Labeling your products correctly is a crucial step in the Amazon FBA (Fulfillment by Amazon) process. Proper labeling not only ensures smooth handling and shipping of your products but also helps you comply with Amazon’s requirements. In this step-by-step guide, we will walk you through the entire process of labeling your Amazon FBA products, from understanding the labeling requirements to troubleshooting common labeling issues. So let’s dive in!
Understanding Amazon FBA Labeling Requirements
Before we get started, it’s important to familiarize yourself with Amazon’s FBA labeling requirements. These requirements exist to ensure that your products are easily identified and tracked throughout the fulfillment process. By adhering to these guidelines, you can avoid potential delays or issues with your shipments.
Before we begin: Every Amazon Seller needs a suite of tools for Keyword Research, Product Development, and Listing Optimization. Our top pick is Helium 10 and readers of this post can get 20% off their first 6 months by clicking the image below.
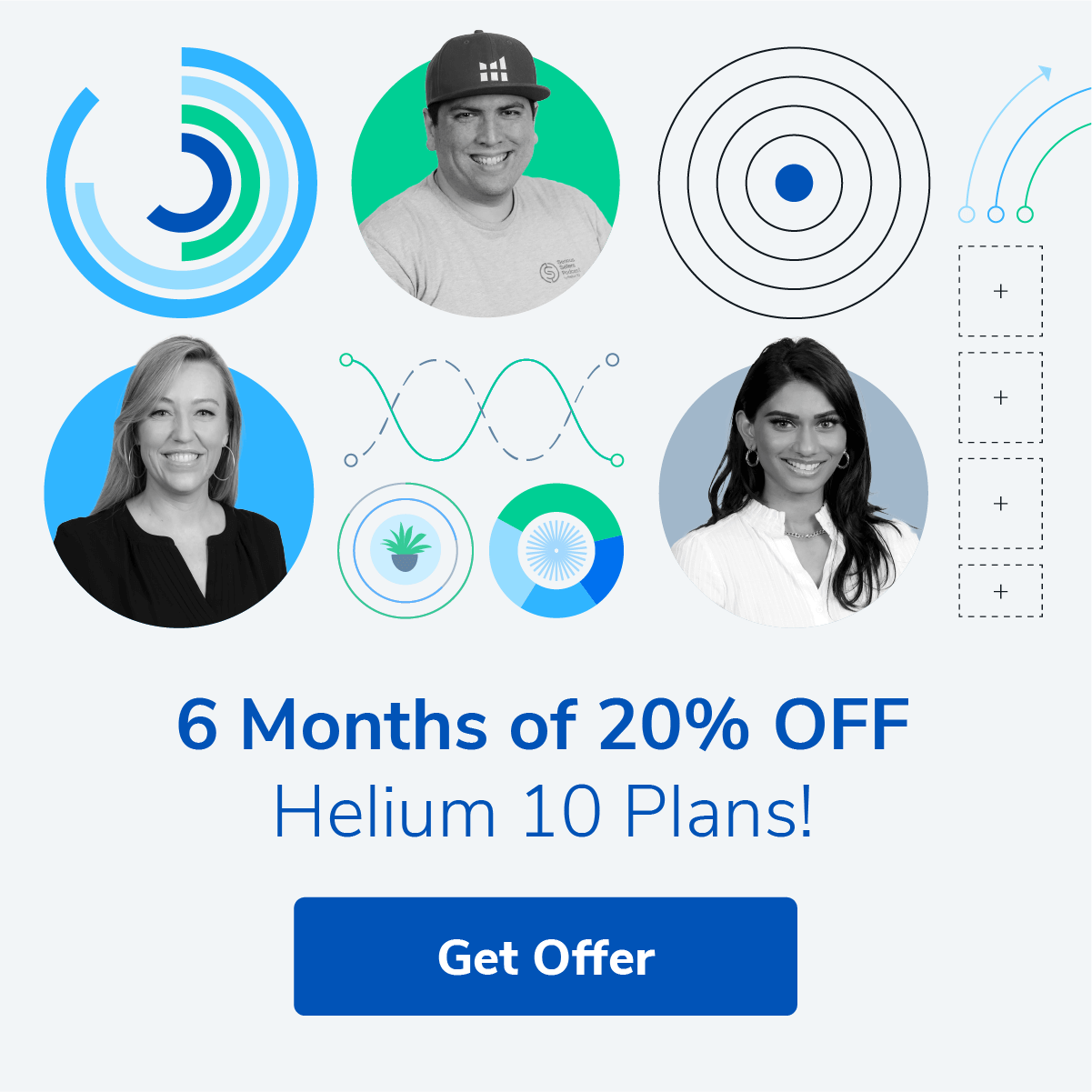
When it comes to Amazon FBA labeling, there are a few key elements to consider. First and foremost, you need to understand the importance of correct labeling. Proper labeling is essential for a smooth and efficient fulfillment process. When your products are correctly labeled, Amazon can easily identify, receive, and store them in their fulfillment centers. This helps minimize errors and ensures that your inventory is accurately tracked.
Now, let’s dive deeper into the importance of correct labeling. Imagine this scenario: you have just sent a shipment of your products to Amazon’s fulfillment center. However, due to incorrect labeling, the products are not easily identifiable. As a result, Amazon’s receiving team has trouble locating and processing your inventory. This can lead to delays in making your products available for sale, which can ultimately impact your sales and customer satisfaction.
On the other hand, when your products are properly labeled, the receiving process becomes much smoother. Amazon’s fulfillment center staff can quickly scan the labels and match them to the corresponding products in their system. This ensures that your inventory is accurately received and stored, ready to be shipped out to customers in a timely manner.
Common Mistakes to Avoid
To prevent any complications, it’s important to be aware of common labeling mistakes and avoid them. One common mistake is failing to use the correct label format. Amazon has specific requirements for label size, font type, and barcode placement. Failing to comply with these guidelines can lead to confusion and delays in the receiving process. It’s crucial to carefully review Amazon’s labeling requirements and ensure that your labels meet all the necessary specifications.
Another mistake to avoid is incorrect label placement. Labels should be affixed to the product or its packaging in a visible and easily scannable location. Placing the label in an obscure or hard-to-reach spot can cause issues during the receiving and inventory management processes. It’s important to choose a location that is easily accessible and won’t be obstructed by other packaging materials.
Illegible labels are yet another common mistake that can cause problems with inventory management. If the barcode or other important information on the label is smudged, faded, or otherwise difficult to read, it can lead to errors in scanning and tracking your inventory. Make sure to use high-quality labels and printing techniques to ensure that your labels are clear and legible.
By staying vigilant and following the guidelines, you can avoid these common labeling pitfalls. Take the time to familiarize yourself with Amazon’s FBA labeling requirements and double-check your labels before sending out your products. This attention to detail will help ensure a smooth and efficient fulfillment process, allowing you to focus on growing your business and satisfying your customers.
Preparing Your Products for Labeling
Before you begin the labeling process, it’s crucial to gather the necessary supplies and organize your inventory. Adequate preparation will ensure a smooth labeling experience.
Labeling your products is an essential step in presenting them to the market. It not only provides important information to consumers but also helps establish your brand identity. To make the most out of this process, it is important to pay attention to the details and ensure that your labels are accurate, visually appealing, and well-organized.
Gathering Necessary Supplies
To label your products, you’ll need the following supplies: a printer, suitable label paper or labels, and a good pair of scissors or a label applicator. These supplies are readily available in office supply stores or online retailers specializing in labeling materials. It’s important to choose label paper or labels that are compatible with your printer to ensure high-quality printing and adherence to your products.
When selecting a printer, consider the type of labels you will be using. Inkjet printers are suitable for most label papers, while thermal printers are commonly used for barcode labels. Additionally, having a good pair of scissors or a label applicator will make the labeling process more efficient and precise.
Organizing Your Inventory
Prior to labeling, it’s important to organize your inventory. Keep your products easily accessible and ensure that you have clear identification of each item. This organization will expedite the labeling process and help prevent any mix-ups along the way.
Start by categorizing your products based on their type, size, or any other relevant criteria. This will allow you to easily locate the items you need to label and ensure that each product receives the correct label. Consider using storage containers, shelves, or any other organizational tools that suit your needs.
Furthermore, it’s beneficial to create a labeling system that corresponds to your inventory organization. This can include using unique product codes, serial numbers, or barcodes that can be easily scanned during the labeling process. By implementing a consistent labeling system, you can streamline your inventory management and improve overall efficiency.
Another important aspect of organizing your inventory is conducting regular stock checks. This involves verifying the quantity and condition of your products to ensure accurate labeling. By keeping track of your inventory, you can avoid labeling errors and prevent any discrepancies between your records and the actual stock.
Remember, a well-organized inventory not only facilitates the labeling process but also helps with other aspects of your business, such as order fulfillment and customer service. It allows you to quickly locate products, respond to customer inquiries, and maintain accurate stock levels.
The Labeling Process Explained
Now that you’re ready to start labeling, let’s walk through the step-by-step process.
Labeling your products is an essential step in the selling process, as it ensures that your items are properly identified and tracked. This is particularly important when selling on platforms like Amazon, where efficient labeling is crucial for smooth inventory management and order fulfillment.
Creating Your Labels
The first step is to create your labels. Amazon provides the option to generate labels through their Seller Central platform, making it convenient and hassle-free for sellers. This feature allows you to select the products you wish to label, and Amazon will generate the necessary labels for you.
When generating labels, it is important to ensure that you have accurate and up-to-date product information. This includes details such as product names, SKUs, barcodes, and any other relevant identifiers. Double-checking this information will help prevent any labeling errors and ensure that your products are correctly identified.
Once you have generated the labels, it is crucial to print them on appropriate label paper or labels that meet Amazon’s requirements. Using the recommended label paper will ensure that the labels adhere properly to your products and remain intact throughout the shipping and handling process.
Applying Labels to Your Products
Once you have your labels printed, it’s time to apply them to your products. This step requires careful attention to detail to ensure accurate placement and readability of the labels.
Start by selecting a clean and flat surface on your product where the label can be easily affixed. It is important to choose a location that is visible and easily scannable by the barcode scanners used at Amazon’s fulfillment centers. This will help expedite the receiving process and minimize any potential delays in inventory processing.
When applying the labels, make sure to handle them with care to avoid any damage or smudging. Gently peel off the backing of the label and align it with the chosen location on your product. Press down firmly to ensure proper adhesion, taking care to smooth out any air bubbles or wrinkles that may occur during the application process.
Proper placement of the labels is crucial for efficient inventory management. It allows Amazon’s systems to accurately track and identify your products, ensuring that they are readily available for purchase and shipment.
By following these steps and paying attention to detail, you can ensure that your labeling process is seamless and effective. This will not only enhance your selling experience but also contribute to a positive customer experience, as accurately labeled products lead to faster and more efficient order fulfillment.
Tips for Efficient and Effective Labeling
To make your labeling process more efficient and effective, consider the following tips:
Streamlining Your Labeling Process
Look for ways to streamline your labeling process. This may include dedicating a specific area for labeling, organizing your products efficiently, or using label applicators to expedite the process. By optimizing your workflow, you can save time and effort.
Ensuring Label Durability and Visibility
Using high-quality label paper or labels will ensure that your labels remain intact throughout the fulfillment process. Additionally, verify that the labels are clearly visible and scannable to avoid any issues with inventory tracking.
Troubleshooting Common Labeling Issues
Despite your best efforts, you may encounter common labeling issues. Here are a few tips to address them:
Dealing with Labeling Errors
If you make a labeling error, don’t panic. Simply remove the incorrect label, print a new one, and carefully apply it to the correct product. It’s important to promptly rectify any labeling mistakes to ensure smooth processing.
Addressing Label Damage or Loss
In rare cases, labels may become damaged or lost during the fulfillment process. If this occurs, it’s crucial to take immediate action. Contact Amazon’s support to report the issue and request a replacement label. Prompt communication will help resolve the problem efficiently.
Labeling your Amazon FBA products correctly is a fundamental aspect of the fulfillment process. By understanding the requirements, adequately preparing your inventory, and following the step-by-step process, you can ensure a smooth and hassle-free experience. Remember to stay organized, double-check your labels, and promptly address any issues that may arise. With these guidelines in mind, you’ll be well on your way to successfully labeling your Amazon FBA products!
Enhance Your Amazon FBA Experience with AI
Ready to take your Amazon FBA business to the next level? Subscribe to Your eCom Agent’s AI Tools today and harness the power of artificial intelligence to optimize your product development, analyze customer feedback, and improve your detail pages with unparalleled efficiency. Say goodbye to the tedious hours of manual work and embrace the future of e-commerce with Your eCom Agent. Start now and watch your Amazon business thrive!