Welcome to the Amazon Warehouse in Arlington, Texas! In this comprehensive guide, we will take you on a journey to explore the inner workings of this technological marvel. From understanding the operations to learning about the layout, workforce, environmental impact, and the future, this article will provide you with a detailed overview. So, let’s dive in!
Understanding the Amazon Warehouse Operations
At the heart of Amazon’s success is its highly efficient warehouse operations. These operations are powered by a combination of cutting-edge technology and a dedicated workforce. One of the key technologies driving these operations is robotics.
Before we begin: Every Amazon Seller needs a suite of tools for Keyword Research, Product Development, and Listing Optimization. Our top pick is Helium 10 and readers of this post can get 20% off their first 6 months by clicking the image below.
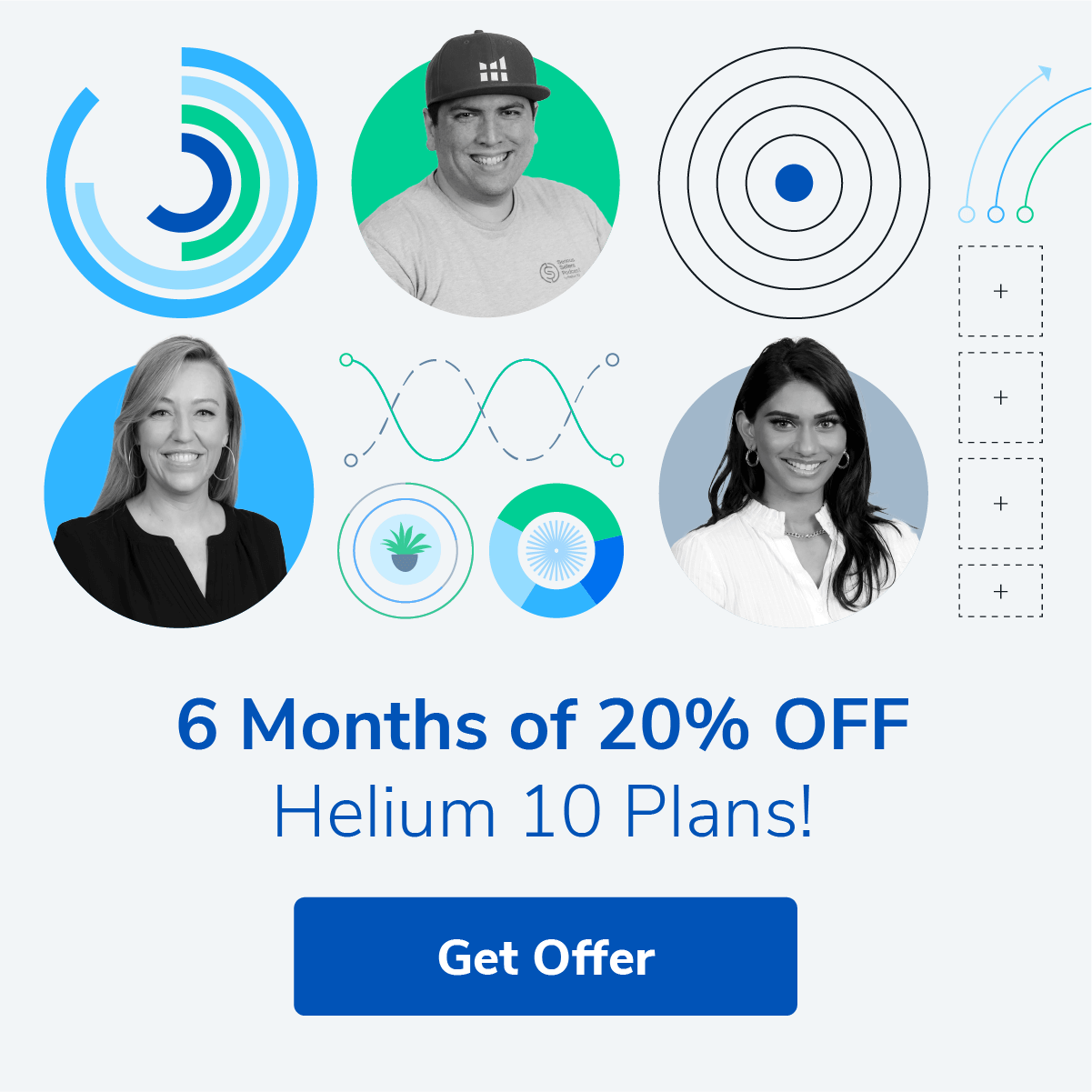
Amazon’s warehouses are a hive of activity, with robots working alongside human employees to ensure smooth operations. These robots are equipped with advanced sensors and algorithms that allow them to navigate the warehouse floor and perform a wide range of tasks.
One of the most important roles of robotics in Amazon warehouses is picking. When an order is received, robots are deployed to locate the items in the vast inventory. These robots use their sensors to identify the correct product and pick it up with precision. This automation not only speeds up the process but also reduces the risk of human error.
In addition to picking, robots also play a crucial role in packing and sorting. Once the items are picked, they are brought to a designated packing station where robots carefully package them. These robots are programmed to select the appropriate box size, insert protective materials, and seal the package securely. This automated packing process ensures that each item is packaged correctly and ready for shipment.
The Process of Order Fulfillment
Order fulfillment is an intricate process that consists of several steps. It begins with the receiving of products from manufacturers or suppliers. These products go through thorough inspection and quality checks before being sorted and organized for storage.
Once the products are received and inspected, they are assigned a specific location within the warehouse. This location is determined based on factors such as product size, popularity, and frequency of orders. By strategically organizing the inventory, Amazon can optimize the picking process and minimize the time it takes to fulfill orders.
When a customer places an order, the items are picked, packed, and shipped to ensure speedy and accurate delivery. The robots play a crucial role in this process, working in tandem with human employees to fulfill orders efficiently. They navigate the warehouse, retrieve the items, and bring them to the packing station, where they are carefully packaged and prepared for shipment.
Safety Measures in Place
Amazon prioritizes the safety of its employees and invests heavily in ensuring a safe working environment. Measures such as extensive training, ergonomic workstations, and strict adherence to safety protocols are in place to minimize accidents and injuries.
Robots in Amazon warehouses are designed with safety features to prevent collisions with humans and other objects. They are equipped with sensors that allow them to detect obstacles and adjust their path accordingly. Additionally, employees working alongside robots receive specialized training to ensure they understand how to safely interact with these machines.
Furthermore, Amazon regularly conducts safety audits and inspections to identify and address any potential hazards. This proactive approach to safety helps create a work environment where employees can perform their tasks with confidence and peace of mind.
The Layout of the Arlington, TX Warehouse
The Arlington warehouse is strategically designed to optimize efficiency and productivity. It is divided into three main areas: the receiving area, the sorting area, and the shipping area.
Located in the heart of Arlington, Texas, the warehouse spans over 100,000 square feet, making it one of the largest distribution centers in the region. With its state-of-the-art facilities and cutting-edge technology, the Arlington warehouse is able to handle a high volume of products and ensure seamless operations.
The Receiving Area
In the receiving area, products arriving from suppliers are meticulously checked, labeled, and organized. This area serves as the entry point for goods and sets the foundation for smooth operations. A team of highly trained warehouse staff carefully inspects each item, ensuring that they meet the quality standards and specifications set by the company.
The receiving area is equipped with advanced barcode scanners and inventory management systems, allowing for efficient tracking and recording of incoming products. This ensures accurate inventory control and minimizes the risk of errors or discrepancies.
The Sorting Area
Once products pass through the receiving area, they are transported to the sorting area. Here, advanced scanning systems and algorithms are utilized to categorize items based on their destination. The efficient sorting process ensures that products are readily accessible for order fulfillment.
The sorting area is divided into different sections, each dedicated to specific product categories. Highly trained warehouse personnel work diligently to organize and arrange the products, optimizing space utilization and facilitating easy retrieval. The use of automated conveyor belts and robotic arms further enhances the sorting process, allowing for swift and accurate placement of items in their respective sections.
The Shipping Area
The final step in the warehouse journey takes place in the shipping area. Here, items are carefully packed, labeled, and prepared for shipment. The use of advanced tracking systems enables customers to monitor their packages throughout the delivery process.
The shipping area is equipped with a variety of packaging materials, ranging from sturdy cardboard boxes to protective bubble wrap and cushioning materials. Warehouse staff meticulously pack each item, ensuring that they are secure and well-protected during transit. Labels with shipping information, barcodes, and tracking numbers are affixed to each package, allowing for easy identification and tracking.
Once the packages are ready for shipment, they are loaded onto delivery trucks or transported to the loading dock for pickup by shipping carriers. The warehouse has established strong partnerships with reliable logistics providers, ensuring that packages are delivered to customers in a timely and efficient manner.
In conclusion, the layout of the Arlington, TX warehouse is designed to optimize efficiency and productivity. From the receiving area to the sorting area and finally the shipping area, each step in the warehouse journey is carefully executed to ensure seamless operations and customer satisfaction.
The Workforce Behind the Warehouse
An essential component of Amazon’s warehouse operations is its dedicated and skilled workforce. Warehouse employees play various roles and have distinct responsibilities that contribute to the smooth functioning of the facility.
Let’s take a closer look at the different roles and responsibilities of these warehouse employees. One crucial role is inventory management. Warehouse employees are responsible for keeping track of the vast inventory that flows in and out of the facility. They meticulously monitor stock levels, ensuring that products are readily available for order fulfillment.
Another vital responsibility is order picking. Warehouse employees are the ones who physically locate and retrieve the items from the shelves or storage areas. They follow precise picking procedures to ensure accuracy and efficiency, ensuring that the right products are selected for each customer’s order.
Quality control is yet another critical aspect of warehouse operations. Employees are responsible for inspecting the products for any defects or damages before they are shipped out to customers. They meticulously examine each item, ensuring that only high-quality products reach the customers’ hands.
Training and Skill Development Opportunities
Amazon understands the value of investing in its employees’ growth and development. It provides ample training and skill development opportunities to help them enhance their expertise and expand their career horizons.
Warehouse employees receive comprehensive training on various aspects of their roles. They learn about inventory management systems, order picking techniques, and quality control procedures. This training equips them with the knowledge and skills necessary to perform their duties efficiently.
Furthermore, Amazon offers continuous learning programs to encourage employees to develop new skills and stay updated with the latest industry trends. These programs include workshops, seminars, and online courses that cover a wide range of topics, from leadership development to technological advancements in warehouse operations.
Employees also have access to career advancement opportunities within the company. Amazon values internal talent and actively promotes from within. Warehouse employees who demonstrate exceptional performance and dedication have the chance to move up the career ladder and take on more challenging roles, such as team leads or supervisors.
In conclusion, the workforce behind Amazon’s warehouse operations is a well-trained and skilled group of individuals. Their roles and responsibilities, from inventory management to order picking and quality control, are crucial in ensuring the smooth functioning of the facility. With Amazon’s commitment to employee growth and development, warehouse employees have ample opportunities to enhance their skills and advance their careers within the company.
Environmental Impact and Sustainability Efforts
As an organization committed to sustainability, Amazon continuously strives to reduce its environmental footprint. The Arlington warehouse is no exception to this effort.
Energy Efficiency Measures
Amazon incorporates various energy-efficient technologies and practices within its warehouses. From utilizing LED lighting to implementing smart climate-control systems, these measures help minimize energy consumption and reduce greenhouse gas emissions.
Waste Management Strategies
To minimize waste and promote recycling, Amazon has established efficient waste management strategies. Recycling programs, proper disposal of hazardous materials, and encouraging sustainable packaging are some of the initiatives undertaken to protect the environment.
The Future of Amazon Warehouses
As technology continues to advance, Amazon anticipates exciting developments in its warehouse operations. Let’s take a glimpse into the future!
Technological Advancements and Innovations
Amazon consistently invests in research and development to stay at the forefront of technological advancements. From exploring the potential of artificial intelligence to optimizing supply chain processes, innovation is key to the future success of Amazon warehouses.
Expansion Plans and New Locations
As demand for fast and reliable service grows, Amazon aims to expand its warehouse network to cater to customer needs effectively. Planning for new locations worldwide is already underway, ensuring a wider reach and faster delivery for millions of customers.
In conclusion, the Amazon Warehouse in Arlington, TX, is a fascinating amalgamation of cutting-edge technology, efficient processes, and a skilled workforce. From the role of robotics to the layout of the warehouse, sustainability efforts to the future outlook, every aspect works together seamlessly to ensure customer satisfaction and operational excellence. Now that you’ve been equipped with a comprehensive guide, explore and appreciate the marvel that is the Amazon Warehouse in Arlington, Texas!
Enhance Your Amazon Business with AI
As you marvel at the efficiency of the Amazon Warehouse in Arlington, TX, imagine the possibilities when you apply similar technological advancements to your own Amazon business. Your eCom Agent offers a suite of AI tools designed to revolutionize how you develop products, analyze customer feedback, and optimize your listings. Don’t let the competition outpace you. Subscribe to Your eCom Agent’s AI Tools today and transform hours of work into seconds of smart, data-driven strategy.