In today’s fast-paced business environment, maximizing efficiency is crucial for maintaining a competitive edge. One area where companies can significantly improve efficiency is in pallet optimization. By utilizing a pallet optimization calculator, businesses can streamline their supply chain processes, reduce costs, and enhance overall productivity. In this article, we will delve into the concept of pallet optimization, explore the mechanics of a pallet optimization calculator, discuss the benefits of using one, and provide valuable insights on implementing and measuring the success of this tool.
Understanding Pallet Optimization
Before we dive into the mechanics of a pallet optimization calculator, let’s first establish a clear understanding of what pallet optimization entails. Essentially, pallet optimization is the process of maximizing the space utilization on a pallet while adhering to specific constraints. These constraints can include weight limitations, product dimensions, and packaging requirements.
Before we begin: Every Amazon Seller needs a suite of tools for Keyword Research, Product Development, and Listing Optimization. Our top pick is Helium 10 and readers of this post can get 20% off their first 6 months by clicking the image below.
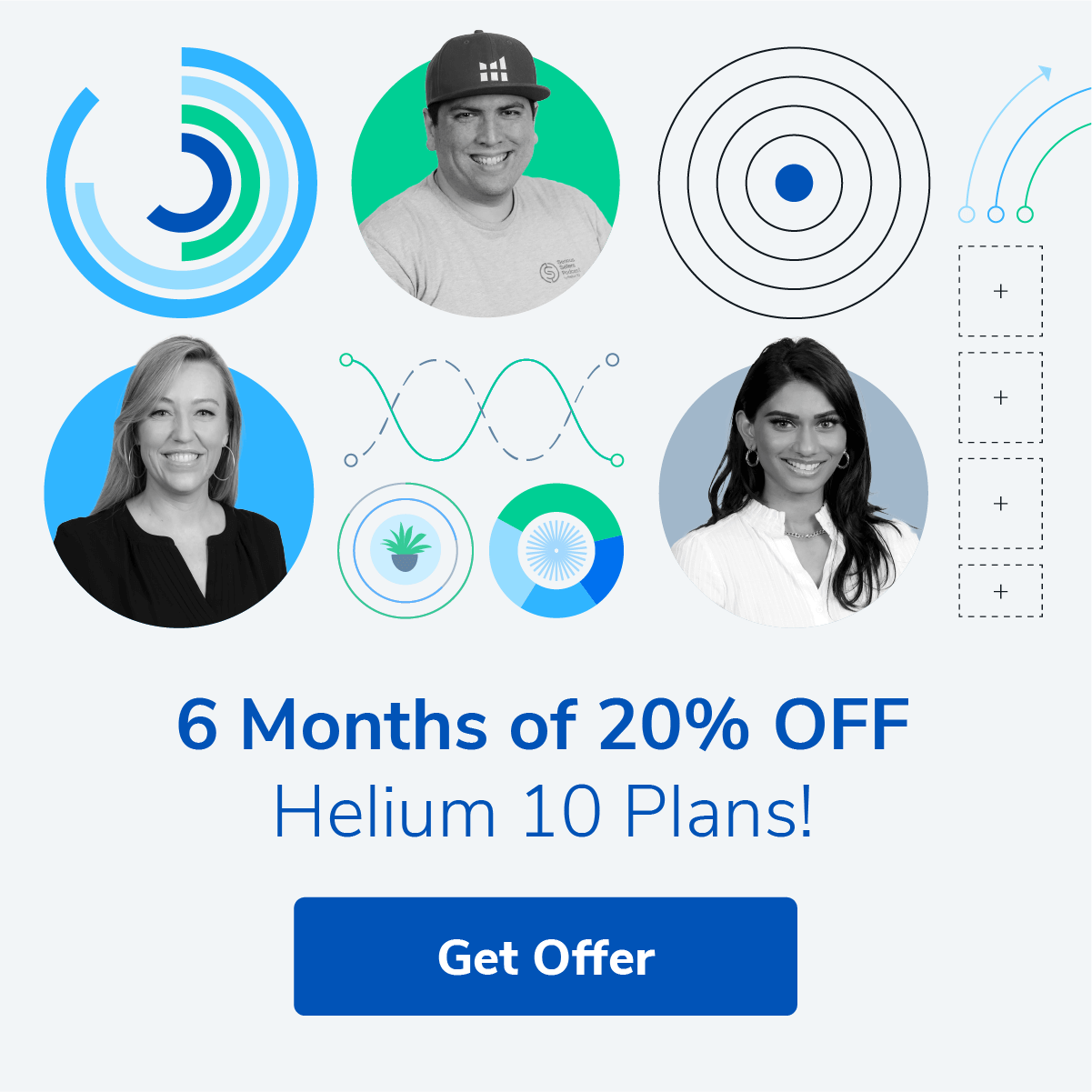
By efficiently arranging products on a pallet, businesses can minimize wasted space and maximize the number of items that can be transported in a single shipment. This not only reduces shipping costs but also enhances warehouse efficiency by maximizing storage capacity.
When it comes to pallet optimization, there are several factors to consider. One important aspect is the shape and size of the products being loaded onto the pallet. Irregularly shaped items may require special arrangements to ensure stability and prevent damage during transportation. Additionally, the weight distribution across the pallet should be carefully balanced to maintain stability and prevent any potential accidents.
The Concept of Pallet Optimization
At its core, the concept of pallet optimization revolves around finding the optimal arrangement of products on a pallet to minimize empty spaces. By strategically placing items based on their dimensions and weight, businesses can create tighter and more compact loads, thereby reducing the need for additional shipments or larger warehouse space.
Furthermore, pallet optimization can also take into account other factors such as product fragility and compatibility. Fragile items may require additional cushioning or separation to prevent breakage, while certain products may need to be kept separate due to incompatibility issues. By considering these factors, businesses can ensure that their pallets are not only optimized for space but also for the safe transportation of goods.
The Role of Pallet Optimization in Supply Chain Management
Pallet optimization plays a vital role in supply chain management by improving overall logistics efficiency. By optimizing pallet loads, businesses can reduce the number of trucks required for transportation, minimize fuel consumption, and lower carbon emissions. This not only benefits the environment but also translates into substantial cost savings for companies.
In addition to cost and environmental benefits, pallet optimization also contributes to better inventory management. By maximizing the number of items that can be loaded onto a pallet, businesses can reduce the frequency of restocking and improve order fulfillment. This leads to shorter lead times and increased customer satisfaction.
Moreover, pallet optimization can also enhance the safety of the supply chain. By ensuring that pallets are loaded and secured properly, the risk of accidents, such as items falling off during transportation, is significantly reduced. This not only protects the products being transported but also safeguards the well-being of the drivers and other road users.
In conclusion, pallet optimization is a critical aspect of efficient supply chain management. By strategically arranging products on a pallet, businesses can minimize wasted space, reduce shipping costs, and improve overall logistics efficiency. With the help of advanced pallet optimization tools and techniques, companies can achieve significant cost savings, enhance customer satisfaction, and contribute to a greener and safer supply chain.
The Mechanics of a Pallet Optimization Calculator
A pallet optimization calculator automates the process of determining the best arrangement of products on a pallet. It takes into account various factors such as product dimensions, weight, and packaging requirements to generate an optimized pallet loading plan. Let’s take a closer look at how a pallet optimization calculator works.
When it comes to pallet optimization, efficiency is key. A pallet optimization calculator utilizes advanced algorithms to analyze product data and constraints and generate an optimized loading plan. These algorithms take into consideration factors such as product dimensions, weight distribution, and stacking configurations to create the most efficient pallet loads.
Imagine a warehouse filled with products of different shapes and sizes. Without a pallet optimization calculator, determining the best arrangement of these products can be a time-consuming and labor-intensive task. However, by leveraging these advanced algorithms, businesses can quickly and accurately determine the optimal arrangement of products, saving time and manual labor.
How a Pallet Optimization Calculator Works
A pallet optimization calculator works by first gathering product data such as dimensions, weight, and packaging requirements. This information is typically stored in a comprehensive product database. Once the necessary data is collected, the calculator applies the algorithms to analyze the data and constraints.
The algorithms take into account various factors, including weight limits, stacking restrictions, and pallet dimensions, to ensure that the generated pallet configurations are optimal. By considering these constraints, the calculator can create loading plans that maximize the use of space while adhering to the specific requirements set by the business.
After analyzing the data and constraints, the pallet optimization calculator generates an optimized loading plan. This plan outlines the arrangement of products on the pallet, taking into consideration factors such as weight distribution, stability, and ease of loading and unloading. The calculator may also provide visual representations of the loading plan, allowing users to view and fine-tune the arrangement of products.
Key Features of a Pallet Optimization Calculator
A pallet optimization calculator typically offers several key features that enhance its functionality and usability. These features include:
- Product Database: A comprehensive database that stores product information such as dimensions, weight, and packaging requirements. This database allows businesses to easily access and manage product data, ensuring accurate and up-to-date information for the optimization process.
- Constraint Settings: The ability to set constraints such as weight limits, stacking restrictions, and pallet dimensions to ensure optimal pallet configurations. By adjusting these constraints, businesses can customize the optimization process to meet their specific needs and requirements.
- Visualization Tools: Interactive visual representations of pallet loading plans, allowing users to view and fine-tune the arrangement of products. These visualization tools provide a clear and intuitive way to understand the loading plan, making it easier to make adjustments and optimize the pallet configuration.
- Reporting and Analytics: Detailed reports and analytics that provide insights into efficiency gains, cost savings, and other key performance indicators. By analyzing the data and metrics provided by the calculator, businesses can identify areas for improvement and make data-driven decisions to optimize their pallet loading processes.
Overall, a pallet optimization calculator is a powerful tool that streamlines the process of determining the best arrangement of products on a pallet. By leveraging advanced algorithms, comprehensive product databases, and visualization tools, businesses can optimize their pallet loading plans, saving time, reducing manual labor, and maximizing efficiency.
Benefits of Using a Pallet Optimization Calculator
Implementing a pallet optimization calculator in your business can yield numerous benefits. Let’s explore some of the most significant advantages:
Improving Warehouse Efficiency
By optimizing pallet loads, businesses can make the most of their available warehouse space. This optimization allows for higher storage density and easier access to products. Additionally, optimized pallet loads reduce the time required for inventory management and order fulfillment, leading to improved overall warehouse efficiency.
Reducing Shipping Costs
One of the most significant benefits of using a pallet optimization calculator is the ability to reduce shipping costs. By maximizing the number of products transported in a single shipment, businesses can lower transportation expenses and minimize the environmental impact associated with excessive carbon emissions.
Implementing a Pallet Optimization Calculator in Your Business
Now that we’ve explored the benefits of using a pallet optimization calculator, let’s examine the steps to successfully integrate this tool into your business:
Steps to Integrate a Pallet Optimization Calculator
1. Research and Select a Suitable Pallet Optimization Calculator: Begin by researching and evaluating different pallet optimization calculators available in the market. Look for a solution that aligns with your specific business needs and constraints.
2. Gather Product Data: Collect accurate and detailed product data, including dimensions, weight, and packaging requirements. This data is crucial for generating accurate loading plans.
3. Configure Constraints: Determine the specific constraints for your business, such as weight limitations, stacking requirements, and pallet dimensions. Configure these constraints into the pallet optimization calculator.
4. Training and Familiarization: Provide adequate training to your staff on how to effectively use the pallet optimization calculator. Familiarize them with its features, functionalities, and best practices.
5. Test and Refine: Conduct test runs and fine-tune the parameters of the pallet optimization calculator to ensure optimal results. Continuously refine the process based on feedback and performance metrics.
Overcoming Potential Challenges in Implementation
Implementing a pallet optimization calculator may come with certain challenges. Some common obstacles include:
- Data Accuracy: Inaccurate product data can lead to suboptimal loading plans. It’s essential to ensure that the data inputted into the calculator is accurate and up to date.
- Training and Adoption: Employees may require time to adapt to the new tool and understand its functionalities. Providing comprehensive training and ongoing support can help overcome these challenges.
- Integration with Existing Systems: Integrating a pallet optimization calculator with existing warehouse management systems or software can be complex. Ensure compatibility and seamless integration to avoid any disruptions in workflow.
Measuring the Success of Pallet Optimization
Measuring the success of pallet optimization is crucial for determining its impact on your business operations. Key performance indicators (KPIs) play a vital role in evaluating the effectiveness of your pallet optimization efforts. Let’s explore some essential KPIs to consider:
Key Performance Indicators for Pallet Optimization
1. Fill Rate: Measure the percentage of pallet space occupied by products. Aim for a higher fill rate to maximize space utilization.
2. Warehouse Space Utilization: Analyze how efficiently your warehouse space is utilized after implementing pallet optimization. Measure the percentage of available storage space utilized.
3. Shipping Cost Savings: Calculate the reduction in shipping costs by optimizing pallet loads. Compare the expenses before and after implementing a pallet optimization calculator.
Continuous Improvement in Pallet Optimization
Pallet optimization should be an ongoing process. Regularly review the performance metrics and seek opportunities for continuous improvement. Feedback from warehouse staff, customers, and suppliers is valuable in refining the pallet optimization process and ensuring sustainable efficiency gains.
By implementing a pallet optimization calculator and continually monitoring its impact, businesses can maximize efficiency, reduce costs, and enhance overall productivity. Harnessing the power of technology and automation in supply chain management is essential in today’s competitive landscape. Embrace the benefits of pallet optimization, and take your business to new heights of operational excellence.
Take Your Pallet Optimization to the Next Level
Ready to transform your Amazon business with the power of AI? Subscribe to Your eCom Agent’s AI Tools today and experience the future of product development, review analysis, and detail page enhancement. Don’t let manual processes slow you down. Join the revolution and watch your efficiency soar with the help of artificial intelligence. Your eCom Agent is your partner in maximizing productivity and profitability.