Amazon Fulfillment Centers are an integral part of the company’s operations. In this comprehensive guide, we will take a closer look at the DTW1 Amazon Fulfillment Center, exploring its functions, infrastructure, and environmental impact.
Understanding Amazon Fulfillment Centers
What is a Fulfillment Center?
Before we dive into the specifics of the DTW1 Amazon Fulfillment Center, let’s first understand what a fulfillment center is. A fulfillment center is a highly organized warehouse facility that plays a crucial role in the order fulfillment process. It is responsible for receiving, storing, and shipping products to customers.
Before we begin: Every Amazon Seller needs a suite of tools for Keyword Research, Product Development, and Listing Optimization. Our top pick is Helium 10 and readers of this post can get 20% off their first 6 months by clicking the image below.
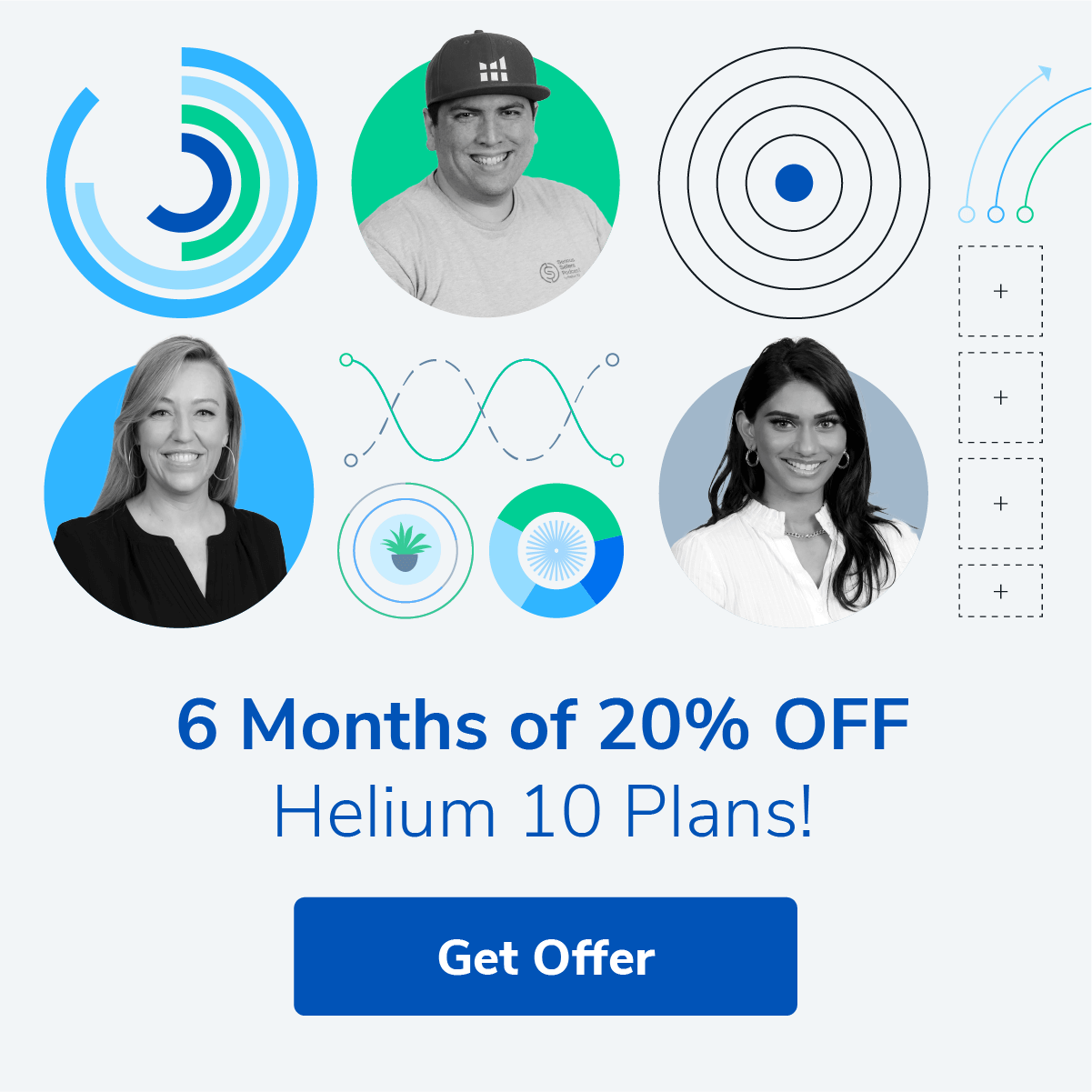
But what happens behind the scenes at a fulfillment center? Let’s take a closer look.
When a customer places an order on Amazon, the order is sent to the nearest fulfillment center that has the item in stock. Once the order arrives at the fulfillment center, it goes through a series of steps to ensure that the customer receives their package in a timely manner.
First, the products are received and checked for quality and quantity. This is an important step to ensure that customers receive exactly what they ordered. Once the products are verified, they are carefully stored in the fulfillment center’s inventory.
Next, when an order is placed, the products are picked from the inventory. This is done by highly efficient robots that navigate through the fulfillment center, retrieving the items and bringing them to the packing area.
At the packing area, the products are carefully packaged to protect them during transit. Amazon takes great care in ensuring that packages are well-protected, using a combination of packaging materials and techniques to prevent damage.
Finally, the packages are labeled and prepared for shipping. They are then handed over to the shipping carrier, who will deliver the package to the customer’s doorstep.
The Role of Fulfillment Centers in Amazon’s Operations
Amazon operates numerous fulfillment centers strategically located across the globe. These centers are the backbone of Amazon’s logistics network, enabling the efficient delivery of millions of products to customers worldwide. They are designed to handle a vast array of products, from books to electronics and everything in between.
But what makes Amazon’s fulfillment centers so efficient?
One key factor is the use of advanced technology. Amazon employs state-of-the-art robotics and automation systems to streamline the order fulfillment process. These robots work alongside human workers, increasing efficiency and reducing the time it takes to process orders.
Additionally, Amazon’s fulfillment centers are designed with optimization in mind. The layout of the centers is carefully planned to minimize the distance traveled by workers and robots, ensuring that orders are processed as quickly as possible.
Furthermore, Amazon’s fulfillment centers are equipped with advanced inventory management systems. These systems keep track of the location and quantity of each product in real-time, allowing for accurate and efficient order picking.
The primary goal of Amazon’s fulfillment centers is to ensure quick and accurate order processing. Through advanced technology and a well-trained workforce, Amazon fulfills customer orders with unparalleled speed and precision.
So the next time you receive a package from Amazon, take a moment to appreciate the intricate process that took place at a fulfillment center to get that package to your doorstep.
A Deep Dive into the DTW1 Amazon Fulfillment Center
Location and Infrastructure of DTW1
DTW1 is one of Amazon’s state-of-the-art fulfillment centers situated in Detroit, Michigan. Its strategic location allows for efficient distribution across the region, serving a large customer base.
The infrastructure of DTW1 is designed to maximize storage capacity and streamline operations. The facility spans over hundreds of thousands of square feet, accommodating racks upon racks of products ready for shipment. With its advanced layout and technology, DTW1 can process and ship hundreds of thousands of products each day.
But what makes DTW1 truly impressive is the level of detail that went into its design. The fulfillment center is equipped with cutting-edge automation systems that optimize the picking, packing, and shipping processes. This includes state-of-the-art conveyor belts, robotic arms, and sorting machines that work seamlessly together to ensure quick and accurate order fulfillment.
Furthermore, DTW1 has implemented innovative sustainability practices. The facility features energy-efficient lighting systems, solar panels on the roof, and rainwater harvesting systems. These initiatives not only reduce the center’s environmental impact but also contribute to cost savings and overall operational efficiency.
The Workforce Behind DTW1
At the heart of DTW1’s success is its dedicated workforce. The center employs a diverse group of individuals who work tirelessly to ensure prompt order fulfillment and exceptional customer service. From warehouse associates to managers, each employee plays a vital role in maintaining the center’s efficiency and productivity.
Amazon recognizes the importance of investing in its employees’ well-being. DTW1 provides a safe and inclusive work environment, offering competitive wages, comprehensive benefits packages, and opportunities for career growth. The company also prioritizes work-life balance, implementing flexible scheduling options and promoting employee wellness programs.
But it doesn’t stop there. DTW1 is committed to fostering a culture of continuous learning and development. Amazon provides comprehensive training programs to equip its workforce with the necessary skills to handle various tasks within the fulfillment center. Whether it’s operating the latest automated machinery or mastering inventory management systems, employees have access to ongoing educational resources that empower them to excel in their roles.
Moreover, DTW1 values diversity and inclusion. The fulfillment center actively promotes a diverse workforce, recognizing that different perspectives and experiences contribute to a more innovative and successful organization. Amazon’s commitment to diversity extends beyond the workplace, as the company actively engages with the local community through various outreach programs and partnerships.
In conclusion, the DTW1 Amazon Fulfillment Center in Detroit, Michigan, is not just a warehouse for storing and shipping products. It is a hub of innovation, efficiency, and employee empowerment. From its strategic location and advanced infrastructure to its dedicated workforce and commitment to sustainability, DTW1 represents Amazon’s relentless pursuit of excellence in the world of e-commerce fulfillment.
The Inner Workings of DTW1
Inventory Management at DTW1
Behind the scenes, DTW1 employs advanced inventory management systems to keep track of the millions of products stored within its walls. This ensures accurate inventory levels and minimizes the chances of stockouts. Efficient inventory management enables Amazon to fulfill customer orders promptly and maintain its reputation for reliable service.
At DTW1, inventory management is a complex and dynamic process. The facility is equipped with state-of-the-art technology that allows for real-time tracking of products. Every item is assigned a unique barcode or RFID tag, which is scanned and recorded as it enters or leaves the facility. This meticulous tracking system ensures that the inventory is always up-to-date and accurate.
Moreover, DTW1 utilizes sophisticated algorithms and predictive analytics to forecast demand and optimize inventory levels. By analyzing historical sales data, market trends, and customer preferences, the system can anticipate which products are likely to be in high demand and adjust the inventory accordingly. This proactive approach helps to prevent stockouts and ensures that popular items are always available for customers.
Order Processing and Shipping Procedures
When a customer places an order, the process of fulfilling that order begins at DTW1. From receiving the order to picking, packing, and shipping, each step is meticulously executed with the help of cutting-edge technology and a well-established workflow.
Upon receiving an order, it is immediately entered into the system, and the clock starts ticking. The order is then sorted and assigned to associates who specialize in different product categories. These associates are equipped with handheld devices that guide them to the exact location of the items within the vast warehouse.
Using advanced scanning technology, the associates scan the barcode or RFID tag of each item to ensure accuracy. The system cross-checks the scanned data with the order details, verifying that the correct products have been picked. This double-checking process minimizes the chances of errors and ensures that customers receive exactly what they have ordered.
Once the products are picked, they are carefully packaged and labeled for shipping. DTW1 has dedicated packing stations equipped with automated machines that precisely measure and cut the appropriate amount of packaging material for each item. This not only ensures that the products are well-protected during transit but also minimizes waste and environmental impact.
After the items are packaged, they are loaded onto conveyor belts that transport them to the shipping area. Here, the packages are sorted based on their destinations and loaded onto delivery trucks or handed over to shipping partners. DTW1 works closely with various shipping carriers to ensure that the packages are delivered to customers in a timely manner.
Throughout the entire order processing and shipping procedures, DTW1 maintains a high level of efficiency and accuracy. The facility operates 24/7, with dedicated teams working in shifts to ensure that customer orders are processed and shipped as quickly as possible.
Technological Innovations at DTW1
Automation and Robotics in DTW1
DTW1 incorporates automation and robotics to enhance its operational efficiency. Automated systems, such as conveyor belts and robotic arms, help streamline the movement of products throughout the facility. Robotics play a crucial role in minimizing human error and increasing productivity.
These technological advancements not only expedite the fulfillment process but also create a safer work environment for employees.
Advanced Tracking Systems
DTW1 employs advanced tracking systems that monitor the progress of packages from the moment they leave the fulfillment center until they reach the customer’s doorstep. This tracking technology allows customers to stay informed about their orders, providing a seamless shopping experience.
The Environmental Impact of DTW1
Energy Efficiency Measures at DTW1
Amazon places great emphasis on sustainability and energy efficiency. DTW1 incorporates various measures to minimize its environmental impact. These include energy-efficient lighting systems, solar panels, and optimized heating and cooling systems. By reducing energy consumption, DTW1 contributes to a greener future.
Waste Management and Recycling Initiatives
Another aspect of DTW1’s commitment to sustainability is its waste management and recycling initiatives. The facility encourages recycling and proper disposal of waste materials, aiming to reduce its ecological footprint. By implementing effective waste management practices, DTW1 demonstrates Amazon’s dedication to environmental responsibility.
Closing Thoughts
The DTW1 Amazon Fulfillment Center is a prime example of Amazon’s commitment to efficient, precise, and sustainable operations. From its location and infrastructure to its dedicated workforce and technological innovations, DTW1 showcases the meticulous planning and execution that goes into the fulfillment process. As Amazon continues to expand its fulfillment network, the DTW1 Amazon Fulfillment Center remains a vital hub in enabling seamless order fulfillment for customers around the world.
Enhance Your Amazon Operations with AI
As you’ve seen with the DTW1 Amazon Fulfillment Center, efficiency and innovation are key to staying ahead in the competitive world of e-commerce. Your eCom Agent brings this same level of meticulous planning and execution to your fingertips. With our suite of AI tools designed for Amazon Sellers, you can revolutionize the way you develop products, analyze customer feedback, and optimize your detail pages. Embrace the power of AI and transform hours of work into seconds of simplicity. Subscribe to Your eCom Agent’s AI Tools today and take your Amazon business to the next level.