The Amazon Fulfillment Center in San Diego is a massive facility that plays a crucial role in enabling Amazon’s efficient supply chain and ensuring prompt deliveries to customers. In this comprehensive guide, we will explore the inner workings of this fulfillment center, from its key features and layout to the technology powering its operations. We will also delve into the roles and responsibilities of the employees who work tirelessly to keep the center running smoothly. Additionally, we will discuss the impact of the San Diego center on the local economy, including job creation and environmental considerations. Finally, we will look ahead to the future of Amazon Fulfillment Centers, examining potential technological advancements and expansion plans.
Understanding Amazon’s Fulfillment Process
The heart of Amazon’s success lies in its highly efficient and streamlined fulfillment process. Fulfillment centers like the one in San Diego are the backbone of this process, handling everything from receiving inventory to packing and shipping customer orders.
Before we begin: Every Amazon Seller needs a suite of tools for Keyword Research, Product Development, and Listing Optimization. Our top pick is Helium 10 and readers of this post can get 20% off their first 6 months by clicking the image below.
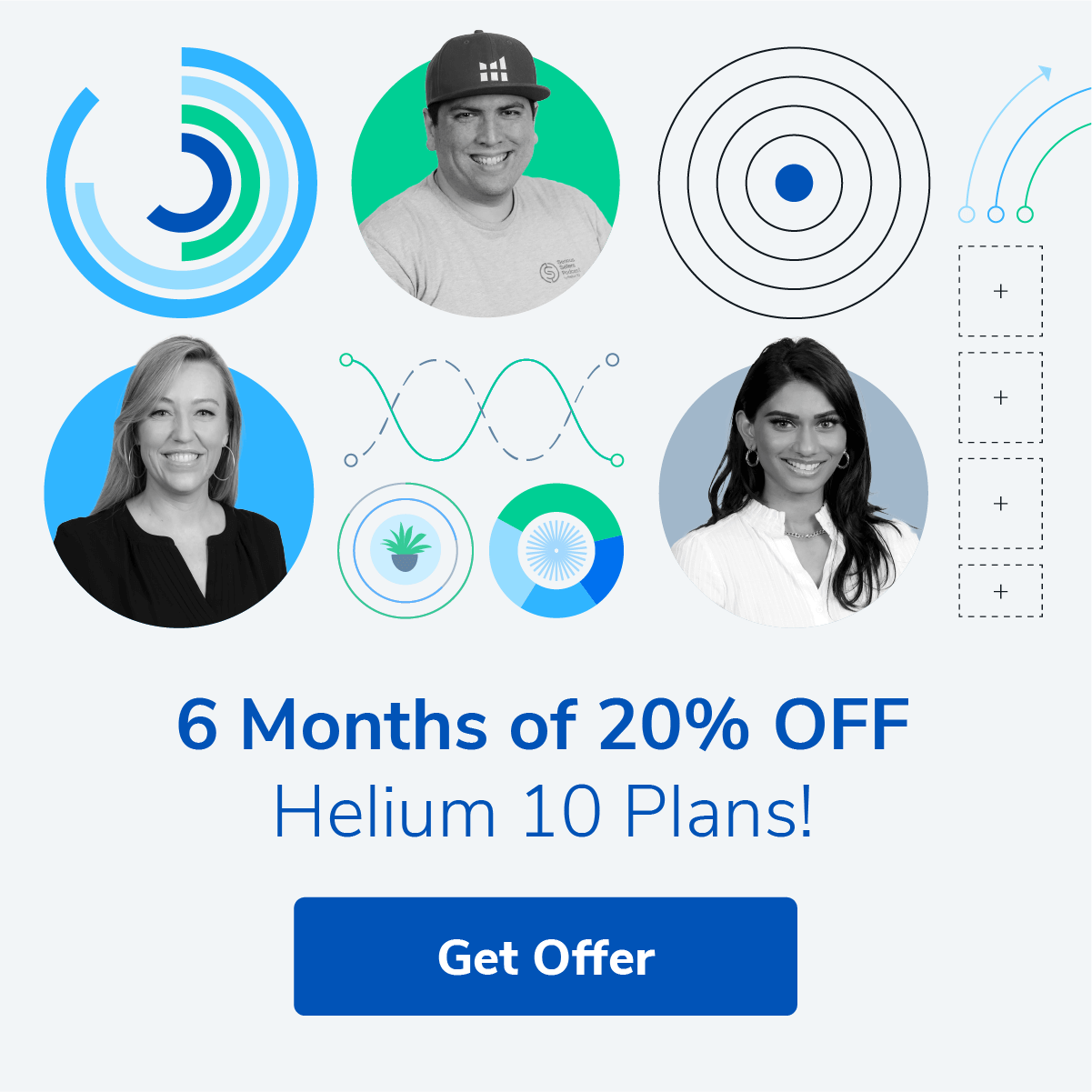
The Role of Fulfillment Centers in Amazon’s Supply Chain
In Amazon’s vast supply chain network, fulfillment centers serve as the epicenter of logistics. Goods from suppliers are received at these centers, where they are stored and organized until they are ready to be shipped to customers. These centers play a vital role in ensuring that products reach customers promptly and in optimal condition.
At the San Diego fulfillment center, for example, the facility spans over 1 million square feet, making it one of the largest in Amazon’s network. With its strategic location near major transportation hubs, it serves as a crucial distribution point for customers in the Southern California region.
Key Features of Amazon Fulfillment Centers
Amazon Fulfillment centers are designed with efficiency and productivity in mind. They are typically massive structures, spanning hundreds of thousands of square feet, equipped with state-of-the-art technology and machinery. These centers feature advanced robotics and automated systems that enhance the speed and accuracy of order fulfillment.
Within these fulfillment centers, products are meticulously organized and stored using sophisticated inventory management systems. Each item is assigned a unique barcode, allowing for seamless tracking and retrieval when an order is placed. The use of advanced robotics further optimizes the storage and retrieval process, ensuring that products are readily available for shipping.
Moreover, Amazon’s fulfillment centers are strategically located near major population centers, enabling faster delivery times. This strategic placement minimizes the distance between the fulfillment centers and customers, reducing transit times and enhancing the overall customer experience.
Efficiency is further enhanced through the use of cutting-edge technology, such as automated sorting systems and conveyor belts. These systems enable the seamless movement of products throughout the fulfillment center, minimizing manual handling and reducing the risk of errors.
Additionally, Amazon’s fulfillment centers prioritize sustainability and environmental responsibility. They are equipped with energy-efficient lighting systems, utilize renewable energy sources, and implement waste reduction initiatives. By integrating sustainable practices into their operations, Amazon aims to minimize its environmental impact while meeting the growing demands of its customers.
A Deep Dive into the San Diego Fulfillment Center
The San Diego Fulfillment Center, located on the West Coast, is a crucial facility for Amazon’s operations. Let’s explore this center in detail to understand its significance and inner workings.
Layout and Design of the San Diego Center
The layout and design of the San Diego Fulfillment Center are meticulously planned to ensure maximum efficiency. The facility is divided into various sections, each dedicated to specific tasks such as receiving, storage, packing, and shipping. This strategic layout allows for a seamless and uninterrupted flow of goods throughout the center.
Upon entering the center, the receiving section is the first stop for incoming shipments. Here, a team of skilled workers carefully inspects and scans each item to ensure accuracy and quality control. The items are then sorted and transported to their designated storage areas.
The storage section of the center is a vast expanse of shelves and racks, meticulously organized to accommodate a wide range of products. Advanced inventory management systems keep track of each item’s location, ensuring efficient retrieval when needed.
Adjacent to the storage area is the packing section, where a well-coordinated team of workers prepares orders for shipment. This section is equipped with state-of-the-art packing stations, complete with automated tape dispensers, weighing scales, and label printers. The workers carefully package each item, ensuring it is secure and ready for transportation.
Once the orders are packed, they are swiftly moved to the shipping section. Here, advanced conveyor systems transport the packages to the loading docks, where they are loaded onto trucks for delivery. The entire process, from receiving to shipping, is meticulously orchestrated to minimize delays and maximize efficiency.
The Technology Powering the Center
The San Diego Fulfillment Center is at the forefront of technological innovation. Cutting-edge robotics and automated systems play a crucial role in streamlining operations and enhancing productivity.
Throughout the center, advanced robotic systems work alongside human employees to handle various tasks. These robots are equipped with sophisticated sensors and algorithms, allowing them to navigate the facility autonomously. They assist in tasks such as inventory management, efficiently locating and retrieving items from the storage area, and delivering them to the packing section.
Additionally, automated systems are employed to optimize the picking and packing process. These systems use advanced algorithms to determine the most efficient route for workers to pick items from the shelves. This minimizes travel time and maximizes productivity, ensuring that orders are processed quickly and accurately.
Another remarkable technological feature of the San Diego Fulfillment Center is the product sorting system. As packages move through the center, they pass through automated sorting machines that use barcode scanning and computer vision technology to identify and sort them based on their destination. This ensures that packages are correctly routed for timely delivery.
The San Diego Fulfillment Center stands as a testament to Amazon’s commitment to innovation and operational excellence. Its carefully planned layout and utilization of cutting-edge technology contribute to its efficient and seamless operations. As Amazon continues to evolve and expand, centers like this play a crucial role in delivering a wide range of products to customers across the West Coast.
The People Behind the Operations
While technology plays a significant role in Amazon’s fulfillment process, it is the dedicated employees who bring it all together.
Behind the scenes of Amazon’s fulfillment center in San Diego, a bustling hive of activity takes place. The center is home to a diverse workforce, each member playing a crucial role in ensuring that customer orders are fulfilled accurately and efficiently.
Roles and Responsibilities of Employees
Within the fulfillment center, various roles exist, each contributing to the smooth operations of the facility. From the moment inventory arrives at the center, it is the responsibility of the receiving team to carefully inspect and verify the items. These meticulous individuals ensure that every product meets Amazon’s high standards before it is made available for purchase.
Once the inventory has been inspected and approved, it is then organized and stored in the vast warehouse. This task falls upon the warehouse team, who meticulously categorize and arrange the products, creating a well-structured system that allows for easy retrieval when orders are placed.
When an order is received, it is the pickers’ responsibility to locate the requested items within the warehouse. Armed with handheld scanners and a keen eye for detail, these individuals navigate the aisles, swiftly gathering the products to be packaged.
Next, the packers step in, carefully wrapping and securing each item in preparation for shipment. They ensure that fragile items are adequately protected, using bubble wrap and other packaging materials to safeguard the products during transit.
Finally, the shipping team takes over, preparing the packages for delivery. They work closely with logistics partners to ensure that the orders are dispatched promptly and reach customers in a timely manner.
Training and Safety Measures for Workers
Amazon places a high priority on the safety and well-being of its workforce. Employees at the San Diego Fulfillment Center undergo comprehensive training programs to ensure they are equipped with the necessary skills to perform their roles effectively.
During the training process, new employees learn about the various tasks they will be responsible for and receive hands-on experience in using the specialized equipment and technology within the center. They are taught best practices for inventory management, order fulfillment, and customer service, ensuring that they are well-prepared to handle any situation that may arise.
Additionally, the fulfillment center is equipped with state-of-the-art safety measures and protocols to minimize workplace accidents and injuries. From automated machinery with built-in safety features to clearly marked walkways and emergency exits, every effort is made to create a secure working environment.
Regular safety drills and ongoing safety training sessions are conducted to keep employees updated on the latest safety procedures and to reinforce the importance of maintaining a safe workplace. Amazon’s commitment to safety extends beyond the walls of the fulfillment center, as the company actively promotes a culture of safety and encourages employees to prioritize their well-being both on and off the job.
The Impact of the San Diego Center on Local Economy
The San Diego Fulfillment Center has had a significant impact on the local economy since its opening.
Job Creation and Economic Growth
The center has created numerous job opportunities for the residents of San Diego and the surrounding areas. These jobs span a wide range of skill levels and provide employment for individuals from diverse backgrounds. The center’s presence has contributed to economic growth in the region, providing a stable source of income for many families.
Environmental Considerations and Sustainability Efforts
Amazon is committed to sustainability, and the San Diego Fulfillment Center exemplifies this commitment. The center incorporates eco-friendly practices, such as energy-efficient lighting and waste management systems, to reduce its impact on the environment. Furthermore, Amazon continues to invest in renewable energy sources to power its fulfillment centers, including solar panels and wind farms.
Future of Amazon Fulfillment Centers
As technology continues to evolve, so does the future of Amazon Fulfillment Centers.
Technological Innovations on the Horizon
Amazon is constantly exploring cutting-edge technologies to enhance efficiency and improve customer satisfaction. From utilizing artificial intelligence for inventory management to implementing advanced delivery systems like drones, the future promises exciting innovations that will revolutionize the fulfillment process.
Expansion Plans and Potential Locations
With its ever-growing customer base, Amazon is continually expanding its fulfillment center network to meet increasing demands. As the company explores new markets and expands globally, new fulfillment centers are expected to emerge in strategic locations, ensuring faster deliveries and greater customer satisfaction.
In conclusion, the Amazon Fulfillment Center in San Diego is an integral part of Amazon’s worldwide logistics network. Its efficient operations, driven by advanced technology and dedicated employees, ensure that customers receive their orders promptly and in excellent condition. The center’s impact extends beyond the realm of commerce, making a positive contribution to the local economy and striving towards sustainability. As the future unfolds, Amazon’s fulfillment centers will continue to evolve, embracing new technologies and expanding their footprint to serve customers around the world efficiently.
Enhance Your Amazon Selling Experience with AI
As you’ve seen, Amazon’s fulfillment centers are marvels of efficiency, driven by the latest in technological innovation. If you’re an Amazon Seller looking to harness the power of AI to streamline your operations, Your eCom Agent is your solution. Our suite of AI tools is designed to help you develop better products, analyze customer feedback, and optimize your detail pages with unprecedented speed and accuracy. Ready to transform your Amazon business? Subscribe to Your eCom Agent’s AI Tools today and experience the future of e-commerce.