Amazon’s inventory reception time is a crucial aspect for sellers who want to ensure smooth operations and timely product availability. Understanding the factors that influence this process is essential for managing inventory effectively and meeting customer demand.
Understanding Amazon’s Inventory Process
When it comes to inventory management, Amazon relies heavily on its vast network of fulfillment centers. These strategically located warehouses play a vital role in receiving, storing, and shipping products. Understanding how these fulfillment centers operate is key to comprehending Amazon’s inventory reception time.
Before we begin: Every Amazon Seller needs a suite of tools for Keyword Research, Product Development, and Listing Optimization. Our top pick is Helium 10 and readers of this post can get 20% off their first 6 months by clicking the image below.
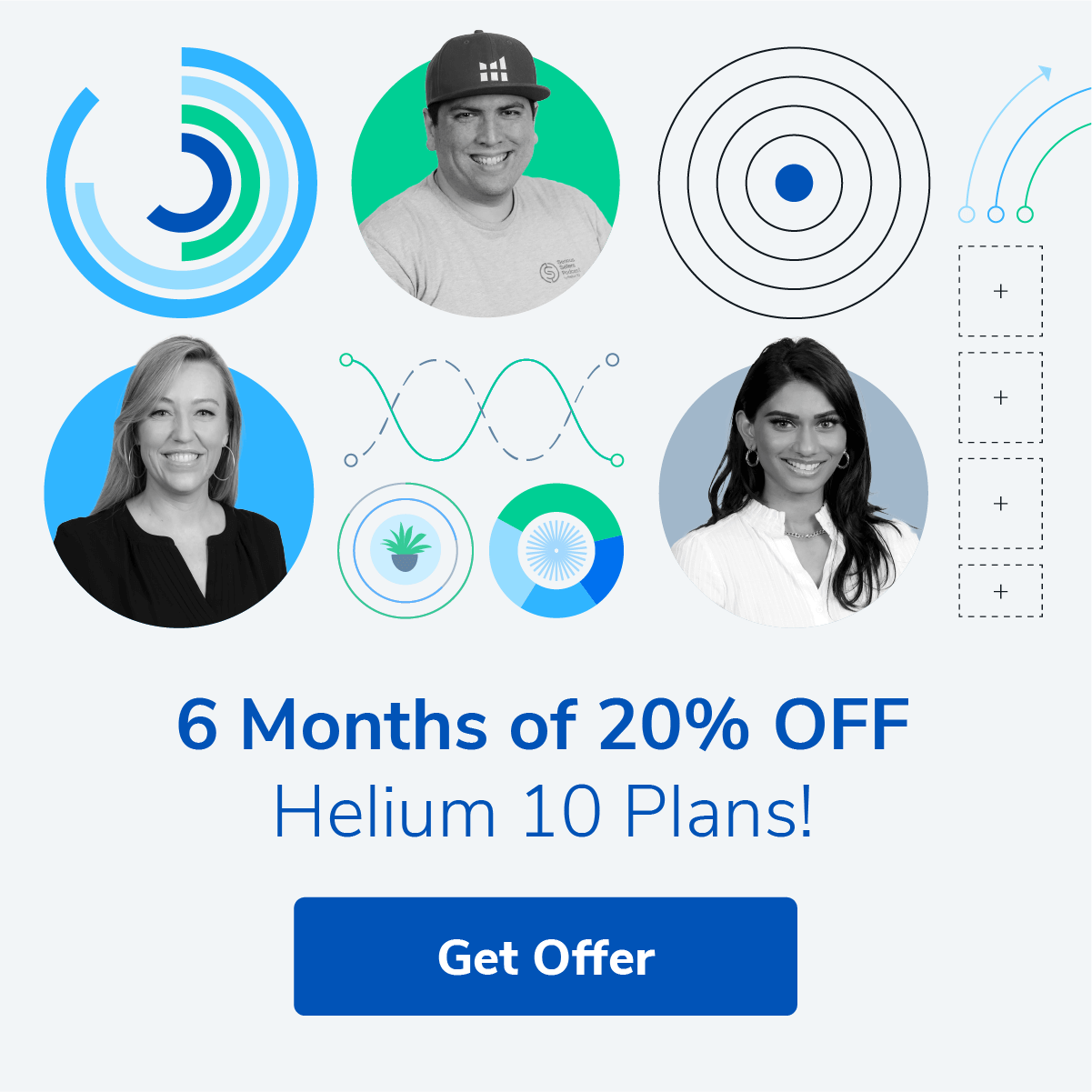
The Role of Fulfillment Centers in Inventory Management
Fulfillment centers act as storage hubs where sellers’ inventory is received and sorted. Once the products arrive, they are checked for quality and accuracy. The items are then appropriately labeled and organized within the fulfillment centers, ensuring efficient retrieval when an order is placed. This meticulous process helps expedite the delivery of products to customers.
Within the fulfillment centers, advanced technology and automation systems are employed to streamline the inventory management process. High-speed conveyor belts transport the products from one area to another, minimizing human error and maximizing efficiency. Additionally, state-of-the-art barcode scanners and tracking systems are utilized to keep a close eye on the inventory levels, ensuring accurate stock counts and timely replenishment.
Furthermore, the fulfillment centers are designed with optimized layouts to facilitate smooth operations. Different areas are designated for specific tasks, such as receiving, storage, and packing. This division of labor allows for a systematic flow of inventory, reducing the chances of confusion or delays.
The Impact of Shipping Methods on Inventory Arrival
Choosing the right shipping method is crucial for timely inventory reception. Different shipping options come with varying delivery times, and selecting the most appropriate method can greatly speed up the process. Sellers should consider factors such as cost, reliability, and transit time when deciding on a shipping method for their products.
Amazon offers a range of shipping methods, including standard shipping, expedited shipping, and priority shipping. Standard shipping is the most cost-effective option, but it may take longer for the inventory to arrive at the fulfillment centers. Expedited shipping, on the other hand, guarantees faster delivery, but it comes with a higher price tag. Priority shipping is the fastest option available, ensuring prompt inventory reception, but it is also the most expensive.
In addition to the shipping methods provided by Amazon, sellers can also choose to use their own preferred carriers. This flexibility allows sellers to leverage existing partnerships or negotiate better shipping rates, potentially reducing the time it takes for their inventory to reach the fulfillment centers.
It’s important to note that once the inventory arrives at the fulfillment centers, Amazon takes over the responsibility of storage and shipping. This allows sellers to focus on other aspects of their business, such as marketing and customer service, while Amazon handles the logistics.
In conclusion, understanding Amazon’s inventory process involves recognizing the pivotal role of fulfillment centers and the impact of shipping methods on inventory reception. By optimizing the storage and retrieval process within the fulfillment centers and selecting the most suitable shipping method, sellers can ensure timely inventory arrival and efficient order fulfillment for their customers.
Factors Influencing Amazon’s Inventory Reception Time
Several factors can influence the time it takes for Amazon to receive inventory. Being aware of these factors enables sellers to proactively manage their inventory and anticipate potential delays.
Seasonal Demand and Its Effect on Inventory Arrival
Seasonal demand fluctuations can impact inventory arrival times. During peak seasons, such as the holiday season, Amazon experiences a surge in orders. This surge in orders leads to a higher demand for inventory at Amazon’s fulfillment centers. As a result, the centers may face higher volumes of inventory, leading to longer reception times.
During the holiday season, customers are actively looking for products to purchase as gifts. This increased demand puts pressure on sellers to ensure their inventory arrives at Amazon’s fulfillment centers in a timely manner. Sellers should factor in these seasonal fluctuations and ensure they plan accordingly to meet customer demand.
Furthermore, the holiday season is not the only time when seasonal demand can affect inventory arrival. Other holidays and events, such as Black Friday or Prime Day, can also lead to increased customer demand and longer reception times. Sellers should closely monitor these events and adjust their inventory management strategies accordingly.
The Role of Supplier Location in Inventory Reception
The location of suppliers plays a crucial role in inventory reception time. If suppliers are located far from Amazon’s fulfillment centers, it can result in longer transit times. This delay in transit can be due to various factors, such as distance, transportation logistics, or customs clearance procedures.
Sellers should consider partnering with suppliers who are geographically closer to Amazon’s fulfillment centers to minimize delays in inventory reception. By doing so, sellers can reduce the time it takes for inventory to travel from the supplier to the fulfillment center, ultimately improving overall inventory reception time.
In addition to proximity, the reliability and efficiency of the transportation network between the supplier and Amazon’s fulfillment centers also play a significant role. Sellers should evaluate the transportation options available and choose suppliers who have established relationships with reliable logistics providers.
Moreover, the location of suppliers can also impact the cost of transportation. Suppliers located closer to Amazon’s fulfillment centers may offer more cost-effective shipping options, reducing overall transportation expenses for sellers.
By considering supplier location as a factor in inventory reception, sellers can strategically choose suppliers that can help optimize their inventory management and minimize delays in inventory arrival at Amazon’s fulfillment centers.
The Process of Sending Inventory to Amazon
Before sending inventory to Amazon, it is essential for sellers to follow specific procedures to ensure a smooth and efficient process. Proper preparation and utilization of Amazon’s Seller Central are crucial steps in managing inventory successfully.
Preparing Your Products for Shipment
Prior to shipping, sellers need to ensure that their products are properly prepared for transit. This includes appropriate packaging, labeling, and compliance with Amazon’s shipping guidelines. Adhering to these requirements helps prevent delays and ensures a hassle-free reception of inventory at Amazon’s fulfillment centers.
When it comes to packaging, sellers must consider the nature of their products. Fragile items, for example, require extra care and protective materials to prevent damage during transportation. This may involve using bubble wrap, foam inserts, or sturdy boxes to safeguard the products.
Labeling is another critical aspect of preparing products for shipment. Amazon requires sellers to affix unique product labels, also known as FNSKU labels, on each unit. These labels help Amazon identify and track the inventory throughout its fulfillment process. Sellers must ensure that the labels are properly placed and adhere to Amazon’s guidelines to avoid any issues.
Furthermore, compliance with Amazon’s shipping guidelines is of utmost importance. Sellers must familiarize themselves with the specific requirements, such as weight limits, packaging dimensions, and prohibited items. By adhering to these guidelines, sellers can prevent their inventory from being rejected or delayed during the shipment process.
Navigating Amazon’s Seller Central for Inventory Management
Amazon’s Seller Central provides valuable tools and resources to help sellers manage their inventory effectively. Utilizing features such as inventory reports, reorder alerts, and shipment creation helps sellers track their inventory and ensure timely replenishment. Familiarizing oneself with these tools is crucial for streamlining the inventory management process.
Inventory reports offer sellers detailed insights into their stock levels, sales performance, and product profitability. By analyzing these reports, sellers can make informed decisions about restocking, pricing, and marketing strategies. This data-driven approach enables sellers to optimize their inventory management and maximize their profitability on the Amazon platform.
Reorder alerts are another valuable feature provided by Amazon’s Seller Central. These alerts notify sellers when their inventory is running low, prompting them to take action and restock in a timely manner. By staying on top of reorder alerts, sellers can avoid stockouts and ensure a continuous supply of products to meet customer demand.
Creating shipments through Seller Central is a straightforward process that allows sellers to efficiently organize and send their inventory to Amazon’s fulfillment centers. Sellers can generate shipping plans, print shipping labels, and track the progress of their shipments all within the Seller Central interface. This centralized system simplifies the logistics of sending inventory to Amazon, saving sellers time and effort.
In conclusion, the process of sending inventory to Amazon involves careful preparation and effective utilization of Seller Central’s tools and resources. By following the proper procedures, sellers can ensure a smooth and efficient process, leading to successful inventory management on the Amazon platform.
How to Track Your Inventory Shipment to Amazon
Once inventory is shipped, it is essential for sellers to track its progress to ensure timely arrival at Amazon’s fulfillment centers. Fortunately, Amazon offers tracking features to help sellers stay informed throughout the process.
Utilizing Amazon’s Shipment Tracking Features
Amazon provides shipment tracking numbers for sellers to monitor the movement of their inventory. By entering the tracking number into the appropriate Amazon tool, sellers can view real-time updates on the status and location of their shipment. This visibility helps sellers plan and manage their inventory effectively.
Understanding Shipment Status Updates
Throughout the shipment process, Amazon provides status updates regarding the inventory’s arrival and processing. These updates can give sellers insights into any potential delays or issues that may arise during the transit. Staying informed about these status updates helps sellers take appropriate action and resolve any challenges that may impact inventory reception time.
Troubleshooting Delays in Amazon Inventory Reception
Despite careful planning and preparation, delays in inventory reception can still occur. Understanding common reasons for these delays and knowing the steps to take can assist sellers in resolving issues promptly and minimizing any negative impacts.
Common Reasons for Inventory Reception Delays
Inventory reception delays can occur due to various reasons such as transportation issues, customs clearance complications, or even internal logistics challenges. By being aware of these common factors, sellers can proactively address and resolve them, reducing the overall impact on inventory reception time.
Steps to Take When Your Inventory is Delayed
If sellers encounter delays in inventory reception, it is essential to take prompt action. Communicating with Amazon’s support team, investigating the root cause of the delay, and implementing corrective measures are crucial steps to minimize the impact on customer satisfaction. Timely resolution and proactive measures can help sellers navigate through these challenges and maintain a smooth inventory reception process in the future.
In conclusion, Amazon’s inventory reception time is influenced by various factors such as fulfillment center operations, shipping methods, supplier locations, and seasonal demand. Effectively managing inventory and tracking shipments to Amazon’s fulfillment centers are crucial steps in ensuring timely inventory availability. By understanding the process and troubleshooting any potential delays, sellers can maintain a seamless and efficient inventory reception system on Amazon’s platform.
Streamline Your Amazon Inventory Management with AI
Maximize your Amazon selling potential by subscribing to Your eCom Agent’s AI Tools. Our advanced suite of AI tools is designed to revolutionize how you manage your inventory, analyze customer feedback, and optimize your product listings. With the power of artificial intelligence, tasks that once took hours can now be accomplished in mere seconds. Don’t let inventory reception delays hinder your business growth. Subscribe to Your eCom Agent’s AI Tools today and transform your Amazon selling experience.