Introduction to Amazon Inventory Adjustment Reason Codes
When it comes to managing your inventory on Amazon, you may come across various reasons for adjustments to your stock levels. These adjustments are often accompanied by reason codes, which help you understand why the change was made. In this comprehensive guide, we will dive into the world of Amazon inventory adjustment reason codes, equipping you with the knowledge you need to effectively manage your inventory.
Before we begin: Every Amazon Seller needs a suite of tools for Keyword Research, Product Development, and Listing Optimization. Our top pick is Helium 10 and readers of this post can get 20% off their first 6 months by clicking the image below.
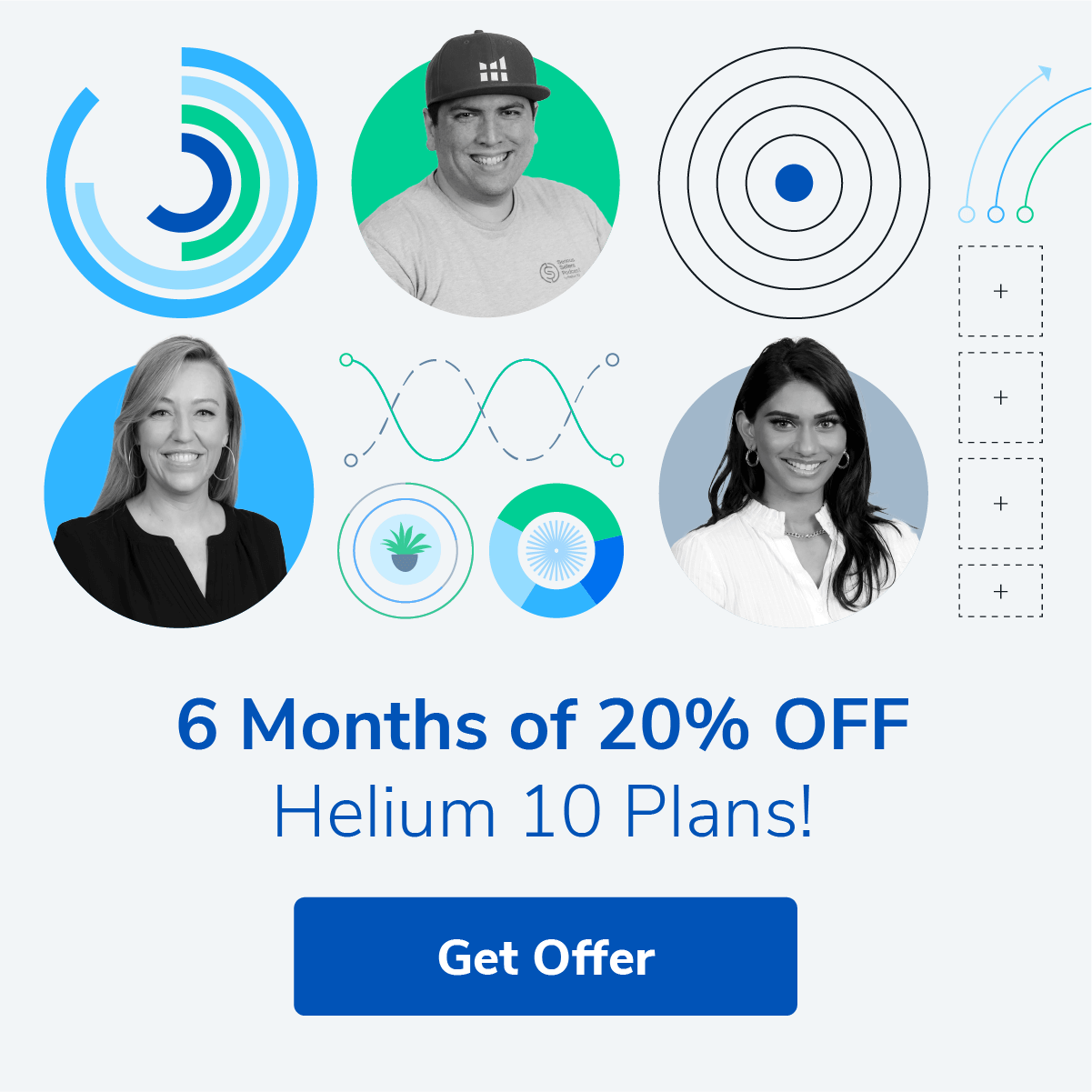
Decoding the Amazon Inventory Adjustment Reason Codes
Common Types of Adjustment Reason Codes
Amazon has a range of adjustment reason codes, each associated with a specific type of inventory change. These codes provide valuable information about the reasons behind the adjustments made to your inventory. Understanding these codes is crucial for effective inventory management. Let’s take a closer look at some common types of adjustment reason codes:
“Damage”: This reason code indicates that the inventory has been damaged and cannot be sold. It serves as an alert to potential issues in your packaging or shipping methods that may be causing damage during transit. By addressing these issues, you can minimize the risk of future damage and ensure that your products reach customers in perfect condition.
“Defect”: When you come across the “Defect” reason code, it means that the product is defective and poses a risk to customers. This code highlights the importance of quality control measures in your manufacturing or sourcing processes. By implementing rigorous quality checks, you can identify and address defects before they reach your customers, protecting your brand reputation and ensuring customer satisfaction.
“Expiration”: The “Expiration” reason code applies to products with an expired shelf life. It serves as a reminder to review your inventory turnover rate and implement processes to ensure timely restocking. By closely monitoring expiration dates and managing your inventory effectively, you can minimize the occurrence of expired products and maximize your sales potential.
“Lost”: If you encounter the “Lost” reason code, it means that the inventory has been lost and cannot be located. This code highlights the importance of accurate tracking and inventory management systems. By implementing robust tracking mechanisms, such as barcoding or RFID technology, you can minimize the occurrence of lost inventory and streamline your operations.
“Process”: The “Process” reason code signifies an internal process that requires adjustment. This code may indicate the need for process optimization or the implementation of new procedures to enhance efficiency. By analyzing the specific circumstances surrounding this code, you can identify areas for improvement and implement changes that will streamline your operations and drive productivity.
Interpreting the Codes: A Detailed Look
Interpreting the adjustment reason codes is vital for understanding the impact of the inventory changes on your business. Each reason code acts as a clue, providing valuable insights into the specific circumstances surrounding the adjustment. By carefully analyzing and interpreting these codes, you can make informed decisions about your inventory management strategies.
For example, if you frequently encounter the “Damage” reason code, it may be necessary to adjust your packaging or shipping methods to minimize the risk of damage during transit. Similarly, if the “Expiration” reason code appears frequently, you may need to review your inventory turnover rate and implement processes to ensure timely restocking. By proactively addressing the underlying issues indicated by these codes, you can optimize your inventory management practices and improve overall operational efficiency.
Impact of Inventory Adjustment Reason Codes on Your Business
Inventory management is a critical aspect of running a successful business. It involves keeping track of stock levels, ensuring accuracy, and avoiding potential issues that can disrupt operations. One key element of inventory management is understanding the impact of adjustment reason codes.
Adjustment reason codes provide valuable insights into the reasons behind inventory adjustments. By knowing the specific reasons for adjustments, businesses can take proactive measures to address underlying problems and prevent them from recurring. This proactive approach helps maintain accurate stock levels and ensures customer satisfaction.
How Adjustment Reason Codes Affect Inventory Management
When it comes to inventory management, adjustment reason codes are like signposts that guide businesses in the right direction. They provide valuable information about the nature of adjustments, such as whether they are due to defects, expiration, or other factors.
For example, let’s say a business consistently encounters the “Defect” reason code. This could indicate a problem with the quality control processes or supplier relationships. By identifying and rectifying the root cause, businesses can minimize the occurrence of defects and ensure customer satisfaction.
Similarly, adjustment reason codes can help businesses identify patterns or trends in inventory adjustments. This information can be used to optimize inventory management strategies, such as adjusting reorder quantities or implementing preventive maintenance measures.
The Role of Reason Codes in Profit Calculation
Reason codes not only impact inventory management but also play a crucial role in profit calculation. By accurately tracking and categorizing inventory adjustments based on reason codes, businesses can gain insights into the financial impact of each adjustment.
For instance, tracking adjustments due to damaged or lost inventory allows businesses to understand the costs associated with such incidents. This information helps in evaluating the effectiveness of packaging, handling, and storage practices. It also enables businesses to take appropriate measures to minimize losses and improve overall profitability.
Reason codes also provide insights into the potential revenue loss from expired products. By categorizing adjustments related to expiration, businesses can evaluate the effectiveness of their inventory rotation strategies and take necessary actions to reduce waste and maximize revenue.
With accurate data on inventory adjustments and their associated reason codes, businesses can make data-driven decisions about pricing, reordering, and replenishing their inventory. This helps optimize profitability by ensuring the right balance between supply and demand.
In conclusion, adjustment reason codes have a significant impact on inventory management and profit calculation. By understanding the reasons behind inventory adjustments and using this information to drive proactive measures, businesses can maintain accurate stock levels, minimize losses, and optimize profitability.
Best Practices for Managing Amazon Inventory Adjustment Reason Codes
Keeping Track of Your Inventory Adjustment Reason Codes
To effectively manage Amazon inventory adjustment reason codes, it is essential to keep detailed records of each adjustment. This includes recording the specific reason code, the quantity of inventory affected, and any relevant notes or comments.
For example, let’s say you have an inventory adjustment due to damaged goods. In your records, you would note the reason code as “Damaged Goods” and specify the quantity of inventory that was affected. You might also include any additional information, such as the condition of the packaging or any visible signs of damage.
By maintaining organized records, you can easily reference past adjustments and identify any recurring issues. This documentation also allows you to provide accurate information to Amazon or your suppliers when necessary.
Furthermore, keeping track of the reason codes can help you analyze patterns and trends in your inventory adjustments. For instance, if you notice a high frequency of adjustments related to incorrect product listings, you can take proactive measures to improve your listing accuracy and reduce future adjustments.
Strategies for Efficient Inventory Adjustment
Efficiently managing inventory adjustments involves implementing strategies to minimize their occurrence and streamline the adjustment process. One key strategy is to regularly conduct quality checks to identify and address any potential issues proactively.
During these quality checks, you can inspect your inventory for any signs of damage, expiration, or other issues that may require adjustment. By catching these issues early on, you can take corrective actions to prevent further inventory loss or customer dissatisfaction.
Additionally, establishing clear communication channels with suppliers and carriers can help prevent inventory loss or damage during transportation. By regularly communicating with your suppliers, you can ensure that they are packaging and handling your inventory appropriately. This can minimize the chances of adjustments due to external factors.
Moreover, maintaining a good relationship with your carriers can also contribute to efficient inventory management. By working closely with your carriers, you can address any shipping or delivery issues promptly, reducing the need for adjustments due to transportation mishaps.
In conclusion, managing Amazon inventory adjustment reason codes requires careful record-keeping and proactive strategies. By keeping detailed records, you can easily reference past adjustments and identify recurring issues. Implementing strategies such as regular quality checks and clear communication with suppliers and carriers can help minimize adjustments and streamline the adjustment process.
Troubleshooting Common Issues with Amazon Inventory Adjustment Reason Codes
Dealing with Unexplained Inventory Adjustments
Unexplained inventory adjustments can be frustrating and challenging to resolve. In such cases, it is crucial to review your internal processes and systems to identify any potential sources of error. However, if you are unable to determine the cause of the adjustments, reaching out to Amazon Seller Support for assistance can provide valuable insights and potential solutions.
Resolving Discrepancies in Inventory Adjustment Reason Codes
Discrepancies in inventory adjustment reason codes may occur when there is a miscommunication or error during the adjustment process. It is essential to carefully review the details of the adjustment and compare them to your records.
If you identify any discrepancies, you can submit a case to Amazon Seller Support, providing all relevant information and requesting a resolution. The support team will investigate the issue and work with you to rectify any errors or discrepancies.
By understanding Amazon inventory adjustment reason codes and their impact on your business, you can effectively manage your inventory, optimize profitability, and resolve any issues that arise. Implementing best practices and troubleshooting strategies will ensure smooth operations and enhance customer satisfaction. Stay proactive and attentive to adjustments, and your business will thrive in the competitive world of Amazon.
Streamline Your Amazon Inventory Management with AI
Ready to take your Amazon inventory management to the next level? Subscribe to Your eCom Agent’s AI Tools today and harness the power of artificial intelligence to enhance your product development, analyze reviews, improve your detail pages, and more. Save time and boost your efficiency with our cutting-edge AI suite designed specifically for Amazon Sellers. Don’t let inventory adjustments slow you down – let Your eCom Agent be your competitive edge!