Amazon Fulfillment Centers are essential to the success of Amazon’s e-commerce operations. These massive warehouses play a pivotal role in storing, packaging, and shipping products to customers all around the world. Understanding how these fulfillment centers work is crucial to comprehend the logistics behind Amazon’s efficient and speedy delivery system.
Understanding Amazon Fulfillment Centers
Amazon Fulfillment Centers are state-of-the-art facilities strategically located across the globe. They are designed to handle a vast range of goods, from electronics to household items, books to apparel. These centers are massive in size and are equipped with advanced technology and systems to ensure smooth operations.
Before we begin: Every Amazon Seller needs a suite of tools for Keyword Research, Product Development, and Listing Optimization. Our top pick is Helium 10 and readers of this post can get 20% off their first 6 months by clicking the image below.
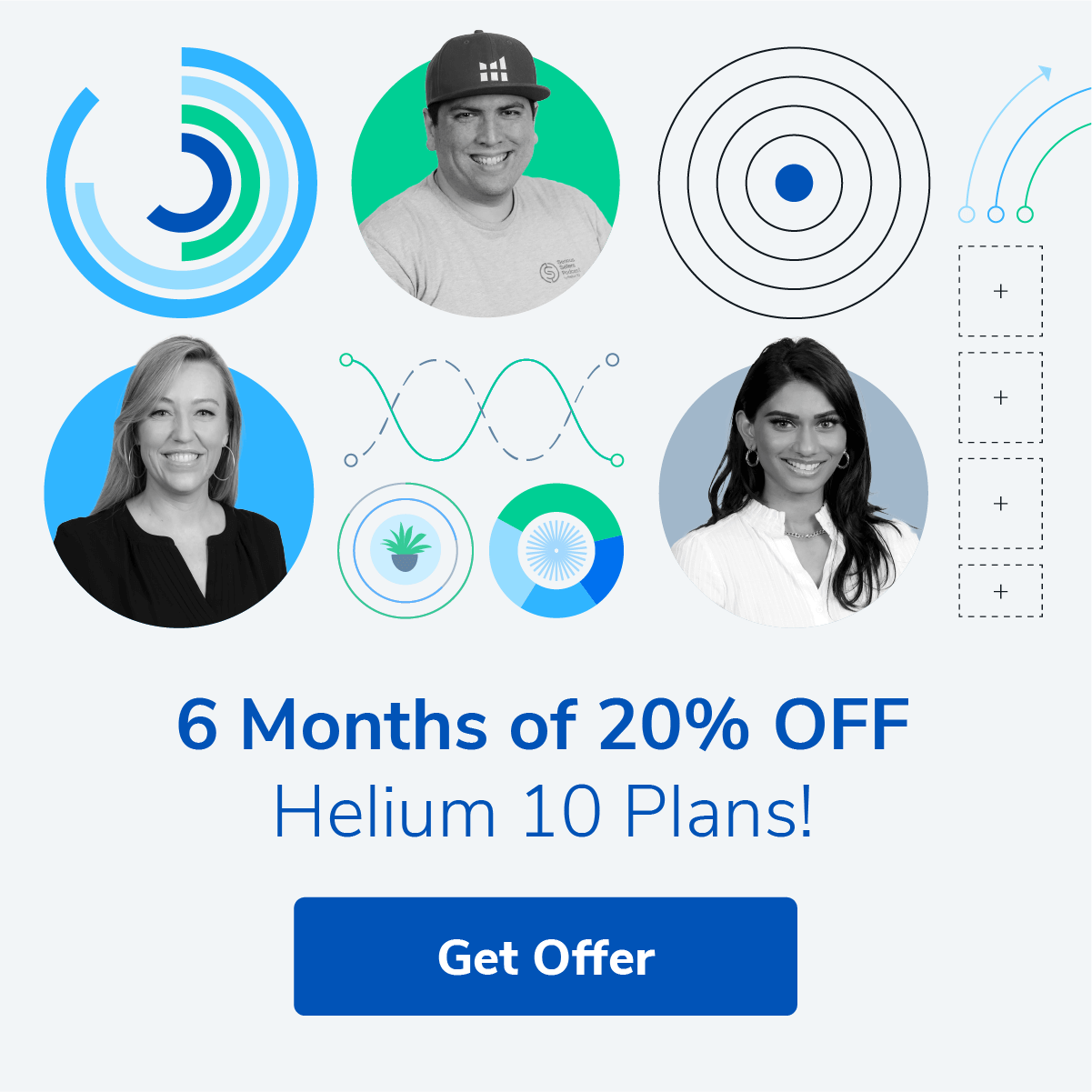
When it comes to the size of Amazon Fulfillment Centers, it’s hard to comprehend just how massive they are. Picture a warehouse that spans several football fields, with towering shelves reaching towards the ceiling. These centers are like small cities, bustling with activity as workers navigate through the aisles, picking and packing items with precision and efficiency.
The Concept Behind Amazon Fulfillment Centers
The concept of Amazon Fulfillment Centers revolves around optimizing the order fulfillment process. The aim is to streamline the movement of products from the moment an order is placed until it reaches the customer’s doorstep. This involves careful planning, organization, and utilization of resources to meet customer demands efficiently.
Imagine a well-choreographed dance, where every step is perfectly timed and executed. That’s how Amazon Fulfillment Centers operate. From the moment an order is received, it is swiftly processed and assigned to a specific area in the warehouse. Workers armed with handheld devices navigate through the maze of shelves, guided by a sophisticated inventory management system that ensures every item is accounted for.
Key Components of Amazon Fulfillment Centers
Amazon Fulfillment Centers consist of several key components that contribute to their effectiveness. These include spacious warehouses, efficient inventory management systems, advanced automation and robotics technology, and comprehensive quality control measures. Together, these components ensure that products are handled, stored, and shipped with utmost care and precision.
Walking through an Amazon Fulfillment Center feels like stepping into the future. The warehouses are meticulously organized, with products neatly arranged on shelves that seem to stretch endlessly. The inventory management systems are a marvel of technology, constantly updating in real-time to ensure accurate stock levels and efficient order processing.
But it’s not just technology that makes these centers so efficient. Amazon has invested heavily in automation and robotics technology, with machines seamlessly working alongside human workers. Automated conveyor belts transport items from one area to another, while robotic arms assist in picking and packing, reducing the risk of errors and increasing productivity.
Quality control is another crucial aspect of Amazon Fulfillment Centers. Every item that enters the center undergoes rigorous inspections to ensure it meets the highest standards. From checking for any damages to verifying the accuracy of product information, no detail is overlooked. This commitment to quality ensures that customers receive their orders in perfect condition, every time.
The Role of Technology in Amazon Fulfillment Centers
Technology plays a vital role in the operations of Amazon Fulfillment Centers. The innovative use of automation and robotics, coupled with sophisticated inventory management systems, enables Amazon to handle an extensive range of products with speed and accuracy.
With the ever-increasing demand for fast and reliable order fulfillment, Amazon has embraced cutting-edge technologies to optimize their processes. Let’s take a closer look at how automation and robotics, as well as advanced inventory management systems, have revolutionized the way Amazon Fulfillment Centers operate.
Automation and Robotics in Fulfillment Centers
Automation and robotics have revolutionized the order fulfillment process in Amazon Fulfillment Centers. These cutting-edge technologies automate tasks such as picking, packing, and sorting, reducing human error and increasing efficiency. Autonomous robots are used to transport goods within the warehouse, while automated systems handle the packaging and labeling of products.
Imagine a bustling Amazon Fulfillment Center, where robots seamlessly navigate through aisles filled with products. These robots are equipped with advanced sensors and algorithms that allow them to efficiently locate and retrieve items from shelves. They can swiftly transport these items to the packaging area, where automated systems take over to ensure precise and secure packaging.
Thanks to automation and robotics, the time required to fulfill an order has significantly decreased. This not only improves customer satisfaction but also enables Amazon to handle a higher volume of orders, even during peak seasons such as Black Friday or Cyber Monday.
Inventory Management Systems
Efficient inventory management is crucial to the smooth functioning of Amazon Fulfillment Centers. Amazon employs sophisticated inventory management systems that enable real-time tracking of products, ensuring accurate stock levels and timely replenishment. This helps prevent stockouts and delays in order fulfillment, enhancing customer satisfaction.
Behind the scenes, powerful algorithms analyze customer demand patterns, sales data, and historical trends to forecast future inventory needs. This data-driven approach allows Amazon to optimize their inventory levels, reducing the risk of overstocking or understocking. By having the right products available at the right time, Amazon can ensure prompt order fulfillment and minimize the chances of disappointing their customers.
Moreover, the integration of inventory management systems with the automation and robotics technologies mentioned earlier creates a seamless flow of information. As robots retrieve items from shelves, the inventory management system is automatically updated, providing real-time visibility into stock levels. This enables Amazon to make informed decisions regarding inventory replenishment and allocation, further enhancing operational efficiency.
In conclusion, technology has transformed Amazon Fulfillment Centers into highly efficient and reliable order fulfillment hubs. The combination of automation, robotics, and advanced inventory management systems has revolutionized the way products are picked, packed, and shipped. With these technological advancements, Amazon can meet the ever-increasing customer expectations for fast, accurate, and reliable order fulfillment.
The Process of Amazon Fulfillment
The process of order fulfillment in Amazon Fulfillment Centers involves numerous steps, meticulously designed to ensure the swift and accurate delivery of products to customers.
When a customer places an order on Amazon’s website, the journey of that order begins. The order is transmitted to the nearest fulfillment center, where a well-orchestrated process takes place to fulfill it. Let’s dive into the step-by-step guide of how Amazon handles order fulfillment.
From Order Placement to Delivery: A Step-by-Step Guide
Once an order is placed on Amazon’s website, it is transmitted to the nearest fulfillment center. This center becomes the hub for all the subsequent actions required to fulfill the order. The order is then assigned to a specific pick station, where an employee retrieves the ordered items from the vast warehouse shelves.
The pick station is a crucial part of the process, where employees use advanced technology and software systems to locate and gather the items efficiently. They meticulously pick each item, ensuring accuracy and attention to detail. This attention to detail is what sets Amazon apart, as they strive to deliver the right products to the right customers.
After the items are picked, they are sent to the packing area. Here, another group of skilled employees takes charge of preparing the items for shipping. They carefully package each item, ensuring it is protected during transit. The packaging process is designed to withstand various handling scenarios, ensuring that the products arrive in pristine condition.
Once the items are securely packed, they move on to the labeling stage. Each package is labeled with the necessary information, including the customer’s address and tracking details. This meticulous labeling ensures that the package is easily traceable throughout its journey.
With the packages labeled and ready, a shipping carrier collects them from the fulfillment center. The carrier is responsible for transporting the packages to the customer’s designated address. Amazon works with various shipping carriers to ensure efficient and timely delivery.
Throughout the entire process, Amazon employs advanced tracking systems that allow customers to monitor the progress of their orders. From the moment the order is placed to the moment it arrives at the customer’s doorstep, transparency is key.
Handling Returns and Refunds
Amazon Fulfillment Centers not only focus on order fulfillment but also handle returns and refunds. Customer satisfaction is of utmost importance, and Amazon strives to make the return and refund process as seamless as possible.
When a customer decides to return a product, the item goes through a thorough inspection at the fulfillment center. Trained employees carefully assess the condition of the returned item to determine if it can be resold. This inspection ensures that only products in suitable condition are restocked, maintaining the high quality that customers expect from Amazon.
In cases where a refund is requested, Amazon processes the refund promptly. They understand the importance of timely reimbursements and strive to provide a hassle-free experience for their customers. By streamlining the refund process, Amazon ensures that customers are promptly reimbursed for their returned items.
Amazon Fulfillment Centers are at the heart of the order fulfillment process. From the moment an order is placed to the moment it is delivered or returned, Amazon’s meticulous attention to detail ensures a smooth and efficient experience for both customers and sellers.
The Impact of Amazon Fulfillment Centers on E-commerce
Amazon Fulfillment Centers have significantly transformed the e-commerce landscape, revolutionizing the way products are ordered, processed, and delivered to customers.
Speed and Efficiency in Order Fulfillment
The streamlined operations of Amazon Fulfillment Centers have revolutionized the speed and efficiency of order fulfillment. Customers can now enjoy fast and reliable shipping options, such as Amazon Prime’s two-day delivery. This quick turnaround time has set new industry standards, raising expectations for speedy delivery across the e-commerce sector.
Customer Satisfaction and Trust
The efficient operations of Amazon Fulfillment Centers contribute to high levels of customer satisfaction and trust. The ability to consistently deliver orders accurately and on time instills confidence in customers, encouraging them to continue shopping on Amazon’s platform. This trust has played a significant role in Amazon’s dominance in the e-commerce market.
Challenges and Solutions in Amazon Fulfillment Centers
Operating Amazon Fulfillment Centers is not without its challenges, but Amazon employs innovative solutions to overcome these obstacles and ensure seamless operations.
Dealing with High Volume Orders
One of the challenges Amazon Fulfillment Centers face is managing high volume orders, particularly during peak shopping seasons, such as Black Friday or holiday seasons. To address this, Amazon hires seasonal workers and expands its fulfillment network to meet increased demand. Additionally, advanced technology and automation help handle large order volumes efficiently.
Ensuring Product Safety and Quality
Amazon places a strong emphasis on ensuring product safety and quality within its fulfillment centers. Stringent quality control measures are implemented to prevent the storage and shipment of defective or counterfeit products. Amazon also works closely with suppliers to ensure that products meet regulatory standards and customer expectations.
Overall, Amazon Fulfillment Centers play a pivotal role in Amazon’s e-commerce operations. Their efficient operations, supported by advanced technology and innovative processes, enable Amazon to provide customers with quick, reliable, and high-quality delivery services. By continually adapting and improving their fulfillment processes, Amazon continues to set the benchmark for seamless e-commerce order fulfillment.
Maximize Your Amazon Success with AI
As an Amazon Seller, understanding the intricacies of Amazon Fulfillment Centers is just the beginning. With Your eCom Agent, you can take your e-commerce business to the next level. Our suite of AI tools is designed to streamline your operations by developing better products, analyzing customer feedback, and enhancing your product detail pages with unparalleled efficiency. Don’t spend hours on tasks that our AI can accomplish in seconds. Subscribe to Your eCom Agent’s AI Tools today and transform the way you manage your Amazon store.