In today’s fast-paced e-commerce landscape, efficient inventory management is crucial for the success of any business. One key aspect of this is barcode labeling, which allows for quick and accurate identification of products. However, many sellers overlook the importance of barcode label size in the FBA (Fulfillment by Amazon) program. Understanding this crucial factor can greatly optimize your inventory management process.
Understanding the Importance of Barcode Label Size in FBA
Barcode labels play a vital role in inventory management. They provide unique identifiers for each product, enabling seamless tracking and control of your inventory. When it comes to FBA, where Amazon handles the fulfillment process, barcode labels are essential for efficient operations.
Before we begin: Every Amazon Seller needs a suite of tools for Keyword Research, Product Development, and Listing Optimization. Our top pick is Helium 10 and readers of this post can get 20% off their first 6 months by clicking the image below.
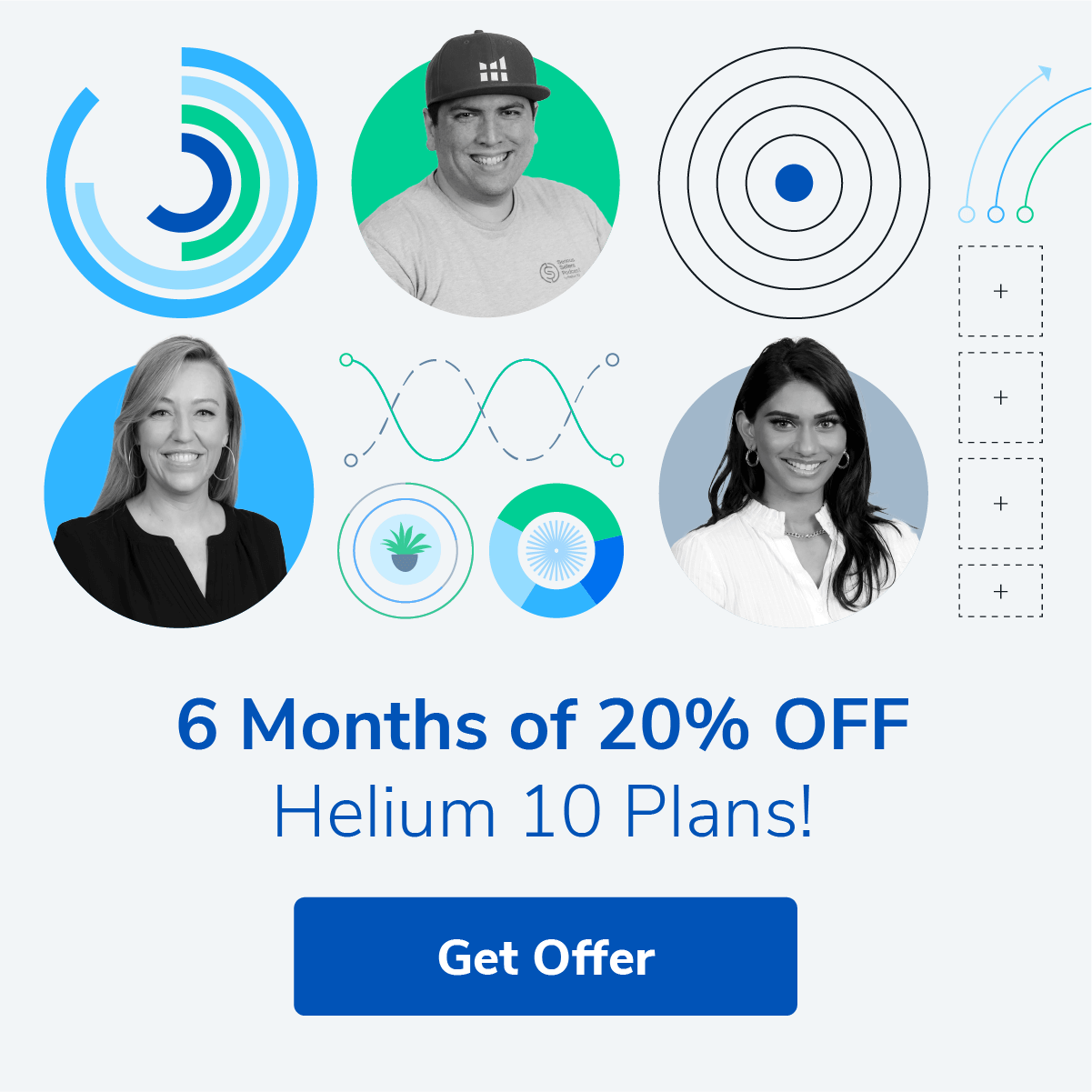
Barcode labels act as the bridge between your physical products and the digital inventory system. By scanning these labels, Amazon’s fulfillment centers can quickly identify and process your products. This streamlines the entire fulfillment process, from receiving your inventory to shipping it to customers.
But have you ever wondered why the size of barcode labels matters? Well, let’s dive into the details.
The Role of Barcode Labels in Inventory Management
Barcode labels are not just simple stickers with random patterns. They contain encoded information that represents various product details, such as the SKU (stock keeping unit), product name, and other relevant information. These labels act as a communication tool between your inventory and the fulfillment centers.
Imagine a scenario where barcode labels are too small or illegible. In such cases, the scanning process becomes challenging, leading to errors and delays in inventory management. This can result in misplacements, lost items, and ultimately, dissatisfied customers.
On the other hand, properly sized barcode labels ensure that the scanning process is smooth and efficient. The recommended barcode label size for FBA is 2 by 1 inches. This size strikes a balance between legibility and space efficiency, ensuring that labels can be easily scanned and fit well on various packaging materials.
Why Size Matters in Barcode Labeling
While barcode labels might seem like a minor detail, their size can have a significant impact on efficiency. Let’s explore why size matters in barcode labeling.
Firstly, larger barcode labels may take up more space on your packaging materials. This can be problematic if you have limited space or if you want to include other important information, such as product descriptions or branding elements. By adhering to the recommended size, you can optimize the use of space and maintain a clean and professional look for your products.
Secondly, smaller barcode labels can be challenging to scan accurately. If the labels are too small, the scanning devices may struggle to read the barcode, leading to errors and delays. This can result in additional time spent on manual data entry or even the need for re-labeling, which can be a time-consuming and costly process.
Lastly, consider the ease of scanning for the fulfillment center employees. They handle a large volume of packages daily, and having easily scannable barcode labels can significantly speed up their workflow. By using the recommended size, you contribute to a smoother and more efficient process, reducing the chances of errors and ensuring timely deliveries to your customers.
In conclusion, barcode label size plays a crucial role in FBA inventory management. By adhering to the recommended size, you can optimize efficiency, reduce errors, and ensure a seamless fulfillment process. So, make sure to consider the size of your barcode labels and reap the benefits of streamlined operations.
Decoding the Amazon FBA Barcode Label Requirements
Amazon has specific guidelines for barcode labels within the FBA program. Adhering to these requirements is crucial to ensure smooth operations and prevent delays or penalties.
When it comes to selling products on Amazon, one of the most important aspects is ensuring that your products have the correct barcode labels. These labels play a vital role in the fulfillment process, allowing Amazon’s systems to accurately track and manage inventory. Without proper barcode labels, your products may face difficulties in being processed and shipped to customers.
Amazon’s Guidelines for Barcode Labels
According to Amazon’s guidelines, barcode labels must be easily scannable and legible. This means that the labels should have a white background with black bars and numbers. The contrast between the background and the bars/numbers is essential for barcode scanners to accurately read the information encoded within the barcode.
In addition to the color requirements, Amazon also emphasizes the importance of proper label placement. Barcode labels should be placed on a flat, smooth surface with no obstructions. This ensures that the barcode scanners can easily capture the barcode information without any interference. Placing the labels on uneven or textured surfaces can lead to scanning errors and delays in processing.
The Consequences of Non-compliance with FBA Barcode Requirements
Failing to comply with Amazon’s barcode label requirements can lead to various issues. Non-compliant labels can result in misreads or failures during scanning, disrupting the fulfillment process. This can lead to delays in processing and shipping, which can ultimately impact customer satisfaction.
Furthermore, inconsistent label sizes can also cause confusion and delays. Amazon’s fulfillment centers are designed to handle products efficiently based on standardized label sizes. If your barcode labels deviate from these standards, it can cause confusion and potentially result in your products being misplaced or misrouted within the fulfillment center.
It is important to note that Amazon takes barcode label compliance seriously. Failure to comply with the requirements may result in penalties or even the suspension of your selling privileges. Therefore, it is crucial to familiarize yourself with Amazon’s guidelines and ensure that your barcode labels meet the specified requirements.
In conclusion, understanding and adhering to Amazon’s FBA barcode label requirements is essential for a successful selling experience on the platform. By following these guidelines, you can ensure that your products are processed efficiently, reducing the risk of delays or penalties, and ultimately providing a positive customer experience.
Determining the Optimal Barcode Label Size for FBA
Choosing the right barcode label size for your FBA inventory involves considering various factors that can impact efficiency and accuracy.
When determining the optimal barcode label size, consider factors such as the size of your product packaging, the available space for labeling, and the scanning equipment to be used. Balancing these factors will help you find the right size that fits within Amazon’s guidelines and works seamlessly with your specific products.
One important factor to consider is the size of your product packaging. If your packaging is small, you may need to choose a smaller barcode label size to ensure it fits properly. On the other hand, if your packaging is large, you may have more flexibility in choosing a larger barcode label size.
Another factor to consider is the available space for labeling. Some products may have limited space for barcode labels, especially if there are other important product information or branding elements that need to be included on the packaging. In such cases, you may need to choose a smaller barcode label size to accommodate all the necessary information.
The scanning equipment to be used is also an important consideration. Different scanners may have different requirements in terms of barcode label size. It is crucial to ensure that the barcode labels you choose can be easily scanned by the equipment you have or plan to use. Labels that are too small or too large can result in scanning errors or even complete failures. A label that is too small may be difficult to scan accurately, while a label that is too large may not fit properly in the scanning equipment. Striking the right balance is essential for seamless scanning and inventory management.
Additionally, it is important to adhere to Amazon’s guidelines for barcode label size. Amazon has specific requirements for the size and placement of barcode labels on FBA inventory. By choosing a barcode label size that meets these guidelines, you can ensure smooth processing and avoid any potential issues or delays.
Overall, determining the optimal barcode label size for your FBA inventory involves considering factors such as the size of your product packaging, the available space for labeling, the scanning equipment to be used, and Amazon’s guidelines. By carefully balancing these factors, you can find the right size that promotes efficiency, accuracy, and seamless inventory management.
Implementing Efficient Barcode Labeling in Your FBA Business
To optimize your FBA inventory management, it’s important to implement efficient barcode labeling practices throughout your business operations.
Choosing the Right Barcode Label Printer
Investing in a high-quality barcode label printer is essential for producing clear and readable labels. Look for printers that offer the necessary resolution and printing speed to meet your business’s specific requirements. Additionally, ensure compatibility with Amazon’s barcode label specifications for seamless integration.
Best Practices for Barcode Label Placement
The placement of barcode labels is critical for efficient scanning. Labels should be affixed to flat, clean surfaces that are easily accessible to scanning equipment. Avoid placing labels on curved or irregular surfaces, as this can lead to scanning issues. By following these best practices, you can significantly improve the accuracy and speed of your FBA barcode scanning process.
The Future of Barcode Labeling in FBA Inventory Management
As technology continues to advance, so too will barcode labeling methods and standards. It’s important to stay ahead of the curve and prepare for future changes in FBA barcode labeling regulations.
Technological Advances in Barcode Labeling
New advancements, such as RFID (Radio Frequency Identification) technology, are revolutionizing inventory management. RFID tags can store and transmit information wirelessly, offering potential benefits for FBA businesses. Keeping an eye on these advancements can help you stay at the forefront of barcode labeling efficiency.
Preparing for Changes in FBA Barcode Labeling Regulations
Regulations and requirements for FBA barcode labeling may evolve over time. As a responsible seller, it is crucial to stay informed about any updates or changes in Amazon’s guidelines. By staying proactive and adapting to new requirements, you can ensure a smooth and efficient FBA inventory management process.
In conclusion, selecting the optimal barcode label size for FBA can greatly enhance your inventory management efficiency. By understanding the importance of barcode labels, decoding Amazon’s requirements, determining the right size, implementing efficient practices, and preparing for future changes, you can stay one step ahead in the fast-paced world of e-commerce. So, take the time to optimize your barcode labeling process and reap the benefits of efficient FBA inventory management.
Streamline Your FBA Inventory Management with AI
Ready to take your FBA inventory management to the next level? Subscribe to Your eCom Agent’s AI Tools and harness the power of artificial intelligence to optimize your Amazon business. From product development to review analysis and detail page enhancement, Your eCom Agent provides the cutting-edge tools you need to succeed. Don’t let manual processes slow you down—let AI do the heavy lifting and save you hours of work. Subscribe now and transform your inventory management today!