If you’ve ever wondered how Amazon manages to deliver millions of packages to customers around the world with astonishing speed, the answer lies in their massive network of fulfillment centers. These fulfillment centers are the backbone of Amazon’s supply chain, ensuring that products are efficiently received, processed, and shipped to customers. In this comprehensive overview, we will take a deep dive into the ALB1 Amazon Fulfillment Center to understand the intricacies of its operations and the impact it has on Amazon’s overall performance.
Understanding the Amazon Fulfillment Process
Before we delve into the specifics of ALB1, it’s important to have a solid understanding of Amazon’s fulfillment process as a whole. At a high level, the process can be divided into several stages: receiving, stowing, picking, packing, and shipping.
Before we begin: Every Amazon Seller needs a suite of tools for Keyword Research, Product Development, and Listing Optimization. Our top pick is Helium 10 and readers of this post can get 20% off their first 6 months by clicking the image below.
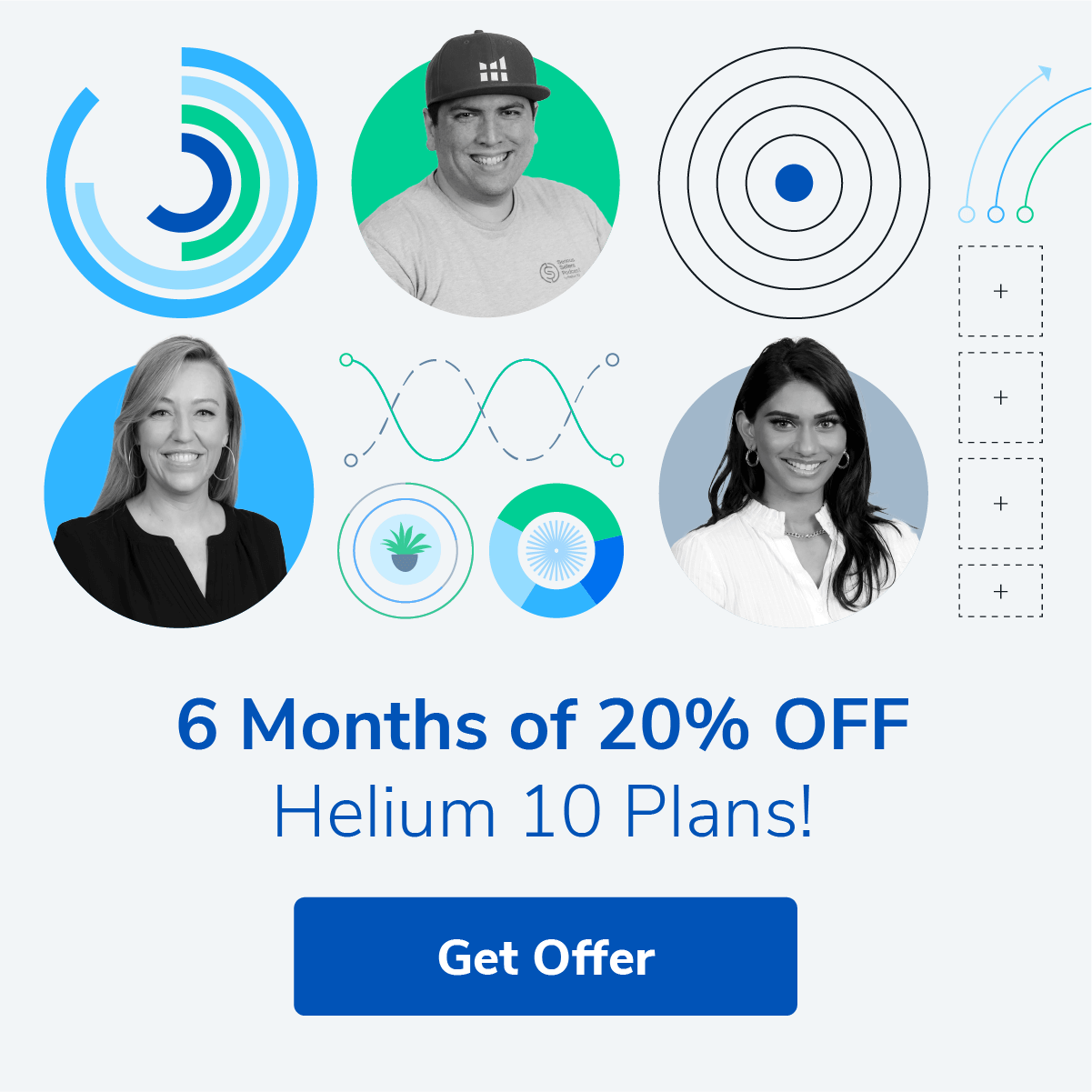
When products arrive at a fulfillment center, they go through a meticulous receiving process. Each item is carefully checked for accuracy and quality before being sorted and stored in designated areas. This attention to detail ensures that only the best products make it into Amazon’s inventory.
Next comes the stowing stage, where products are organized and placed in bins within the fulfillment center. This strategic placement ensures efficient retrieval during the picking stage, where products are selected and prepared for shipment. The stowing process involves careful consideration of factors such as product size, weight, and popularity to optimize the layout of the fulfillment center.
Once products have been picked, they move on to the packing stage. Here, they are carefully packaged, often with the help of automated systems, to ensure proper protection during transit. Amazon’s packing process is designed to minimize waste and maximize efficiency, with packaging materials tailored to the specific dimensions of each item.
Finally, the packaged items are labeled and prepared for shipping. Amazon’s shipping process is highly streamlined, with packages being sorted and assigned to the most appropriate carrier based on factors such as destination, package size, and delivery speed. This ensures that each package reaches its destination in the most efficient and cost-effective manner.
The Role of Fulfillment Centers in Amazon’s Supply Chain
Fulfillment centers play a vital role in Amazon’s supply chain by acting as distribution hubs for products across the globe. With strategically located centers like ALB1, Amazon is able to store inventory closer to customers, thereby reducing delivery times and costs. This proximity to customers also allows for faster order processing and improved customer satisfaction.
These centers serve as the connection point between suppliers and customers, enabling Amazon to efficiently manage inventory, fulfill orders, and handle returns. By streamlining these processes, fulfillment centers contribute to Amazon’s ability to provide fast and reliable service to its customers. Additionally, fulfillment centers play a crucial role in supporting Amazon’s Prime membership program, which offers expedited shipping and other benefits to subscribers.
The Unique Features of Amazon’s Fulfillment Process
One of the most notable features of Amazon’s fulfillment process is its use of advanced automation and robotics. ALB1, like many other centers, employs state-of-the-art technology to optimize operations and enhance efficiency. Automation and robotics play a key role in various stages of the fulfillment process, such as stowing and picking.
Automated systems can quickly and accurately place items in bins, while robots equipped with sensors and artificial intelligence assist in retrieving products for orders. These robots are capable of navigating the fulfillment center’s layout and efficiently picking items from shelves, significantly reducing the time it takes to fulfill an order. This high level of automation allows Amazon to handle a large volume of orders with precision and speed.
In addition to automation, Amazon’s fulfillment centers utilize sophisticated software systems that facilitate inventory management, order tracking, and real-time data analysis. These systems enable seamless coordination between various teams and ensure timely and accurate fulfillment of customer orders. By leveraging technology and data, Amazon can continuously optimize its fulfillment process and provide an exceptional customer experience.
A Deep Dive into the ALB1 Fulfillment Center
Located in the heart of Amazon’s vast network, the ALB1 Fulfillment Center is a prime example of efficiency and innovation. Situated strategically to serve customers in its region, ALB1 boasts an impressive physical structure and a dedicated workforce.
The Location and Structure of ALB1
ALB1 is strategically located in an area that provides easy access to major transportation routes. This enables quick and efficient delivery of products to customers in the surrounding regions.
But the location of ALB1 is not just about convenience. It is also about sustainability. The fulfillment center is designed to minimize its carbon footprint, with energy-efficient lighting and HVAC systems, as well as solar panels on the roof to generate clean energy.
The facility itself spans several acres, housing a vast storage space for products, as well as state-of-the-art technology and machinery. Its layout is optimized for smooth flow of products, with designated areas for receiving, stowing, picking, packing, and shipping.
Within the facility, there are specialized zones for different types of products. Temperature-controlled areas ensure that perishable items are stored at the optimal conditions, while secure sections are dedicated to high-value products.
The Daily Operations at ALB1
Behind the scenes, ALB1 operates around the clock to ensure seamless processing of customer orders. A dedicated team of employees, working in shifts, manages the various stages of the fulfillment process, collaborating with automated systems and robotics to maintain efficiency.
But it’s not just the human workforce that keeps ALB1 running smoothly. The fulfillment center is equipped with advanced robotics that assist in tasks such as picking and packing. These robots work alongside employees, enhancing productivity and reducing the risk of injuries.
From the moment products arrive at ALB1, they undergo thorough inspections to ensure quality and accuracy. Each item is then assigned a specific location within the facility, allowing for easy tracking and retrieval.
But what happens when a customer places an order? At ALB1, the process is streamlined and optimized for speed. When an order is received, it is immediately sent to the picking area, where employees and robots work together to gather the items from their designated locations.
Once the items are picked, they are carefully packed in sturdy boxes, taking into consideration the size and fragility of each product. ALB1 uses advanced packing algorithms to optimize space and minimize waste, ensuring that packages are secure and compact.
Throughout the day, employees work diligently to pick, pack, and ship customer orders. As each order is processed, it undergoes rigorous quality checks to guarantee that customers receive exactly what they ordered.
But the fulfillment process doesn’t end there. ALB1 also takes pride in its commitment to sustainability. The fulfillment center actively promotes recycling and waste reduction, with dedicated areas for sorting and recycling materials. Additionally, ALB1 partners with local charities to donate any unsold or returned products that are still in good condition.
ALB1 Fulfillment Center is not just a place where products are stored and shipped. It is a hub of innovation, where technology and human expertise come together to deliver exceptional customer experiences. With its strategic location, efficient operations, and commitment to sustainability, ALB1 sets the standard for fulfillment centers worldwide.
The Technology Behind ALB1
Automation and robotics are at the forefront of ALB1’s operations. The facility is equipped with cutting-edge technology that improves efficiency, accuracy, and the overall customer experience.
Automation and Robotics at ALB1
ALB1 utilizes a vast array of automated systems and robotics to optimize various tasks within the fulfillment process. Automated conveyor belts and sorting systems efficiently transport products throughout the facility, ensuring swift movement and minimizing the risk of errors.
Robots equipped with advanced sensors and artificial intelligence work alongside employees, aiding in picking and packaging activities. These robots are trained to navigate the facility, identify and retrieve specific products, and collaborate seamlessly with human workers.
The Software Systems Powering ALB1
In addition to automation and robotics, ALB1 relies on robust software systems to manage inventory, track orders, and analyze data in real-time. These systems enable accurate forecasting, efficient inventory replenishment, and streamlined coordination between different teams.
By integrating data from multiple sources, the software systems help optimize ALB1’s operations, alerting the workforce when stocks are running low, streamlining the picking process, and identifying areas for further improvement.
The Workforce of ALB1
Behind every successful fulfillment center is a dedicated and skilled workforce. ALB1 is no exception, relying on highly trained individuals to ensure the smooth functioning of operations.
Roles and Responsibilities within the ALB1 Team
The ALB1 team consists of individuals with diverse roles and responsibilities, all working together to achieve efficient order fulfillment. From management and supervisory positions to warehouse associates and technicians, each employee has a vital role to play.
Leadership at ALB1 oversees the entire operation, ensuring that all tasks are executed according to Amazon’s high standards. Warehouse associates handle the physical aspects of the fulfillment process, such as stowing, picking, and packing. Technicians keep the automated systems and robotics running smoothly, ensuring minimal downtime and maximum efficiency.
Training and Safety Measures for ALB1 Employees
Amazon places great emphasis on the training and safety of its employees, and ALB1 is no exception. New hires undergo comprehensive training programs that equip them with the necessary skills and knowledge to perform their roles effectively.
Furthermore, safety measures are rigorously enforced at ALB1. Employees receive training on proper handling of equipment, lifting techniques, and hazard recognition. Advanced safety systems are in place to protect the wellbeing of every individual within the facility.
The Impact of ALB1 on Amazon’s Overall Performance
ALB1, like other fulfillment centers, plays a crucial role in shaping Amazon’s overall performance and customer experience.
How ALB1 Contributes to Amazon’s Delivery Speed
With the strategic placement of ALB1 and other fulfillment centers, Amazon is able to store products closer to customers, reducing transit times significantly. This proximity enables Amazon to offer fast and reliable delivery services, meeting and often exceeding customer expectations.
ALB1’s location allows Amazon to utilize various shipping carriers efficiently, ensuring that the right carrier is chosen for each customer order. This further enhances the delivery speed and reliability of Amazon’s services.
The Role of ALB1 in Amazon’s Sustainability Efforts
Amazon is committed to sustainability, and ALB1 plays a part in this effort. By streamlining operations and optimizing transportation routes, Amazon reduces carbon emissions associated with the delivery process.
Additionally, ALB1 and other fulfillment centers are designed with energy efficiency in mind. From the use of LED lighting to the implementation of energy management systems, Amazon ensures that its facilities operate in an environmentally responsible manner.
In conclusion, the ALB1 Amazon Fulfillment Center is a testament to Amazon’s commitment to excellence in customer service and efficiency in operations. Through advanced automation, robotics, and cutting-edge technology, ALB1 serves as a cornerstone in Amazon’s extensive supply chain, offering fast and reliable order fulfillment while contributing to the company’s overall performance and sustainability efforts.
Enhance Your Amazon Operations with AI
As you’ve seen with the ALB1 Amazon Fulfillment Center, leveraging advanced technology is key to staying ahead in the competitive world of e-commerce. Your eCom Agent brings this technological edge directly to Amazon Sellers. Imagine harnessing the power of AI to refine your product offerings, analyze customer feedback, and optimize your product detail pages with unprecedented speed and accuracy. Don’t let manual processes slow you down. Subscribe to Your eCom Agent’s AI Tools today and transform your Amazon business with the efficiency of AI.