Fulfillment centers play a crucial role in the world of e-commerce, ensuring that products are efficiently and accurately delivered to customers. In order to understand how fulfillment centers work, it is important to grasp the basics of their operations, the key components involved, and the technology that drives their efficiency. Additionally, we will explore the benefits of utilizing a fulfillment center for your business as well as the challenges that arise in their day-to-day operations.
Understanding the Basics of Fulfillment Centers
Fulfillment centers are strategically designed facilities that house inventory, process orders, and manage the entire logistics of product delivery. These centers act as the backbone of e-commerce operations, allowing businesses to focus on their core competencies while leaving the complex process of order fulfillment to the experts.
Before we begin: Every Amazon Seller needs a suite of tools for Keyword Research, Product Development, and Listing Optimization. Our top pick is Helium 10 and readers of this post can get 20% off their first 6 months by clicking the image below.
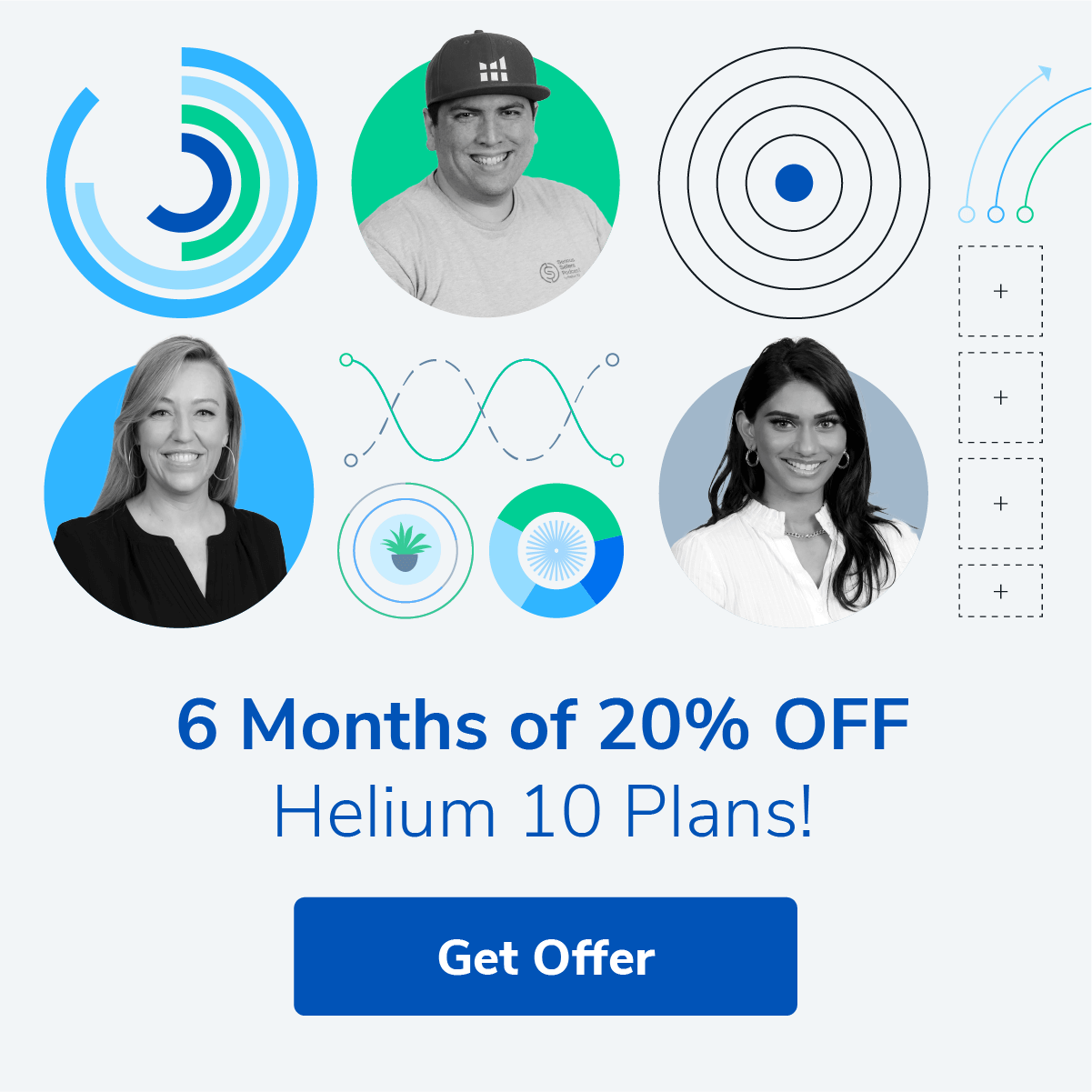
When it comes to e-commerce, the success of a business heavily relies on the efficiency and effectiveness of its fulfillment center. From receiving inventory to shipping out orders, every step in the process must be carefully managed to ensure customer satisfaction and business growth.
One of the primary roles that fulfillment centers play in the world of e-commerce is the storage and management of inventory. These centers have dedicated warehousing space to safely store products until they are ready to be shipped. By having a centralized location for inventory, businesses can optimize space, reduce costs, and ensure efficient order processing.
Imagine a massive warehouse, filled with rows upon rows of neatly stacked shelves. Each shelf is meticulously organized, with products arranged in a logical and systematic manner. This level of organization is crucial to ensure that every item can be easily located when an order is placed.
But it’s not just about storage. Fulfillment centers also utilize advanced inventory management systems to keep track of every single item in their inventory. These systems use sophisticated algorithms and real-time data to monitor stock levels, track product movement, and generate accurate reports. This level of visibility allows businesses to make informed decisions about inventory replenishment, preventing stockouts and minimizing excess inventory.
The Role of Fulfillment Centers in E-commerce
Aside from inventory management, fulfillment centers also play a crucial role in order processing and fulfillment. When a customer places an order on an e-commerce website, it triggers a series of actions within the fulfillment center.
First, the order is received and verified. This involves checking the customer’s details, ensuring that the product is in stock, and confirming payment. Once the order is verified, it moves on to the next stage: picking and packing.
Picking and packing is a meticulous process that involves retrieving the ordered items from their designated locations, carefully packaging them to ensure safe transportation, and labeling the packages with the necessary shipping information. Fulfillment centers often employ advanced automation technologies, such as conveyor belts and robotic arms, to expedite this process and minimize errors.
Once the order is picked and packed, it is ready for shipping. Fulfillment centers work closely with shipping carriers to arrange for timely and cost-effective delivery. They generate shipping labels, schedule pickups, and track the progress of each shipment. This end-to-end management of the logistics ensures that orders are delivered to customers in a timely manner, enhancing the overall shopping experience.
Key Components of a Fulfillment Center
A fulfillment center comprises several key components that work in unison to streamline operations. These include inventory management systems, automated order processing, and shipping logistics. Let’s take a closer look at each of these components.
Inventory management systems are the backbone of any fulfillment center. These systems provide real-time visibility into inventory levels, allowing businesses to accurately track stock, monitor product movement, and generate reports. By having a comprehensive view of their inventory, businesses can make informed decisions about stock replenishment, preventing stockouts and minimizing excess inventory.
Automated order processing is another critical component of a fulfillment center. With the help of advanced software and machinery, orders can be received, verified, and processed with minimal human intervention. This not only speeds up the order fulfillment process but also reduces the likelihood of errors and improves overall accuracy.
Shipping logistics is the final piece of the puzzle. Fulfillment centers work closely with shipping carriers to ensure that orders are delivered to customers in a timely and cost-effective manner. They handle everything from generating shipping labels to scheduling pickups and tracking shipments. By managing the entire shipping process, fulfillment centers take the burden off businesses, allowing them to focus on other aspects of their operations.
In conclusion, fulfillment centers are the unsung heroes of the e-commerce world. They provide the infrastructure, expertise, and technology needed to efficiently manage inventory, process orders, and deliver products to customers. Without these centers, the world of online shopping would not be as seamless and convenient as it is today.
The Process of Order Fulfillment
The process of order fulfillment within a fulfillment center involves several steps, starting from the receipt of inventory to the final delivery of products to customers. Let’s delve into each step of this process.
Receiving and Warehousing Inventory
Upon arrival, incoming inventory is thoroughly inspected for accuracy and quality. Skilled warehouse personnel carefully examine each item, checking for any damage or discrepancies. This meticulous inspection ensures that only the highest quality products are accepted into the fulfillment center’s inventory.
Once approved, the products are stored in dedicated areas within the fulfillment center based on their specific attributes and demand patterns. Advanced inventory management systems are utilized to efficiently organize and track the vast array of products. These systems employ sophisticated algorithms that optimize the placement of items, ensuring that popular products are easily accessible and less popular ones are stored in less prominent areas.
Efficient warehousing practices further enhance the order fulfillment process. The fulfillment center employs a team of skilled warehouse personnel who are trained in efficient inventory management techniques. They utilize specialized equipment, such as forklifts and conveyor belts, to quickly and safely move products within the warehouse. This streamlined approach minimizes the time required to locate and retrieve items, ultimately speeding up the fulfillment process.
Order Processing and Packaging
When an order is placed, the fulfillment center’s systems kick into action. The order details are processed with utmost precision, ensuring that all relevant information is accurately recorded. These systems seamlessly integrate with the inventory management software, allowing for real-time updates on product availability.
Once the order details have been processed, the necessary items are retrieved from the inventory. Warehouse personnel meticulously pick the products, double-checking each item to ensure accuracy. This attention to detail guarantees that customers receive exactly what they ordered, without any errors or substitutions.
After the picking process, the products are carefully packed to ensure their safe transit. The fulfillment center employs a variety of packaging materials, such as bubble wrap, packing peanuts, and sturdy boxes, to protect the products from any potential damage during transportation. Additionally, eco-friendly packaging solutions are utilized to minimize waste and promote sustainability.
Shipping and Delivery
Once the order is packed and ready, it is handed off to delivery partners, such as postal services or courier companies, for final transportation to the customer’s address. Fulfillment centers collaborate closely with these partners to ensure efficient and timely delivery.
Before the packages are dispatched, the fulfillment center’s staff carefully prepares the necessary shipping documentation. This includes generating shipping labels, customs forms (if applicable), and any other required paperwork. By meticulously completing these tasks, the fulfillment center ensures a smooth handover to the delivery partners, minimizing any potential delays or complications.
Throughout the shipping process, the fulfillment center maintains constant communication with the delivery partners. This allows for real-time tracking of the packages, enabling customers to keep tabs on their order’s progress. The tracking information is shared with the customer, either through email notifications or an online tracking portal, providing them with peace of mind and transparency regarding their package’s whereabouts.
In conclusion, the process of order fulfillment within a fulfillment center is a carefully orchestrated series of steps. From receiving and warehousing inventory to order processing, packaging, and finally shipping and delivery, each stage is meticulously executed to ensure customer satisfaction. By employing advanced technologies, efficient practices, and a dedicated workforce, fulfillment centers play a crucial role in delivering products to customers in a timely and efficient manner.
The Technology Behind Fulfillment Centers
To manage the complex operations of a fulfillment center, advanced technology is leveraged to drive efficiency and accuracy.
Inventory Management Systems
Inventory management systems play a crucial role in tracking and managing the vast inventory housed within a fulfillment center. These systems utilize real-time data to provide businesses with accurate information on stock levels, enabling them to make informed decisions regarding purchasing and restocking.
Automation in Fulfillment Centers
Automation is the driving force behind the speed and precision of fulfillment center operations. From automated picking robots to conveyor belts, advanced technologies are employed to optimize efficiency, minimize errors, and reduce labor costs. Automation not only improves overall productivity but also allows for scalability as order volumes increase.
The Benefits of Using a Fulfillment Center
Utilizing a fulfillment center can bring numerous benefits to businesses operating in the e-commerce space.
Efficiency and Speed
Fulfillment centers are designed to streamline operations, resulting in faster order processing and shipping times. By utilizing their expertise in logistics and efficient warehousing practices, businesses can deliver products to customers in a timely manner, enhancing customer satisfaction and loyalty.
Cost-Effectiveness
Outsourcing order fulfillment to a specialized center can be cost-effective for businesses, particularly smaller ones. Fulfillment centers have the scale and expertise to negotiate favorable shipping rates, access discounted packaging materials, and optimize inventory storage, resulting in cost savings for businesses.
Scalability and Flexibility
Fulfillment centers offer businesses the flexibility to scale their operations rapidly. As order volumes increase, fulfillment centers can readily handle the higher demand without the need for major infrastructure investments. This scalability allows businesses to focus on growth and expansion rather than worrying about the logistics of order fulfillment.
Challenges in Fulfillment Center Operations
While fulfillment centers are integral to successful e-commerce operations, they do come with their own set of challenges.
Managing High Volume Orders
As businesses experience growth, managing high volume orders can become a challenge for fulfillment centers. Balancing the increased demand while maintaining efficiency and accuracy requires careful planning and investment in the right technology and workforce.
Dealing with Returns and Exchanges
Returns and exchanges are an inevitable part of e-commerce. Fulfillment centers must have robust processes in place to handle these instances promptly and efficiently. From inspecting returned items to processing refunds or replacements, a smooth returns management system is essential to maintain customer satisfaction.
In conclusion, fulfillment centers play a vital role in the e-commerce industry, providing businesses with the infrastructure, technology, and expertise needed to efficiently manage order fulfillment. Their seamless integration of key components, utilization of advanced technology, and ability to provide numerous benefits make them invaluable for businesses seeking to optimize their operations and enhance customer satisfaction. However, it is crucial to be aware of the challenges that may arise in fulfillment center operations and actively work towards addressing them to ensure continued success in e-commerce.
Optimize Your Amazon Sales with Your eCom Agent
As you navigate the complexities of fulfillment centers and strive to enhance your e-commerce operations, Your eCom Agent is here to empower your Amazon business. With our cutting-edge AI tools, you can effortlessly develop superior products, analyze customer feedback, and refine your product detail pages. Embrace the future of e-commerce and subscribe to Your eCom Agent’s AI Tools today to transform hours of work into seconds of smart, automated decision-making.