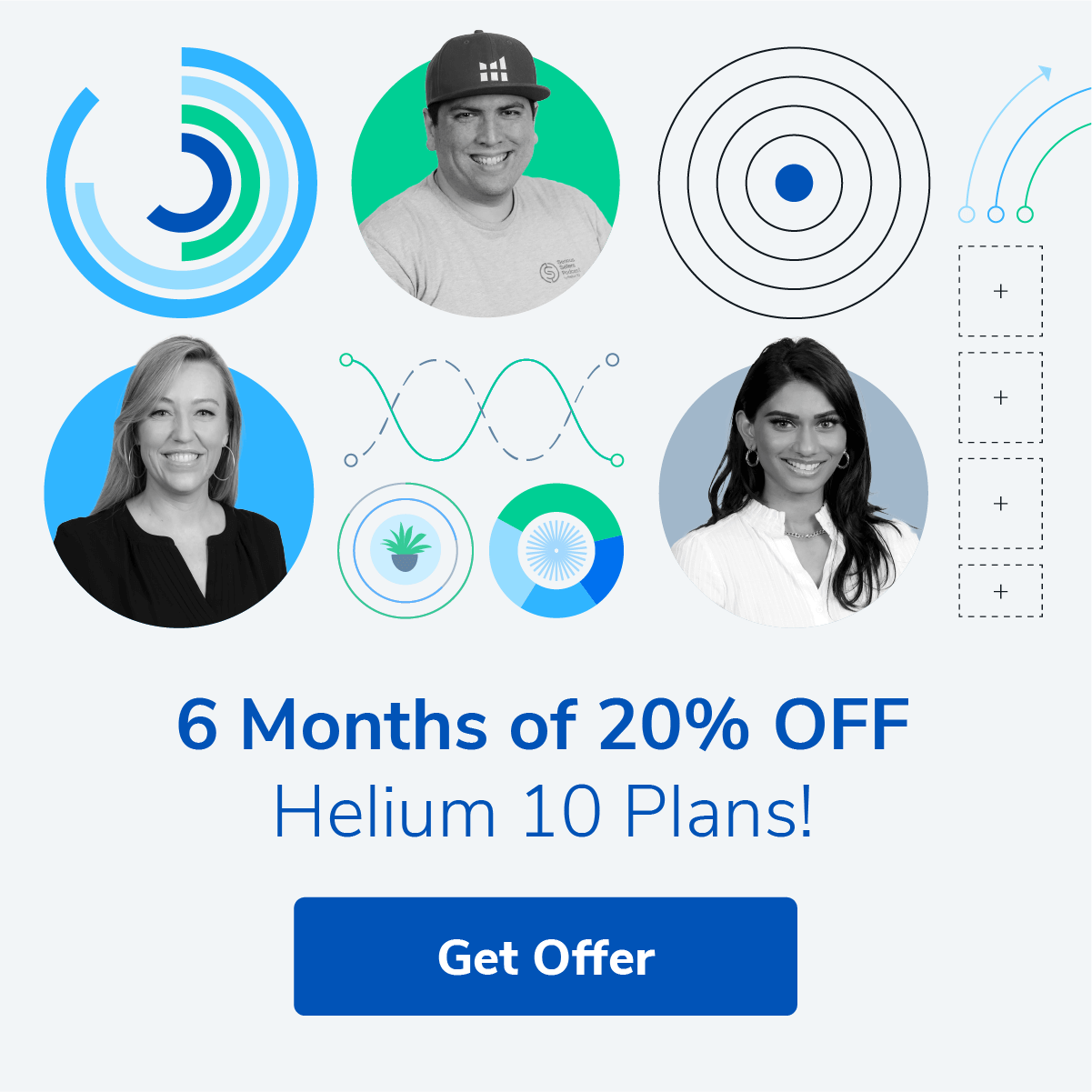
The Role of Fulfillment Centers in Amazon’s Supply Chain
In Amazon’s supply chain, fulfillment centers serve multiple critical functions. They receive inbound shipments from manufacturers, distributors, and suppliers, ensuring the efficient flow and storage of inventory. This process involves meticulous inventory management systems that track the arrival and departure of products, ensuring that the right items are available at the right time.
Once the products are received, fulfillment center employees meticulously organize them within the vast warehouse space. They utilize advanced algorithms and automation technologies to optimize storage capacity and minimize the time it takes to locate and retrieve items when an order is placed.
When a customer places an order on Amazon’s website, the fulfillment center nearest to the customer’s location is responsible for fulfilling that order. This ensures that the shipping time is minimized, allowing for faster delivery and a better customer experience. Fulfillment center employees pick the items from the shelves, carefully pack them in appropriate packaging materials, and prepare them for shipment.
Additionally, fulfillment centers play a crucial role in managing returns. When customers return items, they are sent back to the nearest fulfillment center, where they are inspected, processed, and either restocked or disposed of, depending on their condition.
The Unique Features of Amazon Fulfillment Center BFL1
Amazon Fulfillment Center BFL1, located in the heart of a bustling industrial hub, boasts several unique features that set it apart from other centers. With a sprawling layout spanning multiple floors, BFL1 houses an extensive variety of products, ranging from household essentials to consumer electronics and beyond.
The layout of BFL1 is meticulously designed to maximize efficiency and minimize the time it takes for employees to locate and retrieve items. The products are organized into specific aisles and sections based on their category, ensuring that employees can quickly navigate through the vast warehouse and fulfill customer orders in a timely manner.
BFL1 also utilizes state-of-the-art automation technologies to streamline its operations. Automated conveyor belts transport products from one area of the warehouse to another, reducing the need for manual transportation and increasing overall efficiency. Robotic systems assist in picking and packing items, further enhancing the speed and accuracy of order fulfillment.
Moreover, BFL1’s strategic location enables efficient transportation connections, facilitating the timely delivery of customer orders. It is strategically positioned near major highways and transportation hubs, allowing for seamless integration with Amazon’s extensive logistics network. This ensures that products can be quickly transported to nearby delivery stations, from where they are dispatched for final delivery to customers.
In conclusion, Amazon Fulfillment Center BFL1 plays a vital role in Amazon’s fulfillment network. It serves as a hub for storing, processing, and shipping a wide range of products to customers worldwide. With its unique features and strategic location, BFL1 ensures efficient operations and timely delivery, contributing to Amazon’s commitment to customer satisfaction.
The Inner Workings of Amazon Fulfillment Center BFL1
Now, let’s delve into the inner workings of Amazon Fulfillment Center BFL1, exploring the order processing procedure, inventory management strategies, and packaging and shipping processes that keep its operations running smoothly.
The Order Processing Procedure
At Amazon Fulfillment Center BFL1, the order processing procedure follows a well-orchestrated sequence of steps that minimize handling time while ensuring order accuracy. Once an order is received, it is promptly routed to the storage area where the corresponding items are located. Dedicated employees, guided by advanced inventory tracking systems, retrieve the products and prepare them for packaging.
The order processing procedure at BFL1 is optimized for efficiency and precision. Each step is carefully designed to minimize errors and maximize customer satisfaction. As the order moves through the fulfillment center, it undergoes multiple quality checks to ensure that the correct items are picked and packed. This meticulous attention to detail guarantees that customers receive their orders accurately and on time.
Inventory Management Strategies
Efficient inventory management lies at the core of any successful fulfillment center. At BFL1, a combination of advanced algorithms, real-time tracking systems, and predictive analytics ensures optimal inventory levels. This enables Amazon to meet customer demands while minimizing storage costs and reducing the likelihood of stockouts.
BFL1 employs cutting-edge technology to track inventory levels in real-time. This allows the fulfillment center to anticipate demand patterns and adjust inventory accordingly. By leveraging predictive analytics, Amazon can accurately forecast future demand, enabling proactive inventory replenishment. This strategic approach to inventory management ensures that popular products are always in stock, enhancing customer satisfaction and driving sales.
Additionally, regular inventory audits and quality control measures help maintain inventory accuracy and eliminate discrepancies. BFL1 conducts frequent physical inventory counts to reconcile the data from the tracking systems with the actual stock on hand. This meticulous process ensures that the inventory records are up to date and reliable, preventing any potential issues with order fulfillment.
Packaging and Shipping Processes
The packaging and shipping department at Amazon Fulfillment Center BFL1 is equipped with state-of-the-art machinery and efficient processes to expedite order fulfillment. Packaging materials, tailored to each product’s shape and size, are carefully selected to ensure safe transportation.
BFL1 prioritizes the safety and protection of products during the shipping process. The packaging materials used are specifically chosen to provide adequate cushioning and support, minimizing the risk of damage during transit. Additionally, specialized packaging solutions are employed for fragile or delicate items, ensuring they arrive at the customer’s doorstep in pristine condition.
Automated labeling systems streamline the package labeling process, minimizing errors and enhancing shipping efficiency. These systems automatically generate and apply shipping labels, eliminating the need for manual labeling and reducing the chances of mislabeling or misrouting. This automation not only saves time but also improves accuracy, ensuring that each package is correctly labeled and ready for delivery.
Once the packages are ready, they are swiftly dispatched to various delivery partners for final-mile delivery. BFL1 works closely with a network of trusted carriers to ensure prompt and reliable delivery. By partnering with reputable logistics providers, Amazon can leverage their expertise and infrastructure to efficiently transport packages to customers’ doorsteps, even during peak periods.
In conclusion, Amazon Fulfillment Center BFL1 operates with meticulous precision and advanced technology to ensure seamless order processing, efficient inventory management, and reliable packaging and shipping processes. This commitment to excellence enables Amazon to deliver an exceptional customer experience and maintain its position as a leader in the e-commerce industry.
The Human Element in Amazon Fulfillment Center BFL1
While cutting-edge technology and automated processes drive the operations at Amazon Fulfillment Center BFL1, the human element remains crucial in maintaining high levels of efficiency, quality, and customer satisfaction.
Employee Roles and Responsibilities
Various roles and responsibilities are assigned to dedicated employees who work tirelessly to keep BFL1 running smoothly. From warehouse associates who handle inventory management and order fulfillment to quality control teams responsible for ensuring the accuracy of packages, each employee plays a vital role in delivering an exceptional customer experience. Collaborative teamwork among employees is encouraged, fostering a sense of cohesion within the center.
Training and Skill Development Initiatives
Recognizing the importance of continuous learning, Amazon invests in comprehensive training and skill development initiatives for employees at BFL1. New recruits undergo extensive onboarding programs that familiarize them with the center’s operations, safety protocols, and customer-centric values. Ongoing training ensures that employees stay up to date with the latest technologies and industry best practices, enabling them to adapt to evolving business needs and deliver superior service.
Safety Measures and Worker Welfare
Ensuring the safety and well-being of its employees is a top priority for Amazon Fulfillment Center BFL1. Robust safety protocols and measures are implemented throughout the facility, minimizing the risks associated with heavy machinery and high-volume operations. Regular safety training, ergonomic workstations, and health and wellness initiatives prioritize the welfare of employees, creating a conducive and safe working environment.
Technology and Automation at Amazon Fulfillment Center BFL1
Technology and automation have revolutionized the operations of Amazon Fulfillment Center BFL1, enhancing efficiency, accuracy, and scalability.
Use of Robotics in Warehouse Operations
BFL1 utilizes advanced robotic systems to optimize warehouse operations. Collaborative robots, or “cobots,” work side by side with human employees, assisting with inventory picking, transportation, and organization. These robots are equipped with sophisticated sensors that enable them to navigate complex warehouse layouts and execute tasks swiftly and accurately. By automating repetitive and physically demanding tasks, cobots free up human employees to focus on more complex and value-added activities.
Inventory Tracking and Management Systems
An efficient inventory tracking and management system forms the backbone of operations at BFL1. Real-time monitoring of stock levels, coupled with automated replenishment systems, ensures a continuous availability of products. RFID (Radio Frequency Identification) technology allows for quick and accurate inventory tracking, reducing the likelihood of stockouts and ensuring timely replenishments.
The Role of AI and Machine Learning
AI (Artificial Intelligence) and machine learning algorithms play a critical role in optimizing various aspects of the fulfillment process at BFL1. Advanced algorithms analyze historical data to predict customer demand patterns, enabling proactive inventory management. Machine learning algorithms also power recommendation systems that enhance cross-selling and up-selling opportunities, contributing to increased customer satisfaction and revenue growth.
In conclusion, Amazon Fulfillment Center BFL1 serves as a prime example of the innovative operations within Amazon’s fulfillment network. Through its unique features, efficient order processing, emphasis on employee training and welfare, and the integration of advanced technology and automation, BFL1 exemplifies the dedication to efficiency, accuracy, and customer satisfaction that drives the success of Amazon’s fulfillment centers.
Enhance Your Amazon Selling Experience with AI
As you’ve seen with Amazon Fulfillment Center BFL1, technology and AI are pivotal in streamlining operations and driving customer satisfaction. Your eCom Agent extends this innovative approach to individual Amazon Sellers. With our suite of AI tools, you can effortlessly develop better products, analyze customer feedback, and optimize your detail pages to stand out in the competitive Amazon marketplace. Why spend hours on tasks that can be automated? Subscribe to Your eCom Agent’s AI Tools today and transform your Amazon selling experience with the power of AI.