Pallet racking systems are essential for efficient storage and organization in warehouses and industrial settings. However, before investing in such systems, it is crucial to understand the costs involved. By calculating pallet racking costs accurately, you can make informed decisions and optimize your budget. In this article, we will guide you through the process of calculating pallet racking costs, highlight additional expenses to consider, and provide tips on reducing these costs.
Understanding Pallet Racking Costs
Pallet racking refers to the shelving system used to store and stack pallets. It is commonly used to maximize storage space while allowing easy access to inventory. The cost of pallet racking depends on various factors, including the type of racking, size of the storage area, and additional features required. To accurately estimate the costs, it is crucial to consider these influencing factors.
Before we begin: Every Amazon Seller needs a suite of tools for Keyword Research, Product Development, and Listing Optimization. Our top pick is Helium 10 and readers of this post can get 20% off their first 6 months by clicking the image below.
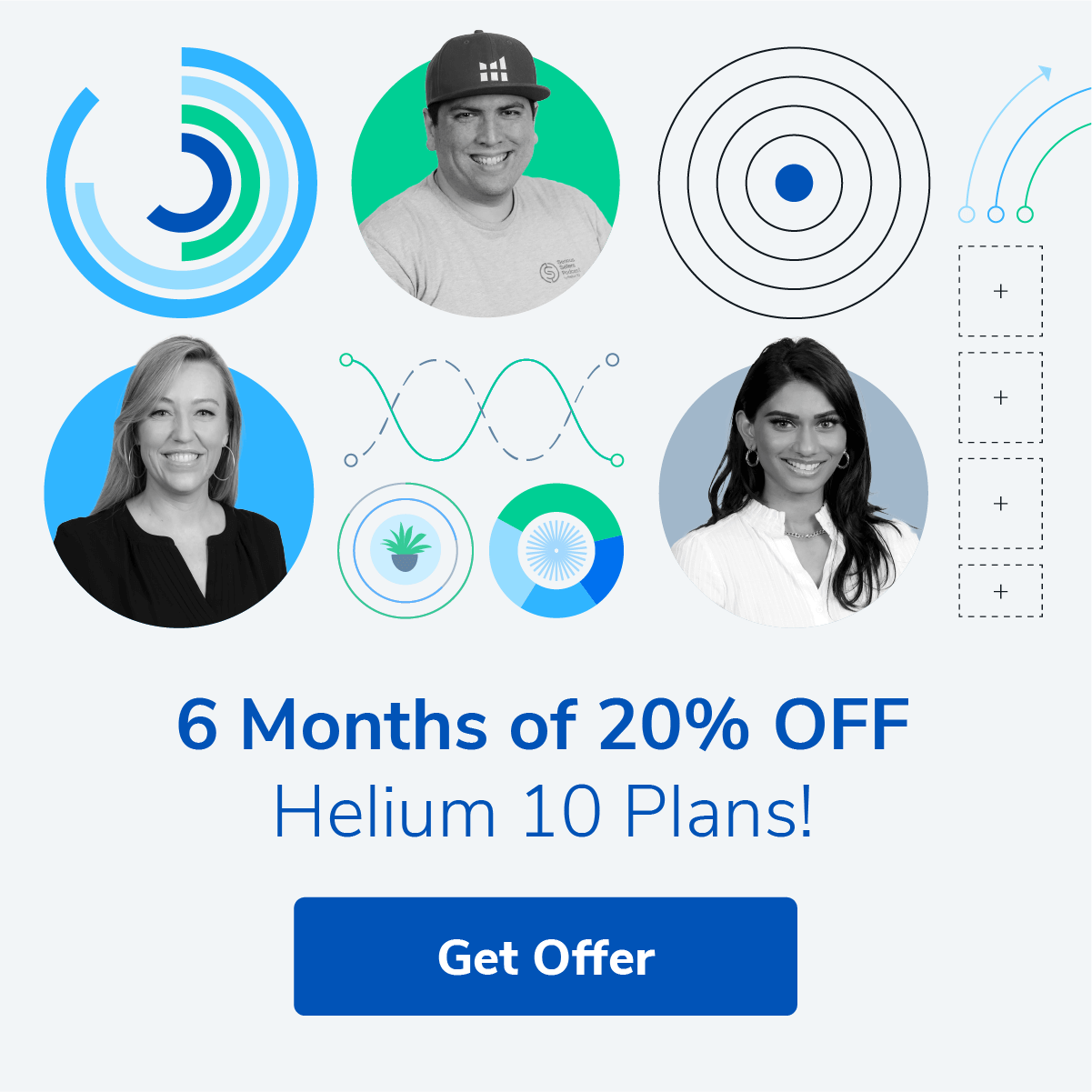
Defining Pallet Racking
Pallet racking comes in various types, including selective racking, drive-in racking, and push-back racking. Each type has unique features and benefits, along with different costs. Understanding the specific requirements of your business and the benefits offered by each type will help you make an informed decision.
Let’s dive deeper into the different types of pallet racking:
Selective Racking:
Selective racking is the most common type of pallet racking system. It allows for direct access to each pallet, making it ideal for businesses that require quick and easy retrieval of inventory. This type of racking is cost-effective and versatile, making it suitable for a wide range of industries.
Drive-In Racking:
Drive-in racking is designed for high-density storage, where forklifts can drive directly into the racking system to place or retrieve pallets. This type of racking maximizes storage space by eliminating aisles, but it may have a higher initial cost due to its specialized design. Drive-in racking is commonly used in warehouses with a large volume of the same product.
Push-Back Racking:
Push-back racking is a dynamic storage system that allows for the storage of multiple pallets in a single lane. Pallets are loaded from one side and pushed back by subsequent pallets, creating a gravity flow system. This type of racking offers high storage density and efficient use of space, but it may have a higher cost due to its complexity and additional components.
Factors Influencing Pallet Racking Costs
The major factors influencing pallet racking costs include:
- Size of the storage area: The larger the storage area, the more materials and labor will be required, affecting the overall cost. A larger storage area may also require additional racking components, such as beams and uprights, to support the weight of the inventory.
- Weight capacity: If you need to store heavier items, the racking system’s weight capacity will impact both the design and cost. Racking systems with higher weight capacities often require thicker beams and stronger uprights, which can increase the overall cost.
- Customization and additional features: Additional accessories and customization options, such as wire decking or safety measures, can increase the overall cost. These features enhance the functionality and safety of the racking system, but they may come at an additional expense.
- Installation location: The cost may vary based on factors like the site’s accessibility, floor condition, and environmental considerations. If the installation site is difficult to access or requires additional preparation work, it may result in higher installation costs.
By considering these factors, you can better estimate the costs associated with pallet racking. It is important to work with a reputable supplier or contractor who can assess your specific needs and provide a detailed cost breakdown. Remember, investing in a well-designed and efficient pallet racking system can greatly improve your storage capabilities and overall operational efficiency.
Steps to Calculate Pallet Racking Costs
Calculating pallet racking costs can be broken down into three key steps:
Determining Your Storage Needs
Thoroughly assess your inventory and consider its current and future growth patterns. Take into account the different types of products you store, such as perishable goods, fragile items, or heavy machinery. Determine the number of pallets to be stored, their dimensions, and weight. This information will help you understand the specific requirements of your storage facility and enable you to choose the most suitable racking system.
For example, if you store perishable goods, you may need a racking system that allows for proper ventilation and easy access for rotation. On the other hand, if you store fragile items, you may require a racking system that provides extra protection and stability.
Additionally, consider the future growth of your inventory. Will you be expanding your product range or increasing the volume of your existing products? By anticipating future growth, you can ensure that the racking system you choose can accommodate your evolving storage needs.
Selecting the Right Type of Pallet Racking
Based on your storage needs, select the most suitable type of pallet racking. There are various types available, each with its own advantages and considerations.
For example, selective pallet racking is the most common type and provides easy access to each pallet. It is ideal for facilities that require frequent inventory rotation. On the other hand, drive-in pallet racking allows for high-density storage, making it suitable for storing large quantities of the same product.
Consider factors such as accessibility requirements, the type of products being stored, and budget constraints. If you have limited space, you may opt for narrow aisle racking to maximize storage capacity. If you need quick and direct access to each pallet, push-back racking may be the best choice.
Furthermore, take into account the durability and quality of the racking system. Investing in high-quality racking will ensure the safety of your inventory and minimize the risk of accidents or damage.
Calculating the Number of Pallet Positions
Once you have determined the type of pallet racking that suits your needs, it is time to calculate the number of pallet positions required.
Consider the size and weight of your inventory to determine the optimal configuration of the racking system. This will help you make the most efficient use of the available space and ensure that you have enough capacity to store your inventory.
Take into account potential future growth and changes in your inventory. If you anticipate an increase in the number of pallets or the size of your products, it is important to factor that into your calculations. By considering future growth, you can avoid the need for costly modifications or expansions in the near future.
Additionally, consider the layout of your storage facility. Are there any obstacles or constraints that may affect the installation of the racking system? Take measurements and consider any limitations to ensure a smooth and efficient installation process.
By following these steps and carefully considering your storage needs, selecting the right type of pallet racking, and calculating the number of pallet positions required, you can accurately estimate the costs associated with implementing a pallet racking system in your facility.
Additional Costs to Consider
While calculating pallet racking costs, it is crucial to consider additional expenses that may arise:
Installation and Labor Costs
The cost of professional installation and labor can significantly impact your budget. Hiring experienced installers ensures that the racking system is properly assembled and safe to use.
During the installation process, it is important to consider the time and effort required to set up the pallet racking system. Depending on the complexity of the design and the size of the warehouse, the labor costs can vary. Additionally, if there are any unforeseen challenges or obstacles during the installation, it may require additional labor and incur extra expenses.
Furthermore, it is essential to factor in the cost of any necessary equipment or tools that may be required for the installation. This can include items such as forklifts, cranes, or other specialized machinery.
Maintenance and Repair Costs
Regular maintenance and occasional repairs are necessary for the longevity and safety of your pallet racking system. Consider budgeting for these costs to ensure optimal performance.
Maintenance costs can include routine inspections, cleaning, and lubrication of the racking system. It is important to allocate funds for these activities to prevent any potential issues or damages that may arise from neglecting maintenance.
In addition to regular maintenance, there may be unforeseen repair costs that need to be considered. Over time, wear and tear or accidental damage can occur to the pallet racking system. It is crucial to have a contingency plan and allocate funds for any necessary repairs to minimize downtime and maintain the safety of your warehouse operations.
Safety and Compliance Costs
Compliance with safety regulations is essential in warehouse operations. Investing in safety features and regular inspections can incur additional costs but are necessary to protect your employees and inventory.
Ensuring the safety of your employees should be a top priority. This may involve investing in safety features such as safety barriers, guardrails, or anti-collapse mesh to prevent accidents and injuries. These safety measures not only protect your employees but also help in avoiding potential legal consequences and liabilities.
Regular inspections by certified professionals are crucial to identify any potential safety hazards or non-compliance issues. Allocating funds for these inspections is necessary to maintain a safe working environment and ensure that your pallet racking system meets all the necessary safety standards and regulations.
Moreover, it is important to consider the cost of safety training for your employees. Providing proper training on how to use the pallet racking system safely can prevent accidents and minimize the risk of damage to your inventory.
How to Reduce Pallet Racking Costs
While pallet racking costs are essential to consider, there are ways to optimize your expenses:
Efficient Design and Layout
By analyzing your storage needs and optimizing the design and layout of your racking system, you can maximize space utilization and reduce unnecessary costs. Utilize software tools or consult with experts to create an efficient design.
Quality vs. Cost Considerations
Although cost is important, remember that investing in high-quality pallet racking can save you money in the long run. Durable and well-designed racking systems require fewer repairs and replacements, resulting in lower maintenance costs.
Long-Term Cost Savings Strategies
Implementing strategies like proper inventory management, organized stacking, and routine maintenance can help prolong the lifespan of your racking system and minimize operational costs over time.
By following the steps outlined in this article and considering the influencing factors and additional costs, you can accurately calculate pallet racking costs. Making informed decisions and implementing cost-saving strategies will ensure efficient storage while optimizing your budget.
Optimize Your Amazon Operations with Your eCom Agent
As you consider the efficiency and cost-effectiveness of your warehouse storage solutions, don’t forget the importance of streamlining your online business operations. Your eCom Agent offers a powerful suite of AI tools designed specifically for Amazon Sellers. From developing standout products to analyzing customer feedback and enhancing your detail pages, our AI-driven platform can transform hours of manual work into seconds of automated precision. Ready to revolutionize your Amazon business? Subscribe to Your eCom Agent’s AI Tools today and take the first step towards smarter selling.