Amazon is renowned for its vast and efficient warehouse operations, which play a crucial role in the management of its diverse inventory. The seamless handling of goods within these warehouses forms the foundation of Amazon’s success. However, just like any other warehouse, Amazon’s operations are not immune to the challenges of damaged inventory, which can have significant financial and reputational consequences.
Understanding Amazon’s Warehouse Operations
The Role of Amazon’s Warehouse in Inventory Management
Amazon’s warehouse is not merely a storage facility; it serves as a strategic hub for managing inventory. This includes receiving, organizing, storing, and fulfilling customer orders to ensure the continuous flow of products. The efficiency of these processes directly impacts the availability of products and customer satisfaction.
Before we begin: Every Amazon Seller needs a suite of tools for Keyword Research, Product Development, and Listing Optimization. Our top pick is Helium 10 and readers of this post can get 20% off their first 6 months by clicking the image below.
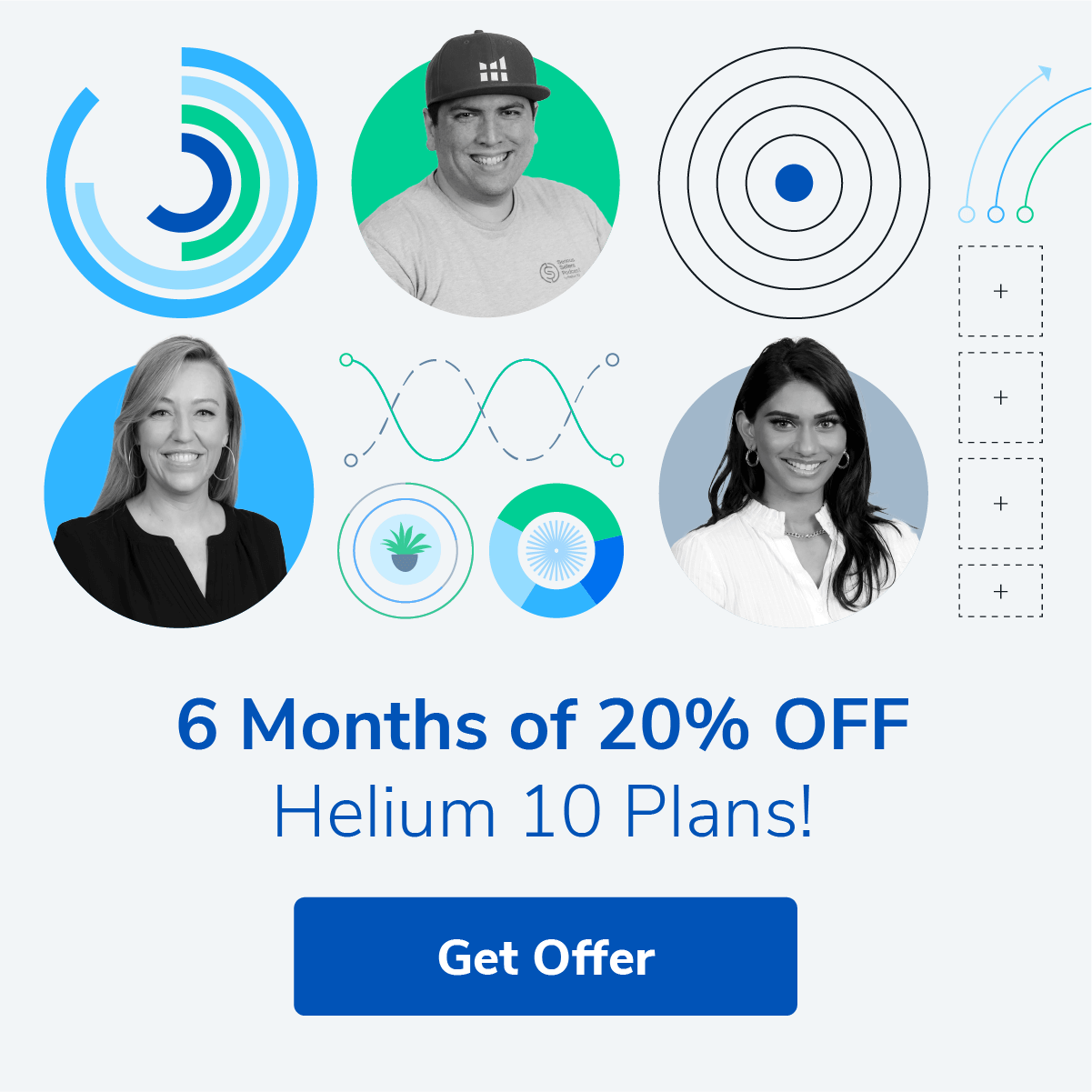
When it comes to receiving inventory, Amazon’s warehouse follows a well-defined process. As soon as the products arrive, they undergo a meticulous inspection for quality control. This step is crucial to ensure that customers receive only the highest quality items. Any damaged or defective products are promptly identified and separated for appropriate action, such as returning them to the supplier or disposing of them responsibly.
Once the quality control inspection is complete, the items are accurately labeled with unique identifiers, such as barcodes or RFID tags. These labels play a vital role in tracking and managing inventory throughout the warehouse. They enable the warehouse staff to quickly locate and retrieve specific products when fulfilling customer orders, minimizing delays and ensuring efficient operations.
Amazon’s warehouse utilizes advanced inventory management systems to keep track of the vast array of products stored within its walls. These systems employ sophisticated algorithms and data analysis techniques to optimize inventory levels, anticipate demand patterns, and streamline the overall supply chain. By leveraging technology, Amazon can maintain a well-balanced inventory, avoiding stockouts while minimizing excess stock.
Once the inventory is labeled and stored in designated areas, the warehouse employs a highly efficient retrieval process. When a customer places an order, the warehouse staff receives a notification and begins the picking process. They navigate through the aisles, guided by the inventory management system, to locate the required items. This streamlined picking process ensures that products are retrieved quickly and accurately, reducing the time between order placement and shipment preparation.
The Process of Handling Goods in Amazon’s Warehouse
Amazon’s warehouse operates like a well-oiled machine, with various steps involved in the handling of goods. Upon arrival, inventory goes through a meticulous inspection for quality control. Items are then accurately labeled and appropriately stored in designated areas, utilizing advanced inventory management systems. From there, they are efficiently retrieved and prepared for shipment.
One of the key aspects of handling goods in Amazon’s warehouse is the meticulous organization of products. Each item is assigned a specific location within the warehouse, based on factors such as size, weight, and demand. This strategic organization enables efficient storage and retrieval, minimizing the time and effort required to locate and pick items.
Furthermore, Amazon’s warehouse employs state-of-the-art automation technologies to enhance the handling of goods. Automated systems, such as conveyor belts and robotic arms, assist in moving and sorting products, reducing the reliance on manual labor and increasing operational efficiency. These technologies work in harmony with the warehouse staff, creating a seamless workflow that maximizes productivity.
In addition to the physical handling of goods, Amazon’s warehouse also places great emphasis on data analysis and optimization. The warehouse management system continuously collects and analyzes data related to inventory levels, order patterns, and customer preferences. This data-driven approach enables Amazon to make informed decisions regarding inventory replenishment, product placement, and overall warehouse operations, ensuring that customer orders are fulfilled promptly and accurately.
Overall, Amazon’s warehouse operations are a complex and well-coordinated process. From the moment inventory arrives at the facility to the preparation of shipments, every step is carefully executed to ensure the smooth flow of products and the satisfaction of customers. By combining advanced technologies, meticulous organization, and data-driven decision-making, Amazon continues to set the standard for efficient warehouse operations in the e-commerce industry.
The Issue of Damaged Inventory
When it comes to the world of e-commerce, one of the biggest challenges that companies like Amazon face is the issue of damaged inventory. Despite their sophisticated operations and state-of-the-art warehouses, damaged inventory remains a persistent problem that requires constant attention and improvement.
Common Causes of Inventory Damage in Warehouses
There are several factors that contribute to the occurrence of damaged inventory in warehouses. One of the most common causes is transportation mishaps. With thousands of products being shipped out every day, it’s inevitable that some accidents will happen along the way. Whether it’s a bumpy ride on a delivery truck or a mishap during loading and unloading, these transportation incidents can result in damaged goods.
Improper handling is another significant factor that leads to inventory damage. In a bustling warehouse environment, where speed and efficiency are crucial, there is always a risk of products being mishandled. From forklift accidents to careless handling during the picking and packing process, these human errors can have costly consequences.
Storage conditions also play a role in inventory damage. While Amazon’s warehouses are designed to optimize space and organization, there are instances where products may be stored in less than ideal conditions. Factors such as temperature fluctuations, humidity, and exposure to elements can all contribute to the deterioration of goods over time.
Furthermore, even natural disasters can wreak havoc on inventory. From floods to fires, these unforeseen events can cause significant damage to warehouses and the products stored within them.
The Cost Implications of Damaged Inventory
The financial impact of damaged inventory goes far beyond the physical loss of products. For a company like Amazon, the costs associated with damaged inventory can quickly add up. Not only do they have to bear the expense of replacing the damaged goods, but they also incur additional labor costs for rework and inspection.
Shrinkage is another cost implication that cannot be overlooked. When products are damaged, lost, or stolen, it directly affects the company’s bottom line. These losses can be particularly significant if they occur frequently or involve high-value items.
However, the financial implications are not the only concern. Reputational costs should also be taken into account. In today’s competitive e-commerce landscape, customer trust is paramount. If customers consistently receive damaged products, it can erode their confidence in the brand. This loss of trust can result in decreased customer loyalty and ultimately impact the company’s reputation.
In conclusion, the issue of damaged inventory is a complex and multifaceted challenge that companies like Amazon continuously strive to address. By identifying and mitigating the common causes of inventory damage, implementing robust quality control measures, and investing in employee training, these companies can minimize the financial and reputational costs associated with damaged inventory.
Amazon’s Approach to Inventory Damage
When it comes to inventory damage, Amazon takes a proactive approach. The company understands the importance of delivering products in pristine condition to ensure customer satisfaction. To achieve this, Amazon has established comprehensive policies and implemented various measures to address and minimize inventory damage.
Amazon’s Policies on Damaged Inventory
Amazon’s commitment to quality is evident in its policies on damaged inventory. The company conducts thorough quality checks to ensure that products meet their standards before they are shipped to customers. These checks include inspecting items for any signs of damage, verifying their functionality, and assessing their overall condition.
In addition to quality checks, Amazon has stringent requirements for its vendors. The company carefully selects vendors that meet their standards for packaging and handling. By setting clear guidelines, Amazon ensures that vendors take necessary precautions to protect the products during transit and storage.
Furthermore, Amazon provides vendors with detailed instructions on how to package and handle products properly. These instructions include using appropriate packaging materials, securing items to prevent movement, and labeling packages with fragile or sensitive contents. By providing vendors with these guidelines, Amazon aims to minimize the occurrence of damaged inventory.
Damage Control Measures in Amazon Warehouses
Amazon’s dedication to customer satisfaction extends beyond its policies. The company implements various measures in its warehouses to prevent and control inventory damage.
One of the key measures is the use of durable packaging materials. Amazon ensures that products are packaged in materials that can withstand the rigors of transportation and handling. This helps protect the items from any potential damage during transit.
In addition, Amazon employs automated systems in its warehouses to prevent mishandling. These systems use advanced technology to sort, move, and store products efficiently. By reducing the need for manual handling, the risk of accidental damage is significantly minimized.
Furthermore, Amazon provides continuous training for warehouse associates. The company emphasizes the importance of proper handling techniques and educates its employees on best practices for minimizing inventory damage. This training includes topics such as proper lifting techniques, safe storage practices, and effective use of handling equipment.
By investing in training and development, Amazon ensures that its warehouse associates are equipped with the knowledge and skills necessary to handle products with care.
In conclusion, Amazon’s approach to inventory damage is comprehensive and proactive. Through thorough quality checks, stringent vendor requirements, and clear guidelines for packaging and handling, the company aims to minimize the occurrence of damaged inventory while maintaining consistent quality for its customers. Additionally, by implementing measures such as using durable packaging materials, employing automated systems, and providing continuous training for warehouse associates, Amazon further mitigates the risks associated with damaged inventory.
The Impact of Damaged Inventory on Amazon’s Business
Financial Impact of Damaged Inventory
While damaged inventory poses financial challenges, Amazon’s robust operations and comprehensive approaches minimize the impact. However, the costs associated with damaged inventory still affect the company’s bottom line. By implementing efficient damage control strategies, Amazon can minimize these expenses and maintain its profitability.
Impact on Customer Satisfaction and Trust
Amazon’s success is built upon its reputation for exceptional customer service. Damaged inventory has the potential to undermine customer satisfaction and erode trust in the brand. Amazon recognizes this risk and works diligently to rectify any issues promptly. By prioritizing customer satisfaction, Amazon aims to preserve its reputation as a reliable and customer-centric company.
Strategies for Reducing Inventory Damage
Technological Innovations for Inventory Management
Technology plays a vital role in minimizing inventory damage. Amazon continuously invests in innovative solutions such as robotics, artificial intelligence, and real-time tracking systems. These advancements enhance accuracy, streamline operations, and reduce the likelihood of damaged inventory, ultimately benefiting both Amazon and its customers.
Training and Employee Engagement Strategies
A well-trained and engaged workforce is crucial in preventing inventory damage. Amazon embraces a proactive approach to employee development, providing comprehensive training programs that emphasize proper handling techniques, safety protocols, and quality control measures. By empowering its employees, Amazon ensures a collective commitment to reducing inventory damage.
In conclusion, while Amazon’s warehouses are a driving force behind its operational success, the occurrence of damaged inventory remains a challenge. By understanding the various facets of warehouse operations and the implications of damaged inventory, Amazon can continue implementing comprehensive strategies to mitigate risks, minimize financial consequences, and preserve its reputation for exceptional customer service. Through ongoing technological innovation and employee engagement, Amazon strives to continuously improve the efficiency of its warehouse operations and reduce the impact of damaged inventory.
Optimize Your Amazon Business with AI
As an Amazon Seller, you understand the challenges of inventory management and the importance of minimizing damaged goods. Your eCom Agent is here to revolutionize the way you handle your Amazon business. With our cutting-edge AI tools, you can now effortlessly develop better products, analyze customer feedback, and enhance your detail pages with precision and ease. Don’t let manual processes hold you back. Subscribe to Your eCom Agent’s AI Tools today and transform hours of work into seconds of simplicity, ensuring your inventory remains pristine and your customers stay satisfied.