In this article, we will take a closer look at the operations of the Amazon Fulfillment Center in Chicago. This facility plays a vital role in Amazon’s supply chain, ensuring efficient order fulfillment and timely delivery to customers. We will delve into the process of how Amazon fulfills orders, explore the layout and design of the Chicago Fulfillment Center, discuss the human element involved in its operations, examine its impact on the local economy and environment, and explore its future plans and advancements.
Understanding Amazon’s Fulfillment Process
At the heart of Amazon’s success is its highly efficient fulfillment process. Fulfillment centers like the one in Chicago are essential components of Amazon’s supply chain, serving as strategic hubs for receiving, storing, and shipping products to customers. These centers employ advanced technology and carefully designed processes to streamline operations and ensure speedy delivery.
Before we begin: Every Amazon Seller needs a suite of tools for Keyword Research, Product Development, and Listing Optimization. Our top pick is Helium 10 and readers of this post can get 20% off their first 6 months by clicking the image below.
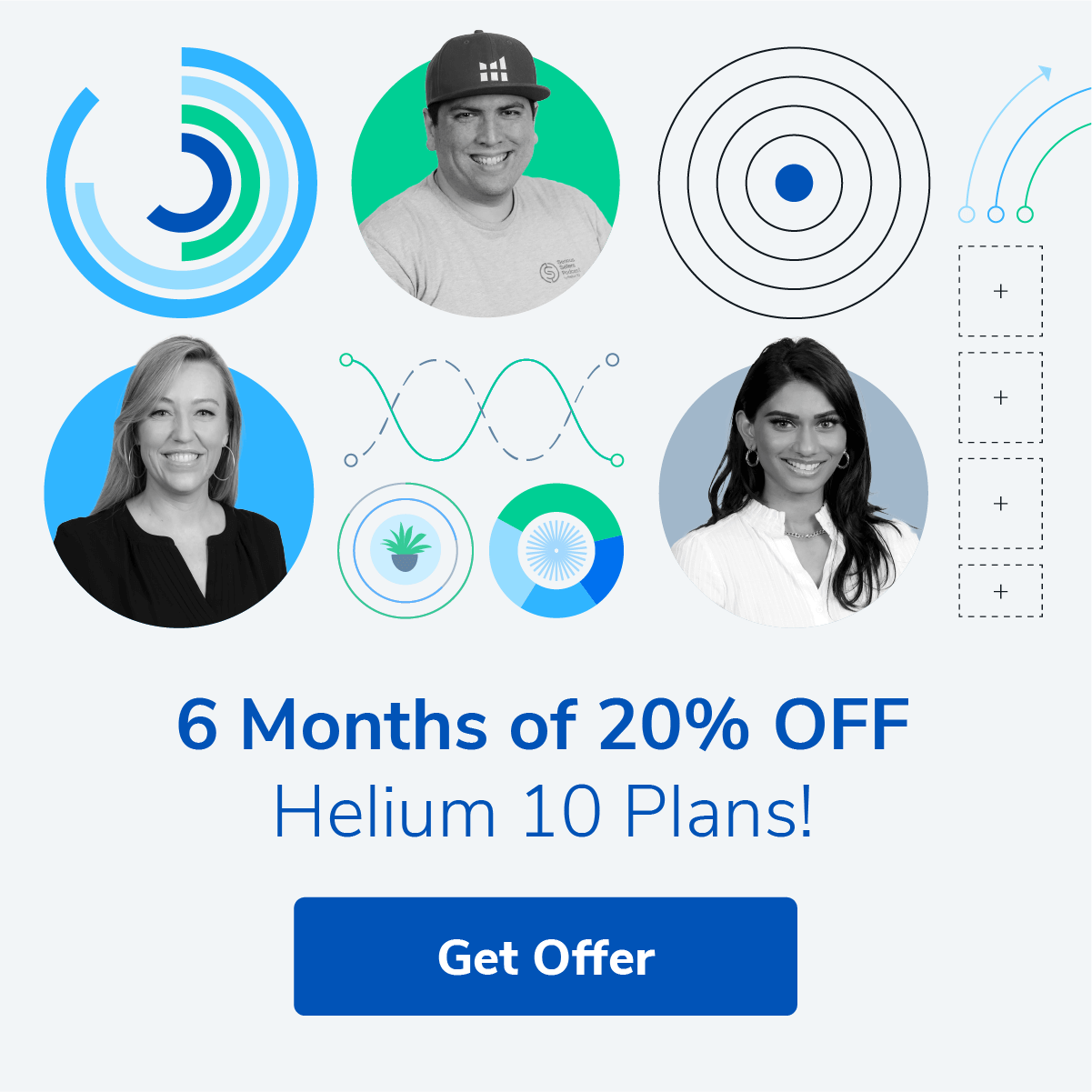
Let’s take a closer look at the fascinating world of Amazon’s fulfillment centers and the role they play in the company’s supply chain.
The Role of Fulfillment Centers in Amazon’s Supply Chain
Fulfillment centers act as key intermediaries between the vast network of Amazon sellers and the end customers. They receive products from sellers, store them in warehouses, and fulfill orders as they come in. These centers help Amazon maintain a large inventory and ensure availability of products to meet customer demands.
Imagine a bustling fulfillment center, with workers diligently sorting through incoming shipments, carefully organizing products on shelves, and preparing them for their journey to customers’ doorsteps. These centers are meticulously designed to maximize storage capacity and minimize the time it takes to locate and retrieve items for shipping.
Each fulfillment center is like a well-oiled machine, with various departments working in harmony to ensure smooth operations. From receiving and inventory management to order processing and shipping, every step is meticulously planned and executed to maintain Amazon’s reputation for fast and reliable delivery.
The Key Components of Amazon’s Fulfillment Process
A well-coordinated series of steps powers Amazon’s fulfillment process. It starts with receiving products, followed by inventory management, order processing, picking and packing, and finally, shipping. The entire process is optimized to minimize errors, reduce shipping time, and deliver a seamless experience to customers.
When products arrive at a fulfillment center, they go through a meticulous receiving process. Each item is carefully inspected for any damage or discrepancies, ensuring that customers receive only the highest quality products. This attention to detail is a testament to Amazon’s commitment to customer satisfaction.
Once the products are received, they are stored in vast warehouses, where advanced inventory management systems keep track of their location and quantity. This real-time tracking allows Amazon to efficiently fulfill orders and prevent stockouts, ensuring that customers can find the products they need when they need them.
When an order is placed, the picking and packing process begins. Workers in the fulfillment center use advanced technology, such as handheld scanners and automated sorting systems, to locate the ordered items quickly and accurately. They carefully pack the products, ensuring they are well-protected for their journey to the customer.
Finally, the packaged products are handed over to the shipping department, where they are sorted and dispatched to the appropriate carrier for delivery. Amazon’s extensive logistics network ensures that packages are efficiently routed to the nearest distribution centers or directly to customers’ addresses, minimizing transit time and optimizing the delivery process.
As you can see, Amazon’s fulfillment process is a well-orchestrated symphony of technology, logistics, and dedicated workers. It is this meticulous attention to detail and commitment to customer satisfaction that has made Amazon the e-commerce giant it is today.
Inside the Chicago Fulfillment Center
Welcome to the fascinating world of the Chicago Fulfillment Center, where efficiency and precision reign supreme. Let’s take a closer look at the inner workings of this state-of-the-art facility and discover the secrets behind its success.
The Layout and Design of the Center
Spread across a vast expanse, the Chicago Fulfillment Center is a marvel of meticulous planning and strategic organization. Every square inch of this facility has been carefully designed to optimize efficiency and ensure smooth operations.
As you step inside, you’ll be greeted by a sprawling layout that is divided into distinct sections, each dedicated to a specific aspect of the fulfillment process. The receiving area is where the journey begins for incoming products, as they are carefully inspected and sorted with utmost precision.
From there, the products are seamlessly transported to the storage area, where they await their turn to be picked and packaged. The storage section is a marvel in itself, with towering shelves that stretch as far as the eye can see. Advanced inventory management systems ensure that products are easily accessible, minimizing the time taken to retrieve them.
Next, we move on to the packaging area, where skilled workers and cutting-edge technology come together to prepare products for their final journey. Here, attention to detail is paramount, as each item is meticulously wrapped, labeled, and prepared for shipping. The packaging process is a well-choreographed dance of efficiency, ensuring that every package is secure and ready to embark on its journey to the customer.
Finally, we reach the outbound shipping area, where the magic happens. This bustling section is a hive of activity, with packages being sorted, loaded onto trucks, and dispatched to their eagerly awaiting recipients. The Chicago Fulfillment Center’s strategic location allows for seamless connectivity to a vast network of transportation options, ensuring speedy and reliable delivery.
The Role of Automation and Robotics
At the heart of the Chicago Fulfillment Center’s success lies the seamless integration of automation and robotics. These cutting-edge technologies play a pivotal role in streamlining operations, increasing efficiency, and reducing the risk of human errors.
Advanced robotics are deployed throughout the facility, taking on repetitive tasks that would otherwise be time-consuming and prone to mistakes. These robotic assistants work tirelessly, swiftly navigating the towering shelves of the storage area to retrieve products with pinpoint accuracy. Their precision and speed ensure that orders are fulfilled promptly, even during peak demand periods.
But it’s not just the robots that make automation a game-changer. The Chicago Fulfillment Center boasts a sophisticated network of conveyor belts, automated sorting systems, and state-of-the-art machinery that seamlessly handle the flow of products from one area to another. This harmonious blend of technology and human expertise creates a well-oiled machine that can handle a staggering volume of orders with ease.
Moreover, automation and robotics have another significant benefit – they free up human workers to focus on tasks that require creativity, problem-solving, and a personal touch. By taking care of the repetitive and mundane aspects of the fulfillment process, these technologies empower the workforce to deliver exceptional customer experiences and ensure that every order is handled with care.
So, as you can see, the Chicago Fulfillment Center is not just a warehouse. It is a meticulously designed, technologically advanced hub of efficiency that brings together the best of human expertise and cutting-edge automation. Behind its walls, a symphony of operations takes place, ensuring that your orders are fulfilled swiftly and accurately, leaving you with nothing but satisfaction.
The Human Element in Amazon’s Fulfillment Centers
While automation and robotics are vital, the human workforce remains an integral part of Amazon’s fulfillment operations. Let’s take a closer look at the roles and responsibilities of employees.
Employee Roles and Responsibilities
Within the Chicago Fulfillment Center, employees have diverse roles, including receiving and inspecting products, managing inventory, supervising packaging operations, ensuring quality control, and managing overall operations. Their expertise and attention to detail are crucial in maintaining efficiency and order accuracy.
Working Conditions and Employee Satisfaction
Amazon places great emphasis on providing safe and healthy working conditions for its employees. The Chicago Fulfillment Center offers a clean and well-maintained workspace, prioritizing employee well-being. Furthermore, the company strives to foster a positive working environment and provides various employee benefits and opportunities for growth, ensuring high levels of job satisfaction.
The Impact of the Fulfillment Center on Chicago
Amazon’s Fulfillment Center in Chicago not only enables efficient order fulfillment but also has a significant impact on the local economy and environment.
Economic Contributions and Job Creation
The Chicago Fulfillment Center has created numerous job opportunities for the local community. These positions range from entry-level warehouse roles to specialized positions in management and operations. Additionally, the center’s operations contribute to the local economy through increased spending on resources, utilities, and transportation services.
Environmental Considerations and Sustainability Efforts
As a responsible corporate citizen, Amazon is committed to environmental sustainability. The Fulfillment Center in Chicago incorporates eco-friendly practices such as energy-efficient lighting, waste recycling, and sustainable packaging. By implementing these measures, Amazon aims to minimize its carbon footprint and contribute to a greener future.
The Future of Amazon’s Fulfillment Centers
Looking ahead, Amazon continues to invest in cutting-edge technologies and innovate its fulfillment processes.
Technological Advancements and Future Plans
Amazon continually explores new technologies to enhance its fulfillment operations. This includes further integration of automation, machine learning algorithms to optimize inventory management, and the utilization of drones for last-mile delivery. These advancements aim to improve efficiency, reduce costs, and enhance the overall customer experience.
Expansion Plans and Potential Impact
As customer demands evolve, Amazon plans to expand its fulfillment center network to cater to the growing needs of its customers effectively. This expansion will create additional job opportunities in various locations and further contribute to the economic development of those regions.
In conclusion, the Amazon Fulfillment Center in Chicago serves as a vital cog in Amazon’s supply chain, ensuring seamless order fulfillment and timely delivery. Through advanced technology, carefully planned layouts, and a dedicated workforce, the center exemplifies the efficiency and scalability of Amazon’s operations. Furthermore, the center’s positive impact on the economy, environment, and future advancements showcases Amazon’s commitment to innovation and sustainability.
Enhance Your Amazon Selling Experience with AI
As you’ve seen, Amazon’s Fulfillment Centers are at the forefront of efficiency and innovation, much like Your eCom Agent’s suite of AI tools designed for Amazon Sellers. Embrace the power of artificial intelligence to refine your product development, analyze customer feedback, and optimize your detail pages with ease. With Your eCom Agent, tasks that once took hours can now be accomplished in seconds. Don’t get left behind in the competitive world of e-commerce. Subscribe to Your eCom Agent’s AI Tools today and transform your Amazon business with the speed and precision of AI.