Amazon is renowned for its efficient and fast order fulfillment process. One of its flagship centers is AMA1, which plays a vital role in the company’s supply chain operations. Let’s take a closer look at how AMA1 operates and the various factors that contribute to its efficiency.
Understanding Amazon’s Fulfillment Process
Before delving into the specifics of AMA1, it is essential to grasp the significance of fulfillment centers in Amazon’s supply chain. These centers serve as the backbone of the company’s operations, enabling it to quickly and reliably deliver products to customers worldwide. Fulfillment centers like AMA1 are strategically located to optimize shipping times and ensure an uninterrupted supply chain.
Before we begin: Every Amazon Seller needs a suite of tools for Keyword Research, Product Development, and Listing Optimization. Our top pick is Helium 10 and readers of this post can get 20% off their first 6 months by clicking the image below.
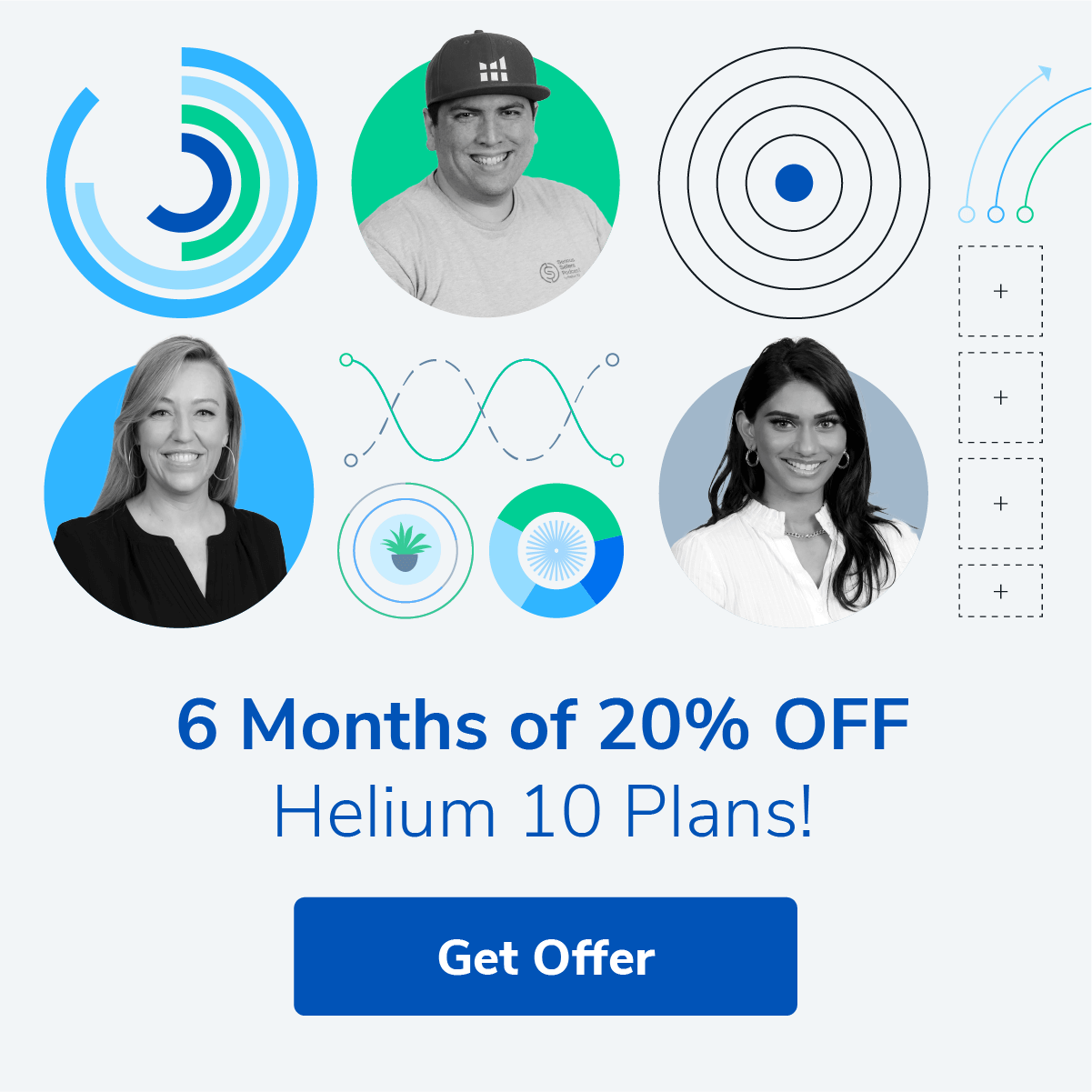
Amazon’s fulfillment centers play a crucial role in the company’s ability to meet customer demands efficiently. These centers act as central warehouses where goods from various suppliers are received, sorted, processed, and stored until they are ready for shipment. With their vast storage capacity and advanced logistics infrastructure, these centers streamline the order fulfillment process, ensuring that products are consolidated and prepared for rapid shipment.
One of the key components of Amazon’s fulfillment process is inventory management. When a customer places an order through Amazon’s online platforms, the order is received and processed. The order is then forwarded to the nearest fulfillment center, such as AMA1. At the fulfillment center, sophisticated inventory management systems come into play. These systems ensure that the necessary products are available and ready for shipping, minimizing delays and ensuring efficient order processing.
Once the products are ready for shipment, the fulfillment center’s operations team meticulously picks, packs, and labels the items. This process is carried out with utmost care and attention to detail, guaranteeing accuracy and timeliness. Each item is carefully inspected to ensure that it meets Amazon’s high standards of quality. The packaging is designed to protect the products during transit, minimizing the risk of damage.
Amazon’s fulfillment centers are equipped with state-of-the-art technology to facilitate the order fulfillment process. Automated sorting systems are utilized to efficiently categorize and organize the products. These systems can handle immense volumes of orders, ensuring that products are quickly and accurately sorted for shipment. The high-capacity storage facilities within the fulfillment centers enable Amazon to store a wide range of products, ensuring a diverse and extensive inventory.
Another crucial aspect of Amazon’s fulfillment process is the optimization of shipping times. Fulfillment centers like AMA1 are strategically located in close proximity to major transportation hubs and population centers. This strategic placement allows for faster delivery times, reducing the distance between the fulfillment center and the customer’s location. By minimizing the distance traveled, Amazon can deliver products to customers in a timely manner, meeting their expectations for fast and reliable shipping.
In conclusion, Amazon’s fulfillment centers, including AMA1, play a vital role in the company’s supply chain. These centers serve as central warehouses, streamlining the order fulfillment process and ensuring efficient delivery of products to customers worldwide. With advanced logistics infrastructure, inventory management systems, and strategic placement, Amazon can meet customer demands effectively and maintain its position as a leader in e-commerce.
A Closer Look at AMA1
AMA1, located at a strategic geographic location, plays a crucial role in Amazon’s logistics network. The primary goal of AMA1 is to optimize regional inventory management, ensuring products are readily available for efficient distribution in the surrounding areas.
Let’s delve deeper into the fascinating world of AMA1 and explore its location, infrastructure, workforce, and operations.
Location and Infrastructure of AMA1
AMA1 is strategically situated in a region with excellent transportation infrastructure, enabling rapid connectivity to nearby cities and major transportation routes. This advantageous location minimizes shipping times and ensures a quick delivery experience for customers.
But what makes this location truly remarkable is its proximity to key suppliers and manufacturers. Being in close proximity to these entities allows AMA1 to establish strong partnerships and streamline the supply chain process. This means that products can be sourced and restocked efficiently, reducing delays and ensuring a constant flow of inventory.
Now, let’s take a closer look at the facility itself. AMA1 boasts a sprawling warehouse that spans several acres. The facility is equipped with state-of-the-art technology, including advanced conveyor systems, automated storage and retrieval systems (AS/RS), and robotic assistance. These cutting-edge technologies work in harmony to optimize the flow of products, from the moment they arrive at the facility to the point of dispatch.
Inside the warehouse, products are meticulously organized and stored in designated areas. The AS/RS system plays a vital role in this process, efficiently retrieving and storing items with precision. This automation not only saves time but also minimizes the risk of errors, ensuring that the right products are always available for distribution.
Moreover, the facility is equipped with a sophisticated climate control system that maintains optimal temperature and humidity levels. This is particularly important for products that require specific storage conditions, such as perishable goods or sensitive electronics. By providing the ideal environment, AMA1 ensures that products remain in pristine condition throughout their journey in the facility.
Workforce and Operations at AMA1
The efficient operation of AMA1 would not be possible without its dedicated and skilled workforce. The employees at AMA1 are trained extensively to handle various aspects of the fulfillment process, including picking, packing, and quality control.
But it’s not just about individual skills; teamwork is also a crucial aspect of AMA1’s operations. The facility operates on a synchronized system, where different teams work together seamlessly to ensure smooth operations. From the moment an order is received to the final stages of packaging, every step is meticulously coordinated to meet customer expectations.
Continuous process optimization is another key factor that sets AMA1 apart. The facility regularly analyzes its operations and implements improvements to enhance efficiency and productivity. This includes fine-tuning the layout of the warehouse, optimizing inventory management systems, and leveraging data analytics to make informed decisions.
Feedback mechanisms are also in place to encourage a culture of continuous improvement. Employees at AMA1 are encouraged to provide suggestions and ideas for enhancing operations. This collaborative approach fosters innovation and ensures that best practices are implemented and shared across the entire facility.
In conclusion, AMA1 is not just a warehouse; it is a meticulously planned and executed logistics hub that optimizes regional inventory management. Its strategic location, advanced infrastructure, skilled workforce, and continuous process optimization make it an integral part of Amazon’s logistics network, ensuring efficient distribution and a seamless customer experience.
Efficiency Metrics of AMA1
AMA1’s efficiency is gauged by various metrics, which provide insights into its performance and operational effectiveness. Two key metrics that highlight AMA1’s efficiency are order processing time and inventory management.
Order Processing Time at AMA1
One of the crucial factors in Amazon’s success is its ability to process orders quickly. AMA1 excels in this aspect, with streamlined processes and advanced technology enabling rapid order processing. By minimizing the time between order placement and shipment, AMA1 ensures that customers receive their orders promptly, contributing to customer satisfaction and loyalty.
Inventory Management and Turnover Rate
AMA1’s inventory management practices are a crucial component of its efficiency. Through advanced inventory tracking systems and predictive analytics, AMA1 optimizes stock levels to ensure a high turnover rate. This strategy minimizes holding costs and reduces the risk of obsolete inventory, allowing Amazon to deliver the latest products to customers while maintaining cost-effectiveness.
Technological Innovations at AMA1
As technology continues to evolve, Amazon leverages cutting-edge innovations to further enhance the efficiency of AMA1.
Automation and Robotics in AMA1
Automation plays a significant role in Amazon’s fulfillment centers, including AMA1. The utilization of conveyor systems, automated picking robots, and smart shelving systems enables faster and more accurate order processing. Automated technologies work in harmony with human workers, empowering them to focus on higher-value tasks while eliminating repetitive and physically demanding activities.
Use of AI and Machine Learning in Operations
AI and machine learning technologies are integrated into various aspects of AMA1’s operations. These advanced systems analyze vast amounts of data to optimize processes, predict customer demand, and enhance inventory management. Furthermore, AI-powered algorithms enable dynamic routing optimization, ensuring that packages are efficiently transported to their destinations while minimizing both cost and delivery time.
Challenges and Solutions in AMA1’s Operations
Despite its high efficiency, AMA1 faces specific challenges in its daily operations. However, Amazon has proven adept in finding innovative solutions to overcome these obstacles and maintain optimal efficiency.
Overcoming Logistical Challenges at AMA1
The complexity of managing a vast array of products and ensuring their rapid delivery presents logistical challenges for AMA1. Amazon addresses these challenges by continuously refining its logistics network, utilizing predictive analytics to forecast demand accurately, and dynamically optimizing transportation routes. With data-driven decision-making and real-time monitoring, AMA1 can efficiently handle these logistical challenges on a daily basis.
Ensuring Worker Safety and Satisfaction
Worker safety and satisfaction are vital aspects of Amazon’s operations. At AMA1, extensive safety protocols are in place, including ergonomic workstations, automated machinery with safety features, and ongoing safety training programs. By prioritizing worker well-being and providing a supportive work environment, AMA1 ensures that its employees can perform their tasks efficiently and with satisfaction.
In conclusion, Amazon Fulfillment Center AMA1 comprises a complex network of efficient processes, advanced technology, and a dedicated workforce. By continuously optimizing its operations, investing in technological innovations, and addressing logistical challenges, AMA1 helps Amazon maintain its position as a leader in fast and reliable order fulfillment.
Enhance Your Amazon Business with AI
As you’ve seen with Amazon Fulfillment Center AMA1, efficiency and innovation are key to staying ahead in the e-commerce game. Your eCom Agent brings the power of AI directly to Amazon Sellers, offering tools that revolutionize product development, review analysis, and detail page enhancement. Embrace the future of e-commerce and subscribe to Your eCom Agent’s AI Tools today to transform your Amazon business with the speed and precision of artificial intelligence.