Amazon Fulfillment Centers (FCs) are known for their highly efficient processing system. These state-of-the-art facilities have revolutionized the way orders are handled, ensuring quick and accurate deliveries to customers around the world. In this article, we will explore the key components that make Amazon FCs so efficient and how they have transformed the customer experience.
Understanding Amazon FC’s Processing System
At the heart of Amazon FC’s efficiency lies its advanced processing system, which leverages cutting-edge technology and innovative strategies to maximize productivity. This not only enables Amazon to process a massive volume of orders each day but also ensures that customer satisfaction remains a top priority.
Before we begin: Every Amazon Seller needs a suite of tools for Keyword Research, Product Development, and Listing Optimization. Our top pick is Helium 10 and readers of this post can get 20% off their first 6 months by clicking the image below.
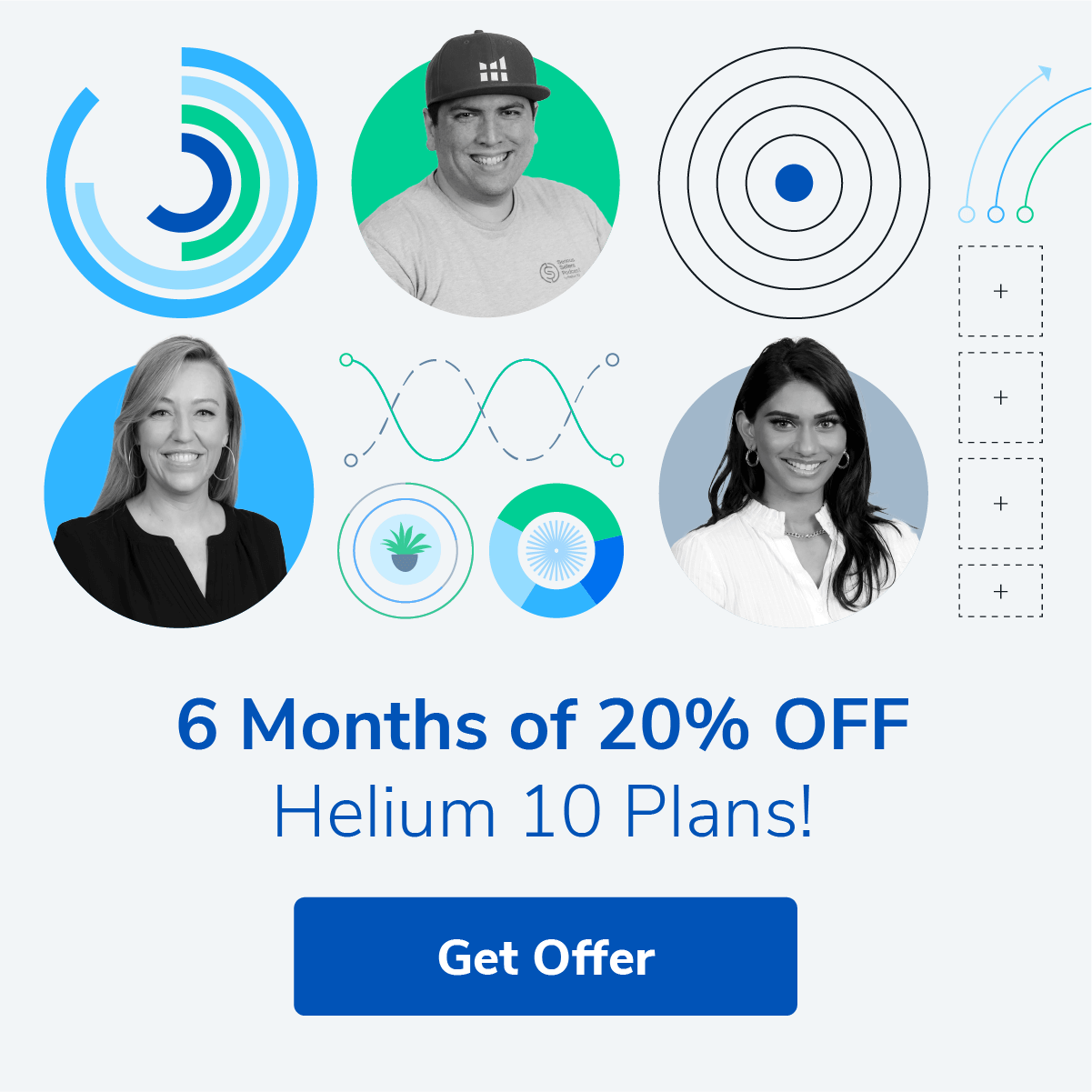
Amazon FC’s processing system is a well-oiled machine, carefully designed to handle the complexities of modern e-commerce. Let’s take a closer look at the various aspects that contribute to its success.
The Role of Technology in Amazon FC’s Efficiency
Technology plays a crucial role in Amazon FC’s processing system. From the moment an order is placed to its fulfillment and shipping, advanced algorithms and automation are utilized to streamline operations and minimize human error.
One of the key technological advancements employed by Amazon FC is robotics. These automated machines work tirelessly in the fulfillment centers, efficiently moving products from one location to another. They navigate through the aisles with precision, ensuring that the right items are picked and packed for each order.
Artificial intelligence (AI) is another vital component of Amazon FC’s processing system. AI algorithms analyze customer data, historical trends, and inventory levels to predict demand accurately. This enables Amazon to optimize its inventory management, ensuring that popular items are always in stock and ready for immediate shipment.
Machine learning algorithms are also employed to continuously improve the efficiency of Amazon FC’s processing system. These algorithms learn from past data and make adjustments to optimize the flow of products, reducing bottlenecks and minimizing the time taken to process orders.
The Structure of Amazon FC’s Processing System
Amazon FC’s processing system is meticulously organized to ensure efficiency at every step. The facility is divided into different sections, each dedicated to specific tasks such as receiving, storage, picking, packing, and shipping.
When an order is placed, it goes through a series of well-defined steps. First, the products are received at the fulfillment center, where they are carefully inspected for quality and accuracy. Once approved, the items are sorted and stored in designated areas based on their size, weight, and popularity.
When it’s time to fulfill an order, the picking process begins. Amazon FC utilizes advanced algorithms to determine the most efficient route for the pickers, ensuring that they can quickly locate the required items. This optimization reduces the time taken to assemble orders and increases overall productivity.
After the picking process, the items are sent to the packing area. Here, they are carefully packaged to ensure safe transportation. Amazon FC employs various packaging techniques, including automated systems that select the appropriate box size for each order, minimizing waste and reducing shipping costs.
Once the orders are packed, they are swiftly moved to the shipping area. Amazon FC has established partnerships with major shipping carriers to ensure fast and reliable delivery to customers’ doorsteps. The shipping process is closely monitored, and tracking information is provided to customers, allowing them to stay updated on the status of their orders.
In conclusion, Amazon FC’s processing system is a testament to the power of technology and efficient organization. By leveraging cutting-edge technology, such as robotics, artificial intelligence, and machine learning, Amazon FC is able to process a massive volume of orders with remarkable speed and accuracy. The meticulous structure of the processing system ensures that each step is optimized for maximum efficiency, resulting in satisfied customers and a thriving e-commerce giant.
Key Components of Amazon’s Fulfillment Centers
Amazon FCs incorporate several key components that contribute to their overall efficiency. These components are designed to optimize inventory management, packaging, shipping, and the overall customer experience.
Inventory Management in Amazon FC
Effective inventory management is essential for an efficient processing system. Amazon FCs utilize advanced inventory tracking systems that enable real-time visibility of stock levels. This minimizes the chances of stockouts and ensures that popular items are readily available for quick fulfillment.
Within the Amazon FCs, there are designated areas for different categories of products. These areas are strategically organized to maximize efficiency and reduce the time taken to locate and retrieve items. The inventory management system is integrated with the fulfillment process, allowing for seamless tracking of products from the moment they arrive at the center to the moment they are shipped out to customers.
Additionally, Amazon employs sophisticated algorithms and data analytics to forecast demand and optimize inventory levels. This ensures that the right amount of stock is maintained at all times, minimizing storage costs and reducing the risk of overstocking or understocking.
Packaging and Shipping Process
Amazon puts great emphasis on packaging to ensure the safe and secure transportation of products. Highly trained employees use efficient packaging techniques, optimizing space and reducing waste. They carefully select appropriate packaging materials based on the nature of the product, ensuring that it arrives in perfect condition.
Within the fulfillment centers, there are dedicated packaging stations equipped with state-of-the-art equipment. These stations are designed to streamline the packaging process, with employees having access to various tools and materials to efficiently pack items. The packaging stations are ergonomically designed to minimize strain and maximize productivity.
Once the items are packaged, they go through a rigorous quality control process to ensure that they meet Amazon’s high standards. This includes checking for any damages, verifying the accuracy of the order, and ensuring that all necessary documentation is included.
Amazon has established strong partnerships with shipping companies worldwide. These partnerships enable swift and reliable deliveries to customers’ doorsteps. The fulfillment centers have designated areas where packages are sorted based on their destination, ensuring efficient routing and minimizing delivery times.
Furthermore, Amazon utilizes advanced tracking systems that allow customers to monitor the progress of their shipments in real-time. This provides transparency and peace of mind, as customers can easily track their packages from the moment they leave the fulfillment center until they reach their doorstep.
In conclusion, Amazon’s fulfillment centers are equipped with advanced inventory management systems and efficient packaging and shipping processes. These components work together to ensure that products are readily available, properly packaged, and swiftly delivered to customers, enhancing the overall customer experience.
The Human Element in Amazon FC’s Efficiency
While technology plays a significant role, the human element is equally important in Amazon FC’s efficient processing system. The dedication and expertise of the employees contribute to the smooth functioning of the facility.
Employee Roles and Responsibilities
Each employee in Amazon FC plays a vital role in the processing system. From receiving and verifying incoming shipments to picking and packing orders, every task is assigned to specialized employees who undergo extensive training to ensure they perform their duties efficiently.
Training and Skill Development
Amazon invests heavily in training and skill development programs for its employees. This ensures that they have the necessary knowledge to operate the advanced technology and perform their tasks with precision. Regular workshops and upskilling initiatives keep the employees updated with the latest processes and tools.
The Impact of Amazon FC’s Efficiency on Customer Experience
The efficiency of Amazon FC’s processing system directly influences the customer experience. By focusing on speed, accuracy, and overall satisfaction, Amazon has set new standards in online shopping.
Speed of Delivery and Customer Satisfaction
With its efficient processing system, Amazon is able to offer fast and reliable delivery options to customers. This not only meets but often exceeds customer expectations, resulting in high levels of satisfaction and loyalty.
How Efficiency Reduces Errors in Order Fulfillment
Efficiency in Amazon FC’s processing system significantly reduces the chances of errors in order fulfillment. The advanced technology ensures that the correct items are picked, packed, and shipped, minimizing the risk of incorrect shipments or missing products. This leads to a higher rate of accuracy and customer satisfaction.
Future Developments in Amazon FC’s Processing System
Amazon FCs are constantly evolving to further improve efficiency and sustainability. The company is constantly exploring new technologies and innovative strategies to make its processing system even more advanced and environmentally friendly.
Innovations in Warehouse Technology
Amazon is continuously investing in research and development to bring the latest technological advancements to its fulfillment centers. From exploring autonomous robots for enhanced inventory management to implementing advanced data analytics for improved forecasting, the future of Amazon FC’s processing system is poised to be even more efficient.
Sustainability Initiatives in Amazon FC’s Operations
As a responsible corporate entity, Amazon is committed to incorporating sustainable practices in its operations. From using eco-friendly packaging materials to implementing energy-efficient systems, Amazon FCs are focused on reducing environmental impact while maintaining top-notch efficiency.
Conclusion
In conclusion, Amazon FC’s efficient processing system is a result of the seamless integration of technology, well-organized infrastructure, and a highly skilled workforce. By continually pushing boundaries and embracing innovation, Amazon has transformed the way orders are processed and delivered, setting new benchmarks for the e-commerce industry. As the company continues to evolve and invest in the future, we can expect even greater levels of efficiency and customer satisfaction from Amazon FCs.
Enhance Your Amazon Selling Experience
As Amazon continues to set the standard in e-commerce efficiency, there’s never been a better time for sellers to optimize their own strategies. Your eCom Agent harnesses the power of AI to elevate your Amazon business, streamlining tasks like product development, review analysis, and detail page enhancement. Embrace the future of online selling and subscribe to Your eCom Agent’s AI Tools today to transform hours of work into seconds of simplicity.