Calculating the number of pallets in a warehouse is crucial for efficient and effective management of inventory and space. By understanding warehouse capacity, the basics of pallet calculation, and the steps involved in determining pallet capacity, you can optimize your warehouse operations. Additionally, considering pallet placement and utilizing technology for pallet calculation can further enhance warehouse efficiency.
Understanding Warehouse Capacity
The first step in calculating the number of pallets in a warehouse is to have a clear understanding of the warehouse capacity. Warehouse capacity refers to the total amount of space available for storing goods and materials. It is essential to know the maximum capacity in terms of area, volume, and weight to ensure proper utilization of the warehouse.
Before we begin: Every Amazon Seller needs a suite of tools for Keyword Research, Product Development, and Listing Optimization. Our top pick is Helium 10 and readers of this post can get 20% off their first 6 months by clicking the image below.
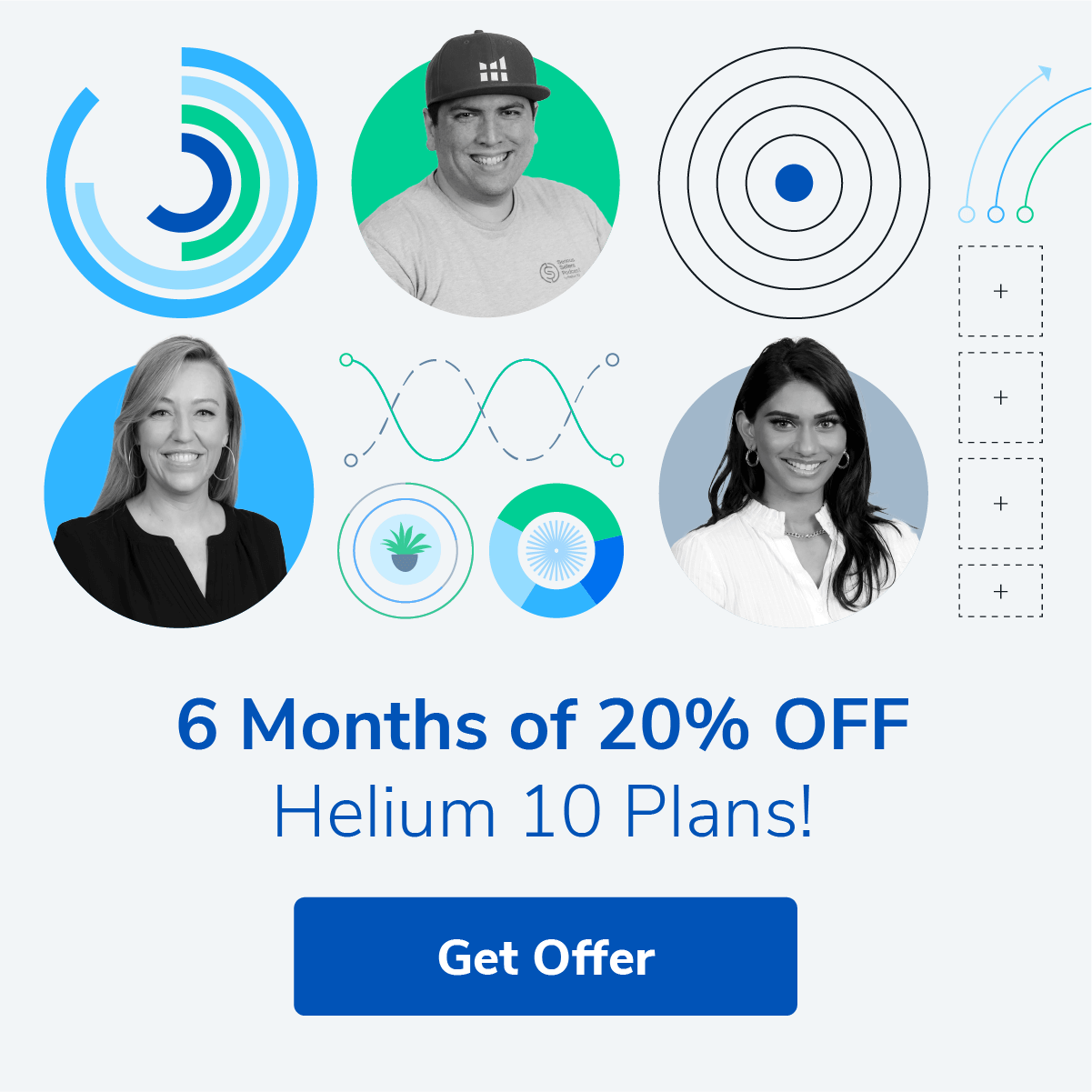
When it comes to warehouse capacity, size matters. The larger the warehouse, the more goods it can accommodate. However, it’s not just about the physical dimensions of the warehouse. Factors such as ceiling height and floor load capacity also play a crucial role in determining the overall capacity.
Warehouse layout and design are key factors that contribute to the effective utilization of space. A well-designed warehouse optimizes storage capacity by strategically placing racks, shelves, and other storage systems. By maximizing vertical space and utilizing efficient storage systems, warehouses can significantly increase their capacity.
Storage systems, such as pallet racking, play a vital role in warehouse capacity. Pallet racking allows for the stacking of goods vertically, making efficient use of space. Different types of pallet racking systems, such as selective racking, drive-in racking, and push-back racking, offer varying levels of storage density and accessibility.
Aisle width and type also impact warehouse capacity. Narrow aisles can maximize storage capacity by reducing the space required for material handling equipment. However, narrow aisles may limit accessibility and maneuverability. On the other hand, wider aisles provide more flexibility but may reduce the overall storage capacity.
The type of inventory being stored is another crucial factor in determining warehouse capacity. Different products have varying storage requirements. Some products may require specialized storage conditions, such as temperature-controlled environments or specific shelving systems. Understanding the specific needs of the inventory is essential to optimize warehouse capacity.
Efficient pallet management is vital for maintaining the overall functionality of the warehouse. Properly organizing and stacking pallets not only maximizes storage space but also facilitates material handling. By implementing effective pallet management practices, such as proper stacking techniques and regular maintenance, warehouses can ensure smooth operations and minimize the risk of accidents or damage to goods.
In conclusion, understanding warehouse capacity is crucial for effective warehouse management. Factors such as warehouse layout, storage systems, aisle width, and inventory type all contribute to determining the number of pallets a warehouse can accommodate. By optimizing these factors and implementing efficient pallet management practices, warehouses can make the most of their available space and enhance overall operational efficiency.
The Basics of Pallet Calculation
When it comes to pallet calculation, two primary aspects need to be considered: pallet size and type, and accurate measurements. The pallet size and type refer to the dimensions and design of the pallets used in the warehouse. Accurate measurements, on the other hand, involve determining the dimensions of the warehouse, including its length, width, and height.
Defining the pallet size and type is crucial for effective pallet calculation. Different industries and storage requirements may call for specific types of pallets, such as standard or customized sizes. Additionally, pallets can vary in material, such as wood, plastic, or metal. Choosing the appropriate pallet size and type ensures compatibility with storage systems and optimal usage of available space.
When considering pallet size, it is important to take into account the dimensions of the products being stored. Some products may require larger pallets to accommodate their size and weight, while others may be more efficiently stored on smaller pallets. By carefully selecting the appropriate pallet size, businesses can maximize storage capacity and minimize wasted space.
Furthermore, the type of pallet chosen can have a significant impact on the efficiency of warehouse operations. For example, some pallets may have additional features like built-in dividers or collapsible sides, which can help organize and protect the products during storage and transportation. Understanding the specific needs of the products being stored and the workflow of the warehouse can help determine the most suitable pallet type.
Accurate measurements play a significant role in calculating pallet capacity. It is essential to measure the dimensions of the warehouse with precision to ensure accurate calculations. Taking into account the length, width, and height of the warehouse accurately enables accurate determination of the number of pallet positions available for storage.
When measuring the warehouse, it is important to consider any obstructions or irregularities that may affect the available space. For example, columns, beams, or equipment may limit the usable area and need to be accounted for in the calculations. Additionally, it is essential to measure the height of the warehouse accurately, as vertical space is often underutilized in many storage facilities.
Once the dimensions of the warehouse are determined, the next step is to calculate the number of pallet positions available. This involves dividing the total available space by the size of the pallets being used. It is important to consider factors such as aisle width, safety regulations, and any specific storage requirements when determining the number of pallet positions.
Efficient pallet calculation not only maximizes storage capacity but also ensures smooth operations within the warehouse. By accurately defining the pallet size and type and taking precise measurements of the warehouse, businesses can optimize their storage systems and effectively utilize the available space. This leads to improved inventory management, increased productivity, and ultimately, enhanced customer satisfaction.
Steps to Calculate Pallet Capacity
Calculating pallet capacity involves specific steps that help determine the precise number of pallets a warehouse can accommodate. These steps include measuring warehouse dimensions, calculating pallet positions, and considering additional factors that may affect pallet storage.
To measure warehouse dimensions, start by measuring the length, width, and height of the warehouse. Use a measuring tape or laser measurement tools for accuracy. Take multiple measurements at different points to account for any irregularities in the warehouse structure. It is important to ensure that the measurements are precise and reflect the actual size of the warehouse.
Once the warehouse dimensions are obtained, the next step is to calculate pallet positions. Pallet positions refer to the number of spots available for pallet storage. Divide the warehouse volume by the volume occupied by each pallet position to determine the total number of pallet positions. This calculation requires accurate measurements of the warehouse dimensions and the dimensions of each pallet position.
In addition to measuring the warehouse dimensions and calculating pallet positions, it is essential to consider other factors that may affect pallet storage capacity. These factors include the type of pallets used, the layout of the warehouse, and any obstructions or restrictions that may limit the number of pallets that can be stored.
The type of pallets used can impact the overall capacity of the warehouse. Different types of pallets have varying dimensions and weight capacities, which can affect how many pallets can be stored in a given space. It is important to consider the specific dimensions and weight limits of the pallets being used when calculating pallet capacity.
The layout of the warehouse also plays a crucial role in determining pallet capacity. Efficient use of space, such as utilizing vertical storage options or optimizing aisle widths, can significantly increase the number of pallets that can be stored. Additionally, considering the flow of goods and accessibility to pallets can help maximize storage capacity.
Furthermore, any obstructions or restrictions within the warehouse must be taken into account. These can include columns, support beams, or equipment that may limit the available space for pallet storage. It is important to carefully assess the warehouse layout and identify any potential obstacles that may impact pallet capacity.
By considering these additional factors along with measuring warehouse dimensions and calculating pallet positions, a more comprehensive understanding of pallet capacity can be achieved. This detailed analysis will provide warehouse managers with valuable insights to optimize storage space and efficiently utilize pallet storage within their facilities.
Considerations for Pallet Placement
Pallet placement within the warehouse should adhere to safety regulations and maximize space utilization. Following safety regulations for pallet stacking is crucial to prevent accidents and damage to goods. Consider factors such as pallet weight limits, stacking heights, and rack load capacities when determining the placement of pallets. Adhering to safety regulations ensures a safe working environment and protects goods from the risk of damage or collapse.
Efficient pallet placement enables maximum space utilization in the warehouse. This can be achieved by optimizing the layout of pallet racks, utilizing stacking techniques, and implementing effective material handling strategies. Employing efficient pallet placement practices ensures smooth workflow, minimizes wasted space, and increases overall productivity.
Using Technology for Pallet Calculation
The advent of technology has revolutionized warehouse management, including pallet calculation. Warehouse Management Systems (WMS) are computerized systems that integrate various warehouse functions and processes. These systems enable accurate and efficient warehouse management, including pallet calculation.
Using pallet calculation software simplifies the process of determining pallet capacity. These software programs utilize algorithms and database systems to calculate the exact number of pallets a warehouse can accommodate based on its dimensions and storage requirements. Pallet calculation software streamlines the calculation process and eliminates human error, resulting in accurate and reliable results.
Utilizing technology for pallet calculation not only saves time and effort but also provides valuable insights into optimizing warehouse operations. WMS and pallet calculation software enable real-time tracking, inventory management, and analysis, allowing warehouse managers to make informed decisions for efficient resource allocation and warehouse utilization.
Benefits of Using Pallet Calculation Software:
- Accurate and reliable calculations
- Time-saving and efficient
- Real-time tracking and analysis
- Optimization of warehouse operations
- Informed decision-making for resource allocation
In conclusion, calculating the number of pallets in a warehouse requires a thorough understanding of warehouse capacity, the basics of pallet calculation, and the steps involved in determining pallet capacity. Considering pallet placement and utilizing technology for pallet calculation further enhances warehouse efficiency. By implementing these practices, warehouse managers can optimize space utilization, streamline material handling processes, and ensure smooth operations for better productivity and profitability.
Optimize Your Amazon Operations with Your eCom Agent
Maximizing warehouse efficiency is just the beginning. As an Amazon Seller, you can take your business to the next level with Your eCom Agent’s suite of AI tools. Streamline your product development, dive deep into customer feedback, and enhance your detail pages with the power of artificial intelligence. Don’t spend hours on tasks that can be automated in seconds. Subscribe to Your eCom Agent’s AI Tools today and transform the way you manage your Amazon operations.